La ruée vers l'innovation dans l'industrie des sables bitumineuxLes exploitants et fournisseurs de sables bitumineux cherchent des moyens de réduire les coûts d'exploitation et les émissions

Des dizaines de technologies émergentes destinées à pratiquement toutes les facettes de la production des sables bitumineux pourraient bien aider l’industrie à trouver des solutions aux enjeux environnementaux et opérationnels les plus importants qu’elle rencontre actuellement. De fait, d’après une étude menée par le Canadian Energy Research Institute (CERI, l’institut canadien de recherche énergétique), ces technologies émergentes posent aujourd’hui les bases qui permettront à l’industrie de réduire de 40 % ses coûts opérationnels et jusqu’à 80 % de ses émissions. En bref, les sables bitumineux de l’Alberta connaissent une ruée vers l’innovation, et les répercussions pourraient être considérables.
Un environnement innovant
« La plupart d’entre nous envisagent l’innovation comme une technologie, mais elle peut se traduire de diverses manières », expliquait Dan Wicklum, directeur général de la Canada’s Oil Sands Innovation Alliance (COSIA, l’alliance canadienne pour l’innovation dans le secteur des sables bitumineux), formée en 2012 par 10 sociétés pétrolières qui représentent à elles seules 90 % de la production de sables bitumineux. « Le modèle de la COSIA constitue probablement l’une des plus grandes innovations dans le secteur pétrolier. »
Plutôt que d’appréhender l’innovation comme un moyen de se tailler un avantage concurrentiel, les sociétés membres de la COSIA collaborent en développant de nouvelles technologies qui leur permettront d’améliorer leurs performances environnementale et opérationnelle. Elles ont déjà partagé des droits de propriété intellectuelle d’une valeur de 1,4 milliard de dollars pour quelque 985 technologies et innovations. Il y a deux ans, la COSIA a également lancé le concours NRG COSIA Carbon XPRIZE, d’une valeur de 20 millions de dollars américains. Ce concours, mené à l’échelle internationale, récompense les équipes découvrant des technologies permettant de réduire les émissions de dioxyde de carbone (CO2) et de convertir le CO2 en produits utilisables.
« Un bon système d’innovation repose sur des personnes créatives, de bonnes idées et un financement solide, mais il requiert également l’infrastructure d’essai adaptée », déclarait M. Wicklum. Ainsi, la COSIA a établi un partenariat avec les gouvernements fédéral et de l’Alberta pour créer à Calgary l’Alberta Carbon Conversion Technology Centre (ACCTC, un centre de recherche dédié à la mise à l’essai de nouvelles technologies de conversion du CO2 en Alberta), qui a ouvert ses portes en mai. Construit à côté du Shepard Energy Centre (le centre pour l’énergie de Shepard), dont les émissions de gaz de combustion émanent d’une usine électrique au gaz naturel, cette nouvelle installation offre aux innovateurs les capacités requises pour tester, perfectionner et approfondir les technologies qui convertissent le CO2 en des produits utilisables en vue d’une commercialisation.
En avril, la COSIA a annoncé la liste des dix finalistes du concours Carbon XPRIZE. Chacun des finalistes recevra 500 000 dollars américains afin d’amener sa technologie jusqu’à la phase de commercialisation. Cinq des finalistes s’intéressent à la conversion des émissions de CO2 provenant du gaz, et ils seront les premiers à utiliser le nouveau centre ; les équipes s’intéressant à la conversion du CO2 émanant du charbon seront envoyées au Wyoming’s Integrated Test Center (le centre d’essai intégré du Wyoming). Avec du CO2, Carbicrete transforme les résidus industriels issus des scories d’acier en béton sans ciment, CERT crée des combustibles et des matières premières à valeur ajoutée, Newlight fabrique du plastique biologique, Carbon Upcycling Technologies développe des nanoparticules graphitiques et des dérivés du graphène, et C2CNT fabrique des nanotubes. Aux côtés des finalistes du Wyoming, ces sociétés prépareront leurs technologies à la commercialisation et entreront en lice pour remporter l’un des deux premiers prix de 7,5 millions de dollars, qui seront décernés en 2020.
Des systèmes de transport autonome
Avec un parc de véhicules de transport aussi imposant, le potentiel de l’automatisation se fait indéniablement ressentir dans l’industrie des sables bitumineux. Cependant, sa mise en œuvre requiert une certaine créativité afin de se préparer aux conditions difficiles de la région.
Pour Komatsu, qui travaille de concert avec Suncor depuis 2013 pour adapter les systèmes de transport autonome (AHS, de l’anglais autonomous haulage systems) des fabricants d’équipement d’origine (FEO) que la société a lancés dans le district ferrifère de la région de Pilbara en Australie-Occidentale, les sables bitumineux posaient des problèmes particuliers, notamment en raison des hivers froids et de l’aspect visqueux des corps minéralisés. La préparation à l’hiver et le développement d’un réseau de trajectoires multiples pour les camions afin qu’ils n’endommagent pas les routes ont résolu les problèmes.
