La spirale de la chaîne d’approvisionnementLa composition complexe des métaux nécessaires à la fabrication des batteries, les forces du marché et les progrès de la science
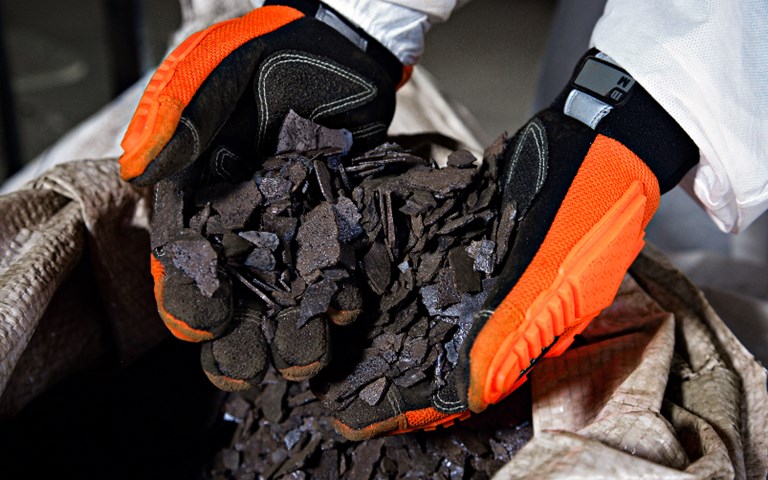
Les batteries constituent une méthode simple et polyvalente de stocker l’énergie électrique dans toute sorte de dispositifs, depuis les minuscules équipements médicaux implantables et dispositifs électroniques personnels jusqu’aux véhicules, maisons, bâtiments, mines et réseaux de villes entières. On les connaît mieux pour leurs applications portables, notamment dans des dispositifs électroniques et des véhicules, mais elles ont aussi des usages permanents et stationnaires comme le stockage dans le réseau de l’électricité générée à partir de sources renouvelables, par exemple l’énergie solaire et éolienne.
Pour les sociétés minières, l’économie à faibles émissions de carbone en plein essor et le rôle primordial des batteries représentent à la fois un défi et une occasion. La demande en métaux nécessaires à la fabrication des batteries est, certes, vouée à augmenter, mais quels métaux seront les plus recherchés ? Actuellement, les principaux moteurs de cette demande sont les véhicules électriques (VE) et les matériaux nécessaires à la fabrication de différents types de cathodes dans leurs batteries lithium-ion (Li-ion) tels que le lithium, le nickel, le cobalt, le manganèse et l’aluminium. La fabrication des VE ne constitue cependant qu’une partie de l’équation. La charge des VE dans un système électrique qui dépend fortement de l’énergie éolienne ou solaire requiert un stockage d’énergie fiable pour la stabilisation du réseau.
« La capacité renouvelable, provenant essentiellement des énergies éolienne et solaire, doublera au cours des dix prochaines années », déclarait Daniel Brenden, analyste principal en matière d’énergie et de sources renouvelables chez Fitch Solutions. « Le problème des énergies éolienne et solaire est qu’elles sont par nature instables, qu’elles dépendent des conditions météorologiques et que leur fiabilité repose sur une grande capacité de stockage. Les véhicules électriques constituent le principal moteur de croissance de la capacité de stockage qui fait surface. »
Des compositions divergentes
Les constructeurs automobiles du monde entier investissent des milliards de dollars pour les décennies à venir dans le développement de nouveaux modèles de VE et l’élimination progressive des moteurs à combustion interne (MCI). D’après J.P. Morgan, les ventes de véhicules électriques rechargeables à l’échelle mondiale atteignaient presque un million de véhicules, soit 1 % des ventes pour l’année 2016. Selon les prévisions de la société, ces ventes atteindront près de 8,4 millions de véhicules, soit une part de marché de 7,7 % d’ici 2025.
« Avec un VE, l’important est de pouvoir stocker autant d’énergie que possible dans un espace toujours plus restreint, aussi la densité énergétique est très importante », expliquait M. Brenden. « C’est là où les applications de [batteries] pour VE diffèrent des applications en réseau, car elles n’ont pas les mêmes limites en termes d’espace. »
Dans une série d’articles publiés à la fin de l’année 2018, Fitch Solutions prévoyait qu’à l’échelle mondiale, les cathodes de nickel-manganèse-cobalt (NMC) domineraient les ventes de batteries pour VE à l’avenir, mais que les cathodes moins coûteuses de lithium-fer-phosphate (LFP) conserveraient une présence importante sur les marchés chinois. La cellule LFP ne contient pas de cobalt, sa densité énergétique est faible et par conséquent, elle a une portée peu élevée ; elle présente cependant des avantages, notamment son faible coût, une stabilité thermique intéressante et la capacité à être déchargée et rechargée à plusieurs reprises. Les cathodes NMC sont le type de batteries Li-ion qu’utilisent la plupart des fabricants de VE européens, lesquels apprécient leur stabilité thermique, leur haute densité énergétique et leur faible coût.
