L’avenir de la flottationLes technologies de flottation deviennent plus stratégiques, écoénergétiques et performantes
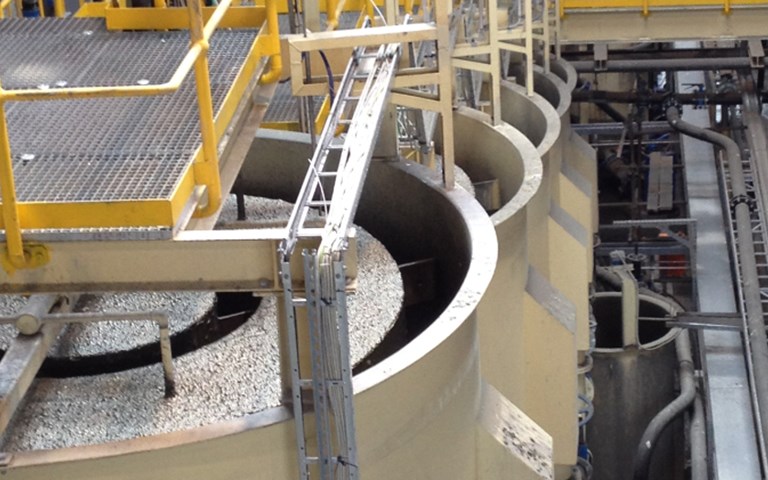
En matière de critères de conception, il est bien audacieux de proclamer pouvoir éliminer la couche d’écume dans la méthode de flottation par mousse. Pourtant, un tel dispositif existe, et on en trouve d’ailleurs près de 50 unités actuellement en exploitation, ce qui vient attester de la pression imposée sur l’industrie pour trouver de nouvelles solutions aux difficultés auxquelles elle est confrontée de nos jours. Faibles teneurs, minerais complexes et hausse des coûts de l’énergie : ces facteurs ont engendré le développement de toutes nouvelles cuves de flottation et incité à porter des améliorations aux technologies existantes ainsi qu’à adopter de nouveaux modes de réflexion quant aux schémas de traitement par flottation.
Une cuve de flottation sans écume a été mise au point par le service Flottation d’Eriez, qui l’a brevetée en 2002 et l’a commercialisée sous le nom d’HydroFloat. Elle est spécifiquement conçue pour un schéma de traitement innovant qui aborde l’un des plus gros problèmes que rencontrent les exploitations minières : la quantité de tonnes à traiter et de minerai à grains fins étant toujours plus grande, la comminution requiert toujours plus d’énergie. Si les circuits de flottation parvenaient à gérer les particules plus grossières, on pourrait économiser de l’énergie dans le circuit de comminution.
« La plupart des sociétés minières se trouvent confrontées à un déclin des teneurs des minerais et à une minéralogie très complexe », indiquait Barun Gorain, directeur du groupe Solutions technologiques stratégiques de Barrick Gold. « Le véritable problème est que plus de 99 %des minerais que nous traitons dans l’industrie aurifère sont considérés comme des résidus. »D’après lui, la flottation des particules grossières pourrait permettre aux mines de rejeter les résidus plus tôt dans la chaîne de valeur, ce qui contribuera à terme à réduire les coûts d’investissement et d’exploitation.
Malheureusement, la cellule de flottation traditionnelle n’atteint un degré élevé de récupération que dans des gammes de taille relativement restreintes. Par exemple, un minerai sulfuré peut très bien flotter entre 90 et 120 microns (μ), mais pas à 50 ou 150 μ.
Les recherches menées à ce jour ont identifié deux principales raisons à la limite supérieure imposée à la taille des particules flottantes. Tout d’abord, les particules grossières ont tendance à ne pas avoir une aussi grande minéralisation de surface pour attirer les bulles.
Ensuite, même si elles parvenaient à s’attacher aux bulles, elles ont tendance à se détacher de nouveau. Dans la plupart des modèles traditionnels de cuves, une turbine de flottation (aussi appelée agitateur) placée au fond de la cuve provoque une turbulence qui aide les bulles et les particules à entrer en collision. Les bulles remontent en passant par une zone calme, et s’assemblent en une couche d’écume en surface.
Graeme Jameson, professeur lauréat à l’université de Newcastle en Australie, expliquait que si les particules s’attachent aux bulles qui tournent autour d’elles en vortex liquides à 100 tours par seconde (tr/sec), la particule se détachera tout simplement de la bulle à une taille critique donnée.