« La capacité à stocker beaucoup d’énergie dans un véhicule et d’effectuer de grands trajets entre chaque charge est indispensable pour rendre plus attrayants les VE auprès d’un public plus vaste », indiquait M. Brenden. « Ceci incitera à augmenter l’usage du nickel dans les batteries. »
Nickel
Le nickel est un métal abondant, déclarait George Heppel, analyste principal pour les marchés du cobalt, du lithium et des batteries au sein du groupe CRU. De nombreux gisements de nickel de catégorie 2, idéaux pour la production d’acier inoxydable, sont à l’étude, particulièrement en Asie du sud-est. C’est toutefois la pénurie de nickel de haute pureté de catégorie 1 nécessaire aux batteries et aux alliages spéciaux qui pose problème. « Si l’on trouve du nickel en grande quantité sur le marché », indiquait M. Heppel, « le problème est réellement de savoir où nous allons trouver les matériaux de haute qualité adaptés à une utilisation dans les batteries. »
La solution la plus ardue consiste à trouver et à développer de nouveaux gisements riches en nickel de catégorie 1 ; toutefois, un autre procédé techniquement complexe, l’exploitation minière par lixiviation acide sous haute pression (HiPAL, de l’anglais high-pressure acid leach), pourrait constituer une option. Le procédé HiPAL produit du sulfate de nickel (la matière première nécessaire à la production des batteries) directement sur le site minier à l’aide d’un procédé de séparation à haute température et haute pression qui est appliqué au minerai de latérite, relativement abondant. Sumitomo Metal Mining (SMM) déclare avoir été l’une des premières sociétés à tester la technologie HiPAL dans son exploitation de nickel aux Philippines.
Cobalt
À l’échelle mondiale, plus de la moitié du cobalt est extraite en République démocratique du Congo (RDC), un pays relativement instable sur le plan politique où les mineurs artisanaux extraient environ un cinquième du minerai de cobalt à la main.
Comme le déclarait le 18 juin 2018 sur Twitter le cofondateur et chef de la direction de Tesla Elon Musk, « nous utilisons actuellement moins de 3 % de cobalt dans nos batteries, et nous n’en utiliserons plus du tout dans la prochaine génération ». Si cet objectif est admirable, M. Heppel avertissait qu’il ne serait pas facile à atteindre dans la décennie à venir, car le cobalt est un élément extrêmement important pour la composition chimique de la batterie. En effet, il tient lieu d’agent stabilisateur et empêche la batterie de surchauffer.
« Le cobalt est extrêmement important pour préserver la sécurité de la batterie », indiquait M. Heppel. « Nous continuerons à réduire la teneur en cobalt de nos batteries, mais pour ce qui est de l’éliminer complètement, nous n’en sommes pas encore à cette étape. En termes de stabilité, de coût et de facilité de production, les composants chimiques des batteries au cobalt ne peuvent en effet pas être remplacés par n’importe quel élément. »
Jusqu’à ce que l’on identifie une autre source acceptable de cobalt, le monde continuera d’acquérir la majeure partie de son cobalt en RDC, où les risques de nationalisation des ressources sont grands et où le gouvernement a tendance à modifier de manière soudaine les lois minières, notamment en mettant en œuvre des interdictions imprévues sur les exportations de cobalt telles que celle de mars 2019.
Le troisième type de batterie Li-ion utilisé dans les VE est la batterie à nickel-cobalt-aluminium (NCA). Les batteries à NCA se trouvent à mi-chemin entre celles à NMC et à LFP, avec une teneur moins élevée en cobalt mais une densité énergétique plus forte. Tesla déclarait en milieu d’année 2018 que la teneur en cobalt des éléments de batterie à NCA utilisées dans le VE de modèle 3 contenait moins de cobalt qu’une batterie à NMC affichant un rapport nickel-manganèse-cobalt de moins de 8:1:1. Quatre de ces batteries à NCA seront utilisées pour alimenter les semi-remorques que Tesla envisage de commencer à fabriquer en 2020.