La turbulence à haute énergie est excellente pour la récupération de petites particules ; par définition, c’est l’existence même de la turbulence qui maintient les particules de toute taille en suspension. Cependant, c’est également cette turbulence qui dissuade les particules grossières de flotter.
« Avec des particules grossières, il faudra mélanger le liquide encore plus vite pour éviter qu’elles ne se déposent au fond de la », indiquait-il. « Ainsi, le but même de cet équipement est intrinsèquement voué à l’échec dans la mesure où il tente de faire flotter des particules grossières. »
Lits fluidisés
Au lieu d’utiliser un agitateur, la technologie HydroFloat d’Eriez utilise un lit fluidisé pour soulever les particules grossières de minerai. L’alimentation est insérée par le haut, et l’arrivée d’eau de la cuve se trouve environ aux deux tiers vers le bas. À mesure que les particules grossières se déposent au fond de la cuve, le flux constant d’eau les repousse vers le haut, ce qui perturbe constamment une région composée à 65 % de solides. L’eau est traitée avec du gaz comprimé et un adjuvant moussant pour générer des bulles auxquelles peuvent s’attacher les particules grossières. Alors que les particules minéralisées se déplacent en flottant vers la goulotte de déversement, la gangue grossière se dépose dans une zone d’exhaure dans le dernier tiers de la cuve, au fond. Lorsque cette zone atteint une certaine densité, elle libère son contenu dans la conduite d’évacuation de la sous-verse.
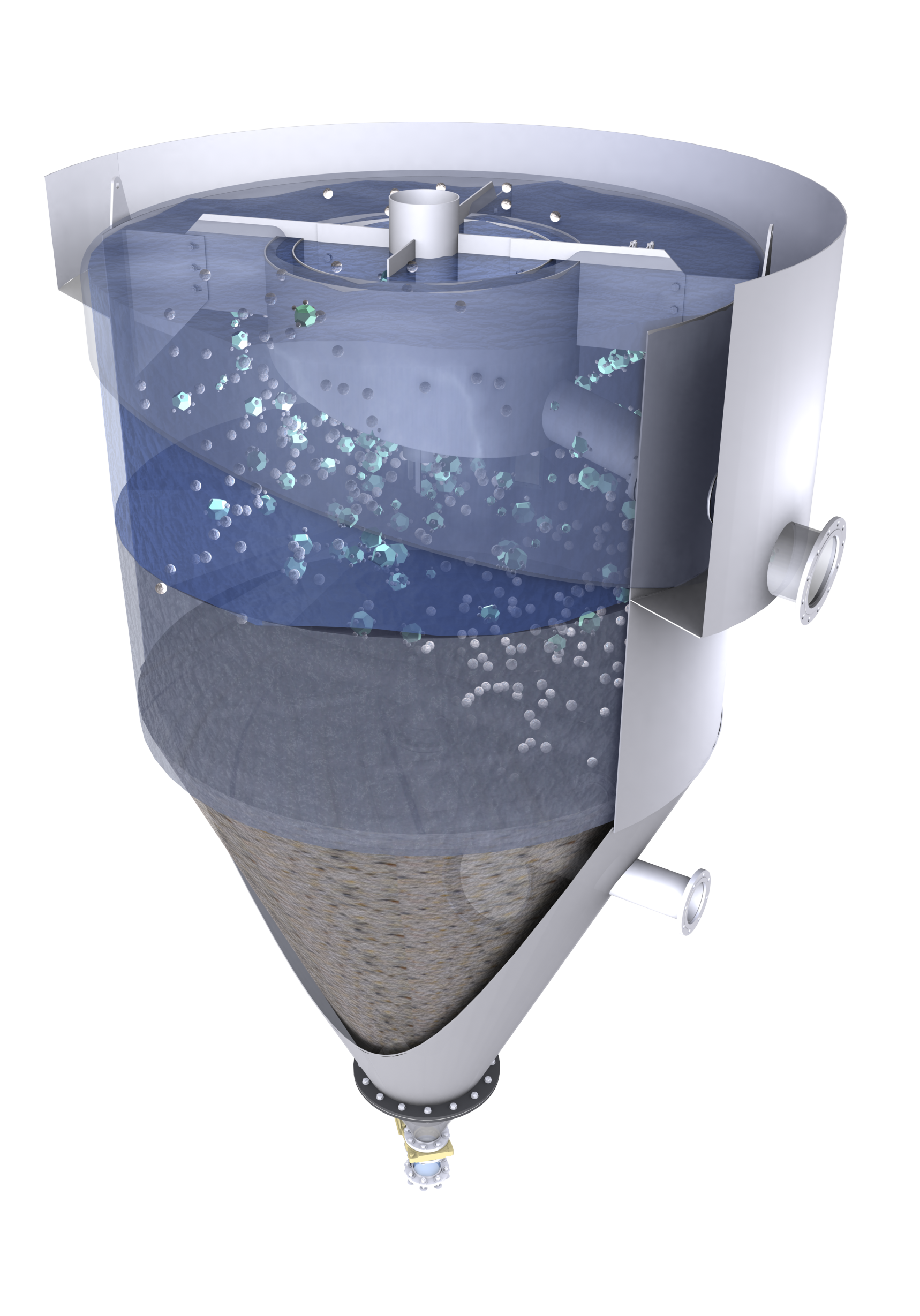
D’après Ken Roberts, directeur des ventes à l’international chez Eriez, HydroFloat peut étendre la flottation à des minerais de 400 μ, voire plus. Avec certains minerais sulfurés, ce dispositif a permis de récupérer des particules de 2 millimètres, soit 2 000 μ. En outre, expliquait-il, « nos recherches menées en collaboration avec l’université de l’Utah ont montré que nous pouvons faire flotter une particule affichant une minéralisation de surface de 2 %. »
M. Jameson mène des travaux de recherche en laboratoire sur sa propre solution de lit fluidisé depuis 2006. Son modèle adapte la cellule du même nom, la cellule Jameson, qu’il a brevetée à la fin des années 1980. Contrairement au dispositif HydroFloat, sa cellule traite les particules fines et grossières ensemble. L’alimentation du circuit de flottation passe tout d’abord à proximité d’un jet d’air, où elle rencontre la haute énergie nécessaire à la fixation des particules fines aux bulles. « Comme la cellule de flottation Jameson en quelque sorte », indiquait-il.
Elle s’écoule ensuite dans un lit fluidisé où l’environnement à plus faible énergie permet aux particules grossières de se fixer. Les bulles chargées de minerai flottent vers une couche d’écume et se déversent dans une goulotte. Une conduite de recyclage élimine le liquide en surface et le recycle dans la base, lequel servira à la fluidisation. Toutes les particules fines soumises à ce procédé de recyclage ont une seconde chance de se fixer à une bulle proche de la base. La gangue fine se rapproche d’une conduite d’évacuation du trop-plein.
Il y a un an, M. Jameson a mis la main sur un minerai de cuivre porphyrique d’Amérique du Sud, et ses travaux récemment terminés ont donné des résultats prometteurs. « On peut obtenir une récupération de 100 % pour des particules d’environ 100 microns », indiquait-il.
M. Jameson cherche maintenant un site minier souhaitant tester une installation grandeur nature capable de traiter entre 50 et 100 tonnes par heure. « La logique est qu’une unité de cette taille est relativement facile à gérer et à construire », indiquait- il. « On peut l’amener sur un site par camion et l’installer facilement pour effectuer des essais, et on peut ensuite envisager une mise à l’échelle en toute confiance. »
Construire plus grand, mais aussi plus intelligent
La technologie éprouvée permet la flottation du minerai grossier, mais elle est encore loin de répondre aux normes. « L’industrie minière a tendance à résoudre les problèmes de déclin des teneurs de l’alimentation et de coûts élevés en exploitant les économies d’échelle », déclarait Walter Valery, directeur à l’international en matière de conseils et de technologie pour l’exploitation minière et la minéralurgie chez Hatch. La tendance consiste à « traiter beaucoup de tonnes, broyer finement tous les matériaux et laisser les procédés de séparation en aval se charger du tri. » Malheureusement, c’est une pratique généralement inefficace qui n’est ni responsable ni viable pendant les temps d’immobilisation.
Les grands équipementiers répondent à cette demande en concevant des cellules de flottation toujours plus grosses. Il y a 30 ans, une cellule d’un volume de 30 mètres cubes (m3) aurait été exceptionnellement grande. Aujourd’hui, il est courant de trouver des cellules de 300 m3. Outotec dispose d’une cellule de 500 m3 en service et attend la livraison imminente de plusieurs cellules de 630 m3 ; FLSmidth, quant à elle, en exploite une de 660 m3.