Lithium, aluminium et manganèse
Les trois autres composants essentiels à la fabrication des batteries des VE, à savoir le lithium, l’aluminium et le manganèse, sont abondants, relativement peu coûteux et faciles à extraire. Sur ces trois composants, la chaîne d’approvisionnement en manganèse est celle qui pose le moins problème. Le manganèse est un élément abondant, que l’on trouve sous une forme utilisable et qui bénéficie d’un marché fort appuyant sa production à d’autres fins.
« Le lithium est indéniablement le métal le plus affecté par la forte augmentation de la demande en VE et en batteries, surtout parce que ces dernières sont au cœur de la forte demande en lithium », expliquait M. Heppel. D’après une analyse récente menée par le groupe CRU, la fabrication de batteries en 2018 représente pour la première fois plus de 50 % de la demande en lithium. Le groupe CRU prévoit une croissance rapide de la demande en batteries à lithium au cours des dix prochaines années ; d’ici 2023, plus de 69 % de la demande en lithium concernera les batteries.
Si l’aluminium est lui aussi abondant, nous avons besoin des fabricants pour le transformer en alumine à haute pureté (HPA, de l’anglais high-purity alumina), utilisée comme séparateur dans les éléments de batterie, un fin revêtement entre l’anode et la cathode.
« Il existe un risque de pénurie de HPA », expliquait M. Heppel. « L’aluminium n’est pas enclin à la pénurie, mais le transformer en cette forme de HPA pourrait poser problème. L’investissement est important, notamment en Australie, mais si des obstacles ou un manque d’investissement venaient à se produire, il faudra alors s’inquiéter. »
Des véhicules électriques lourds à batterie
En plus des millions de véhicules électriques pour particuliers qui devraient être mis en circulation dans les dix années à venir, il convient de parler de l’attrait des véhicules électriques lourds à batterie dans tout un éventail de secteurs, dont le secteur minier. Étant donné le coût de remplacement des équipements lourds, de nombreux exploitants envisagent désormais de rénover leur équipement lourd alimenté au diesel en les équipant de batteries électriques.
Robert Rennie est le président de Mobile Equipment Design and Automation Technology (MEDATECH), une société basée en Ontario qui convertit les véhicules à MCI en des véhicules électriques à batterie à l’aide de techniques personnalisées. Environ 80 % des clients de MEDATECH travaillent dans le secteur minier, et l’équipe a récemment collaboré avec MacLean Engineering pour fabriquer une niveleuse automotrice entièrement rénovée en un véhicule électrique fonctionnant à 100 % sur batterie pour la mine Borden Lake de Goldcorp, qui deviendra la première mine souterraine entièrement électrique.
« Nous ne nous arrêtons pas à une composition en particulier », expliquait M. Rennie. « L’élément principal qui intéresse tout le monde est AKASOL, notre fournisseur de batteries allemand. »
AKASOL fabrique des batteries Li-ion de diverses compositions, dont plusieurs versions de la batterie à NMC. MEDATECH utilise principalement la nanobatterie d’AKASOL, une version hybride entre une cellule NMC et une cellule de lithium-titane-oxyde (LTO). Le résultat est une batterie riche en énergie adaptée aux demandes qui pèsent sur l’équipement lourd.
M. Rennie recommande la nanobatterie d’AKASOL pour les véhicules qui requièrent beaucoup d’énergie et une grande capacité énergétique, par exemple un camion de transport. Tout comme pour les véhicules commerciaux particuliers, la difficulté réside dans la coordination du régime de chargement en fonction du type de batterie et de ses fins.
« La batterie est réellement importante », expliquait M. Rennie. « Ce qui est tout aussi important, c’est le lieu où vous allez la charger. Les technologies ne seront sans doute pas très différentes dans dix ans, mais on investira incontestablement beaucoup plus dans l’infrastructure de chargement. »
Un fondement pour les applications stationnaires
Si certaines applications stationnaires utilisent des piles de batteries Li-ion, notamment car il s’agit du seul type de batterie disponible ces dernières années, le vanadium, que l’on utilise principalement pour renforcer l’acier, devient le métal de prédilection pour le stockage en réseau.