Construire une grosse cuve permet en effet de réaliser des économies d’échelle en termes de consommation d’énergie. Ceci se révèle particulièrement prometteur pour les sociétés minières qui commencent à s’intéresser au coût énergétique de la flottation ; il s’agissait jusqu’ici d’un grand problème dans le domaine de la comminution, mais on s’y intéresse désormais étant donné l’intensification générale des pressions concernant les coûts et l’augmentation de la quantité de tonnes traitées par flottation.
« Lorsque l’on double la taille [d’une cuve], on économise entre 10 et 20 % d’énergie en pratique », indiquait Antti Rinne, vice-président des ventes destinées à la valorisation chez Outotec. « À l’heure actuelle, ceci représente des sommes énormes dans la plupart des pays du monde. »
Cette mise à l’échelle progressive s’accompagne cependant d’inconvénients. Si le volume de la cuve augmente, la turbulence n’atteindra pas nécessairement une hauteur correspondante, faisant ainsi d’une partie du volume supplémentaire de la cuve une perte d’espace, d’acier et d’argent.
« La partie hautement turbulente de la cellule a considérablement diminué étant donné l’augmentation importante de la taille des cellules ces 20 dernières années », déclarait Erico Tabosa, ingénieur principal des procédés chez Hatch.
FLSmidth a résolu ce problème grâce à son nouveau modèle d’agitateur nextSTEP, développé dans l’optique d’éliminer les espaces « morts » dépourvus de turbulence. Ce nouveau modèle rend également cette machine plus écoénergétique. « Nous avons constaté que la consommation d’énergie de notre modèle est toujours inférieure à celle d’autres machines de flottation à air forcé », déclarait Asa Weber, directeur de la technologie de flottation chez FLSmidth.
L’autre grande innovation de FLSmidth est la configuration du circuit de flottation à énergie hybride (Hybrid Energy Flotation), qui résout un problème d’incohérence dans les cellules de flottation. Une quantité donnée de minerai est récupérée dans chacune des cellules du circuit, aussi les caractéristiques minéralogiques varient d’une cellule à l’autre, mais pas la conception de la cellule.
Outotec a également développé des moyens de changer d’échelle tout en préservant l’efficacité énergétique. Le Float- Force, son propre modèle innovant d’agitateur présenté en 2007, comprend un rotor/stator affichant des avantages similaires en termes de répartition de la turbulence. Outotec a également inventé un agitateur auxiliaire, baptisé FlowBooster, qui améliore le mélange dans la cuve en ne requérant que très peu d’énergie supplémentaire.
Des efforts importants ont été déployés afin de trouver la vitesse de l’agitateur la plus adaptée à ce genre de minerai et d’application. « Nous avons mené de nombreuses recherches ses dernières années pour étudier les variateurs de vitesse sur les cellules de flottation », expliquait Ben Murphy, directeur de la technologie de la flottation chez Outotec. Les premières grandes cellules fonctionnant avec des variateurs de vitesse ont été installées il y a environ cinq ans. Depuis, ces installations ont montré qu’elles pouvaient optimiser l’utilisation d’énergie, sa récupération, ou les deux.
« Le plus intéressant est que nous avons pu analyser une grande partie des recherches sur l’optimisation de la vitesse et la réduction de la consommation énergétique, et les appliquer à de petites cellules », indiquait M. Murphy. « C’est ingénieux ; cela ne fonctionne pas toujours de cette façon. » Une petite exploitation reposant sur des groupes électrogènes diesel dans un lieu isolé pourrait réaliser de grandes économies.
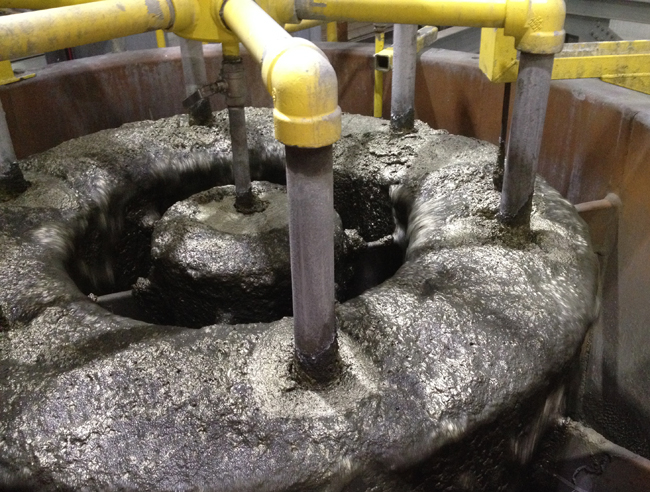
Chambres séparées
Barrick utilise de grandes cellules traditionnelles dans ses exploitations. La société collabore cependant avec différents consortiums pour développer « la prochaine génération » de machines de flottation plus performantes, indiquait M. Gorain. « Les économies d’échelle fonctionnent encore pour certains minerais ; cependant, pour les corps minéralisés complexes à faible teneur, les cellules traditionnelles atteignent leurs limites techniques ou, dans le meilleur des cas, leurs avantages sont insignifiants », indiquait-il.
Le consortium a financé les travaux de Woodgrove Technologies sur un nouveau modèle. Plutôt que des zones séparées dans une cuve, le réacteur de flottation étagé (SFR, de l’anglais staged flotation reactor) répartit les étapes du processus de flottation dans trois chambres, à savoir une unité de collecte des particules turbulentes, une unité de libération des bulles latentes et une unité similaire de récupération de l’écume latente. Chaque SFR est construit sur commande en fonction des caractéristiques prévues du minerai dans chaque mine.
« Nous étudions la teneur et le nombre de tonnes de minerai à traiter sur la durée de vie complète de la mine, puis nous concevons l’unité de récupération de l’écume afin de gérer la distribution pondérée des unités métalliques durant cette période », indiquait Glenn Kosick, président de Woodgrove Technologies. « Par exemple, à l’extrémité du banc de cellules dans des machines de flottation classiques, on pourrait récupérer entre 0,3 et 0,5 tonne par heure et par mètre carré. Cette machine, quant à elle, pourrait bien parvenir à traiter entre 2,5 et 3 tonnes par heure et par mètre carré. »
D’après M. Kosick, la conception performante du SFR réduit de près de la moitié sa consommation énergétique par rapport à une cellule de flottation traditionnelle ; en outre, elle prend moins de place, ce qui réduit les frais liés à son installation. « Nous la vendons en raison des économies qu’elle permet de réaliser en termes de coûts d’investissement et d’exploitation », indiquait-il. Cependant, sa conception promeut également une meilleure sélectivité en raison de la quantité inférieure d’air nécessaire utilisé dans ces machines par rapport aux cellules des cuves.
« Les données que nous recevons avec les machines à échelle réelle nous montrent que l’on peut assurer la flottation de matériaux plus grossiers en restreignant la zone de surface, ce qui permet d’obtenir des mousses très stables et des distances de transport relativement courtes », déclarait M. Kosick. La cellule la plus grossière actuellement utilisée traite une alimentation dont 80 % (p80) fait 230 microns environ ; la plus fine mesure 20 microns.
Depuis 2010, 22 réacteurs de flottation étagés ont été mis en service ; plus de 130 sont en cours de conception. Après quelques installations fructueuses dans des petites exploitations minières, le consortium a financé une mise à l’échelle pilote permettant de traiter 930 tonnes par heure (t/h) à la mine de cuivre Sossego de Vale, au Brésil. L’une des sociétés du consortium a récemment attribué à Woodgrove l’étude technique détaillée d’une installation dans un projet d’extraction de cuivre traitant 95 000 tonnes par jour (t/j) au Chili.
Fusion des solutions
Ces nouvelles solutions sont souvent présentées (et peuvent être installées) comme des projets particuliers. Elles sont cependant plus efficaces si on les envisage de manière holistique. Par exemple, Woodgrove a récemment fusionné avec le prestataire de contrôles de procédés Portage Technologies, ce qui lui permet de fournir en un seul lot la surveillance de l’équipement et des procédés. Woodgrove propose maintenant un système de caractérisation de l’écume qui mesure sa vitesse, sa stabilité et sa couleur, ainsi que la taille, le nombre et la densité des bulles ; ce système suggère par ailleurs des changements au niveau des paramètres de l’équipement. En outre, en contrôlant l’alimentation qui passe dans le broyeur et les cyclones, on pourra éviter que des matériaux non souhaités atteignent le circuit de flottation.