« Certains faits se produisant au sein de l’industrie du vanadium changent rapidement la donne en termes de demande », expliquait Mark Smith, chef de la direction de Largo Resources, une société d’extraction du vanadium basée à Toronto produisant environ 10 000 tonnes de produits à base de vanadium par an à la mine Maracás Menchen, au Brésil. « L’un d’eux concerne la norme pour barre à béton armé qui a vu le jour en Chine. »
En novembre 2018, la Standardization Administration of the People’s Republic of China (SAC, l’administration de normalisation de la République populaire de Chine) a présenté de nouvelles réglementations exigeant que les barres à béton armé (une barre en acier renforcé) répondent à des exigences spécifiques en termes de limite d’élasticité, un objectif réalisable en ajoutant environ un kilogramme de vanadium à une tonne d’acier. D’après Vanitec, une association commerciale internationale de producteurs de vanadium basée au Royaume-Uni, ces nouvelles réglementations visent « à réduire l’utilisation d’acier ne répondant pas aux normes, et à rendre plus résistants aux tremblements de terre les bâtiments en Chine. »
Ce métal est également un élément important dans les batteries rechargeables à flux à oxydoréduction au vanadium (VRFB, de l’anglais vanadium redox flow battery). « Le moment est bien choisi au vu de toutes les énergies renouvelables qui font leur entrée sur le marché », indiquait M. Smith. « Les consommateurs ou les sociétés de services publics n’en auront pas grand usage s’ils ne les associent pas à une batterie. »
La mine Maracás Menchen de Largo Resources au Brésil. Avec l'aimable autorisation de Largo Resources
Le premier brevet pour une VRFB a été accordé il y a plus de 30 ans à des chercheurs de l’université de Nouvelle-Galles du Sud à Sydney, en Australie, mais la batterie a seulement été commercialisée ces dernières années. L’avantage d’utiliser le vanadium pour stocker l’énergie réside dans les quatre états d’oxydation différents des sels de vanadium. L’anode et la cathode sont deux espèces du vanadium. À l’intérieur d’une VRFB, deux électrolytes sont mélangés dans un assemblage de cellules, mais sont maintenus séparés par une fine membrane perméable échangeuse d’ions. Une réaction redox (ou réduction-oxydation) a lieu dans la cellule, générant un flux d’électrons qui produit de l’énergie électrique. En stockant les deux solutions d’électrolyte liquide contenant différents sels de vanadium dans des réservoirs différents, les solutions ne se dégradent pas.
« Le vanadium ne se consomme pas comme dans une batterie Li-ion », expliquait M. Smith. « Il s’agit d’une manière préférable de stocker l’énergie renouvelable ou du réseau, puis de la distribuer lorsque le public en a besoin. »
Les VRFB longue durée sont bien adaptées aux applications stationnaires, car leur capacité peut facilement être augmentée en ajoutant davantage d’éléments. Cependant, la concurrence pour l’utilisation du vanadium à d’autres fins est intense. D’après Vanitec, on a produit à l’échelle mondiale 80 523 tonnes métriques de vanadium en 2017. À l’heure actuelle, un peu plus de 90 % du vanadium est destiné à l’industrie de l’acier. Vanitec estime que la demande potentielle de vanadium pour les batteries pourrait augmenter et atteindre 25 000 à 30 000 tonnes par an d’ici 2025.
Le vanadium de grande pureté est également très demandé pour une nouvelle batterie Li-ion au vanadium développée par le fabricant de montres Swatch et Belenos Clean Power Holding Ltd. pour diverses utilisations, notamment pour un usage dans les VE développés par le fabricant automobile chinois Geely.
« Nous avons rencontré Swatch car la société avait besoin de vanadium très pur, et Largo en produit », indiquait M. Smith. « Nous sommes l’un des deux fournisseurs vers qui la société peut se tourner. »
Les perspectives pour les explorateurs et les producteurs de vanadium sont de bon augure. Largo mène l’exploration d’un site désaffecté et travaille sur un projet d’agrandissement afin d’augmenter sa production à la mine Maracás Menchen pour atteindre 12 000 tonnes de pentoxyde de vanadium (V205) par an.
Les autres compositions des batteries évoluent à pas de géant sur la scène du stockage fixe d’énergie. Deux sociétés australiennes développent actuellement une autre technologie de batterie à flux qui repose sur la composition zinc-brome. La première, Redflow Energy Storage Solutions basée à Brisbane, a récemment installé des batteries à zinc-brome à flux pour stocker de l’énergie solaire et fournir une source d’énergie fiable à un village isolé dans le nord montagneux de la Thaïlande. Ce projet, soutenu par le gouvernement thaïlandais, utilise des cellules solaires pour exploiter l’énergie et un système hybride de batterie haute performance, dont le modèle de batterie ZBM2 de Redflow, pour stocker l’énergie nécessaire à un mini-réseau pour alimenter le village, distinct du réseau national de distribution de l’électricité.
La société Gelion Technology du nord de Sydney, en Australie, met au point une batterie fonctionnant au zinc et au brome qui repose sur un électrolyte sous forme de gel, et non liquide, à l’intérieur. Ces batteries sont ininflammables, ignifuges et suffisamment flexibles pour être incorporées dans diverses applications.