À plus grande échelle, les modèles de schémas de traitement innovants et l’élaboration de systèmes de réactifs sont tout aussi importants que les besoins en équipement de flottation performant. Barrick, par exemple, utilise son propre schéma de traitement breveté pour un corps minéralisé aurifère réfractaire très complexe. Ce procédé, baptisé mill-chemical-float-mill-chemical- float (MCF2, un procédé de broyage-ajout de substance chimique-flottation réitéré à deux reprises), implique en premier lieu de faire flotter les particules grossières dans l’alimentation, de les rebroyer, puis de faire flotter les fines, tout en assurant la présence de composés chimiques adaptés qui pourront répondre aux besoins des particules grossières et des fines séparément.
Comme beaucoup travaillant dans le milieu de la recherche et de l’innovation, les conseillers de Hatch suggèrent d’adopter un modèle de schéma de traitement de type mine-to-mill (« de l’extraction au broyage ») adapté à une gamme particulière de corps minéralisés.
Un schéma de traitement réinventé pourrait commencer par un abattage à l’explosif plus ciblé ; il pourrait ponctuer la flottation d’activités de broyage. Kristy Duffy, ingénieure en traitement des minerais chez Hatch, suggérait que les nouvelles technologies de flottation de particules grossières pourraient se révéler utiles à l’étape de préconcentration pour éliminer la gangue grossière. Ces étapes pourraient être le broyage grossier, la flottation pour la préconcentration, le broyage, le dégrossissage, le rebroyage et la flottation de nettoyage.
M. Gorain reconnaît l’utilité potentielle de cette technique. « La préconcentration non fondée sur la flottation est en réalité bien plus intéressante car on essaie de gérer au mieux les résidus au moment même de l’extraction, avant d’entreprendre une quelconque activité de comminution, qui consomme beaucoup d’énergie », indiquait-il. Pourtant, si la minéralogie du minerai est disséminée trop largement ou finement pour d’autres méthodes, la flottation pourrait selon lui potentiellement constituer une première étape efficace.
On accorde aujourd’hui un plus grand intérêt au triage du minerai, lequel peut contribuer à éliminer la gangue dès le départ et apparaît souvent dans les discussions portant sur le procédé de type « de l’extraction au broyage ». M. Roberts d’Eriez précisait que plusieurs grandes sociétés minières envisageaient cette option, qui pourrait aller de pair avec une installation potentielle d’HydroFloat.
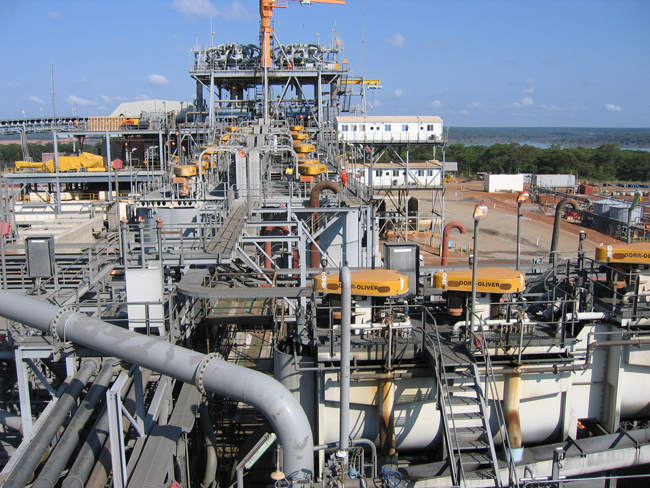
Effets du ralentissement économique
Dans le contexte financier morose que traverse l’industrie ces dernières années, il a fallu aller de l’avant en matière d’innovation, car nombre de projets n’auraient tout simplement pas été viables s’ils n’avaient pas adopté de nouvelles approches. « J’ai rencontré deux grandes sociétés minières en entreprise commune en Amérique du Sud il y a environ un mois, et leur ai présenté HydroFloat ainsi que d’autres technologies dont nous disposons », indiquait M. Roberts. « C’était le but premier de cette rencontre, leur présenter nos nouveautés. Il y a cinq ou dix ans en arrière, personne n’aurait évoqué cela. »
Comme l’indiquait M. Kosick, Woodgrove Technologies reste active pendant cette période de ralentissement économique, sans avoir à se vendre. « Nous embauchons pratiquement toutes les semaines pour essayer de répondre à la demande », indiquait-il.
Le ralentissement économique a cependant aussi étouffé la recherche qui pourrait permettre de générer de nouvelles innovations. « La plupart des services de R&D des sociétés ont été durement touchés par le ralentissement économique qui s’est abattu sur l’industrie minière », indiquait Sergio Vianna, ingénieur en traitement des minerais chez Hatch. « Ainsi, le nombre de nouvelles solutions développées dans le domaine de la minéralurgie ces dernières années est bien trop insuffisant. »
Pour aider à déterminer la bonne taille des cellules traditionnelles et les sélectionner, Hatch aimerait disposer d’une étude détaillée sur le rythme auquel l’écume peut déverser de manière stable les minéraux récupérés par-delà le rebord de la cellule de flottation. M. Vianna émet cependant des doutes quant à la probabilité qu’une telle étude ait lieu dans le climat actuel du monde de la recherche.
D’après Kym Runge, chercheuse universitaire principale au Julius Kruttschnitt Mineral Research Centre (JKMRC, le centre de recherche Julius Kruttschnitt sur les minéraux) de l’université de Queensland en Australie, l’écosystème autrefois sain de centres de recherche, de sites miniers et de services d’expertise d’Australie risque, si les tendances se poursuivent, de subir trop de coupes pour pouvoir se redresser. De nombreux chefs de file mondiaux spécialisés dans le traitement des minerais sont passés par le JKMRC ou se servent d’outils développés dans ce centre.
La recherche se poursuit cependant dans la mesure du possible. « Nous travaillons sur bon nombre d’autres technologies », expliquait M. Gorain de Barrick. « Bien entendu, elles sont très confidentielles, aussi nous ne serons pas en mesure d’en parler ouvertement. Mais de manière générale, l’idée principale consiste à développer des solutions pour divers corps minéralisés complexes. »
Mme Runge travaille sur plusieurs projets de recherche. En dépit des progrès réalisés par les équipementiers, nous avons encore beaucoup à apprendre quant à la manière dont la turbulence affecte la flottation dans les plus grosses cellules. « En changeant une seule variable, beaucoup ont vu des corrélations et ont tiré leurs conclusions », expliquait-elle.
Elle décrit également le besoin de simuler le type de schéma de traitement intégré et innovant imaginé au JKMRC. « L’industrie minière n’aime pas prendre de risques », indiquait- elle, ajoutant qu’« en pouvant évaluer l’avantage économique de l’installation d’une unité de flottation de particules grossières pendant le broyage, on pourra promouvoir l’adoption de cette technologie. »
Lorsqu’on lui demandait ce à quoi ressembleraient les circuits de flottation dans une dizaine d’années, Mme Runge faisait preuve d’un optimisme prudent. « J’espère que nous allons commencer à assister à l’adoption de certaines de ces nouvelles technologies », concluait-elle. « Nous sommes voués à traiter de plus grandes capacités, aussi nous devrons fabriquer des outils plus grands, mais il faut espérer que nous gérerons la situation de manière un peu plus intelligente. »
Traduit par Karen Rolland
Plus dans la catégorie Technologie
La révolution de l'automatisation
Cela ne fait aucun doute, l'avenir de l'industrie minière passe par l'automatisation. Cependant, à quoi ressemble cet avenir et par quel chemin allons-nous y arriver?
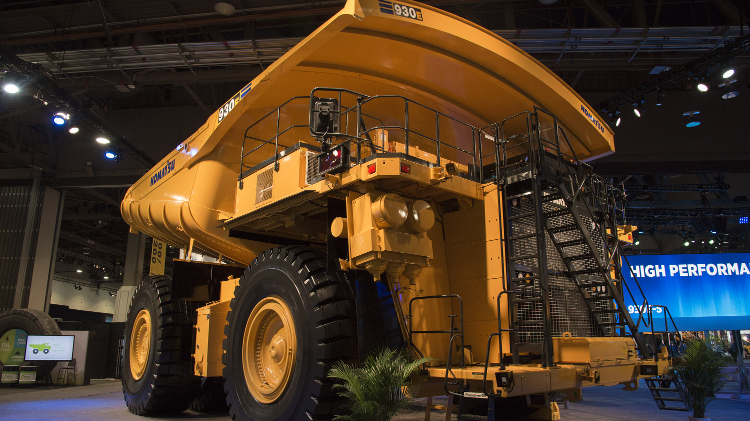
La conscience des coûts dans la ville que l’on surnomme « Sin City »
Efficacité et rendement : la philosophie du dernier Minexpo