La demande est claire, mais qu’en est-il de l’offre ?
Alors que les chercheurs et les fabricants s’efforcent de développer des batteries fiables et à bas prix affichant des capacités toujours plus importantes de densité de stockage de l’énergie et de charge et recharge, les compositions et les technologies de batteries progressent rapidement. Il est évident que les matières premières nécessaires à leur confection resteront très demandées. Cependant, la demande ne suffit pas, prévenait David Anonychuk, directeur général de la société de conseils en exploitation minière M. Plan International Limited.
« Ce n’est pas la demande qui est cœur du problème, mais plutôt la pénurie que nous risquons fort probablement de rencontrer », déclarait M. Anonychuk. « Ni l’investissement ni les sociétés ne suffisent aujourd’hui à recueillir le capital nécessaire [pour faire avancer les projets dédiés aux métaux nécessaires à la fabrication des batteries]. »
D’après M. Anonychuk, la réticence à investir dans des projets dédiés aux métaux nécessaires à la fabrication des batteries dont font preuve les grandes sociétés et les institutions financières actuellement risque de créer une pénurie en matière d’offre d’ici quelques années.
« Nous pouvons parler de la magie de la demande, mais qui est confronté aux plus grands risques ? Ce sont les sociétés automobiles et de produits chimiques qui ont besoin de batteries Li-ion pour atteindre les objectifs qu’elles se sont fixés », expliquait M. Anonychuk. Ce dernier prévoit que le tournant en termes d’investissement de l’industrie des batteries se produira lorsque les sociétés automobiles et des produits chimiques commenceront à proposer de sérieux contrats d’approvisionnement ou des acquisitions d’actifs miniers. Actuellement, aucune grande société minière ne s’est diversifiée afin d’inclure des projets dédiés au créneau spécifique des métaux nécessaires à la fabrication des batteries.
« Ce n’est que lorsque les sociétés automobiles commenceront à investir que d’autres investisseurs emboîteront le pas - c’est le signal », concluait M. Anonychuk.
Traduit par Karen Rolland
Object reference not set to an instance of an object.
Plus dans la catégorie Opérations
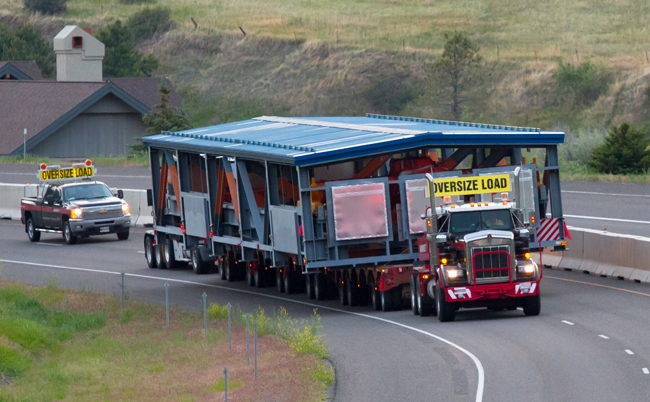
Emballés et prêts à l’emploi
Les avantages prouvés de la construction modulaire, assortis d’une pression financière extérieure, poussent l’industrie minière à adopter cette pratique
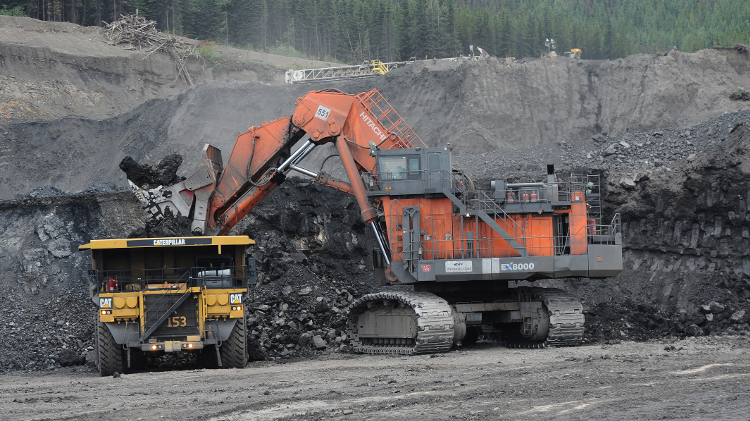
La hausse des prix du charbon nécessaire à la fabrication de l'acier redonne vie aux mines canadiennes
Le charbon n'avait pas atteint de tels prix depuis 2011, une année record où la tonne se vendait à 330 $ US