Suncor prévoit d’ajouter 150 unités d’AHS dans ses exploitations de sables bitumineux au cours des six années à venir, en commençant par sa mine de North Steepbank. Il ne s’agit pas de la seule société d’exploitation des sables bitumineux qui envisage d’adopter cette nouvelle technologie. En effet, Canadian Natural Resources Ltd prévoit de lancer un petit projet pilote pour 2019.
Les AHS de Komatsu associent des camions autonomes aux équipements et pelles de soutien commandés par des hommes. « Nous disposons de cinq couches de sûreté qui permettent aux humains d’interagir avec les camions autonomes », expliquait Brian Yureskes, directeur du développement des entreprises pour les sables bitumineux à Komatsu. « Certaines sont des couches virtuelles de sécurité, qui permettent au système de voir et d’anticiper ce que les hommes font autour des camions. D’autres sont des couches physiques, par exemple les lasers et les radars. Quant à la dernière couche, chaque équipement actionné par un humain et exploité dans la région dispose d’un gros bouton rouge sur lequel on peut appuyer pour arrêter tous les camions autonomes. »
D’après Scott Schellenberg, dirigeant des AHS auprès de SMS Equipment, le distributeur canadien de Komatsu, la technologie autonome a elle-même énormément renforcé la sécurité. « Les employés travaillant autour des camions de transport autonome peuvent voir sur leur écran où se trouvent les camions, et savoir où ils se dirigent, ce qui n’est pas le cas avec un humain conduisant le camion », indiquait-il.
Les sables bitumineux passent au numérique
Les exploitations de sables bitumineux adoptent de plus en plus les technologies d’apprentissage automatique et d’intelligence artificielle (IA), déclarait Dinara Millington, vice-présidente de la recherche au CERI. « L’adoption est plus rapide depuis que ces technologies ont été commercialisées il y a quelques temps », expliquait-elle.
Marty Reed, chef de la direction d’Evok Innovations, un partenariat entre des sociétés du secteur pétrolier et gazier canadien et la BC Cleantech CEO Alliance (l’alliance des dirigeants des principales sociétés de technologies propres de la Colombie-Britannique), évoque deux technologies innovantes générant des avantages considérables pour le secteur pétrolier et gazier ainsi que pour celui des sables bitumineux. L’une des sociétés, Kelvin, possède un système d’IA déployé dans les champs gaziers et pétroliers de BP à Wamsutter, dans le Wyoming. Des centaines de capteurs peu coûteux ont été installés dans les puits où ils recueillent des données qui sont transmises par l’intermédiaire du nuage vers des ordinateurs performants. Ces données identifient des modèles et font des prévisions, qui sont utilisés pour générer de petites modifications à des fins d’optimisation ; ces modifications sont ensuite renvoyées vers les salles de commande dans le champ.
« L’ère où l’on devait remanier toutes les données dès la moindre modification sera bientôt révolue », indiquait M. Reed. « Les ordinateurs sont plus adaptés à ce genre de tâches. »
La deuxième société, Expeto, a été fondée en Colombie-Britannique (C.-B.) et propose une solution logicielle qui met en relation tous les dispositifs technologiques de l’évolution à long terme (LTE) en toute sécurité. « Si l’on ne parvient pas à envoyer les données dans le nuage, cette technologie n’a plus aucun sens », expliquait M. Reed. « Expeto propose une plateforme offrant aux entreprises un bien meilleur contrôle de tous leurs dispositifs reliés à Internet. La société évolue dans les secteurs pétrolier, gazier et minier. »
Réduire l’empreinte environnementale
À l’heure actuelle, l’industrie des sables bitumineux est responsable de l’émission de 70 mégatonnes de CO2 par an. En 2030, un système gouvernemental de plafonnement des émissions sera instauré en Alberta et fixera la limite d’émissions acceptables de CO2 à 100 mégatonnes par an. Si l’industrie souhaite continuer de croître, il lui reste relativement peu de temps pour réduire l’intensité de ses émissions de CO2.
En 2015, Shell Canada a ouvert la première installation de captage et stockage du dioxyde de carbone (CSC) à l’échelle commerciale pour une exploitation de sables bitumineux, l’installation Quest de CSC, située sur les lieux de l’usine de traitement du bitume Scotford de la société, près d’Edmonton. Trois années plus tard, l’usine a capté et stocké plus de trois millions de tonnes de CO2. Ce système, conçu par Shell, utilise de l’amine pour absorber le CO2 émanant de la combustion des gaz. Il sépare ensuite le CO2 de l’amine et le pressurise en un liquide, qui est transporté à 65 kilomètres au nord par le biais d’une canalisation, puis est injecté à deux kilomètres dans le sol.
Parmi les autres technologies visant à réduire les émissions de gaz à effet de serre (GES) figure la méthode de captage du CO2 par une enzyme, mise au point par la société québécoise CO2 Solutions. Ce procédé est en cours de démonstration dans le cadre d’un projet de captage et d’utilisation du CO2 de 30 millions de dollars à Chimie Parachem, une installation de paraxylène (PX) située à Montréal, détenue à 51 % par Suncor. La construction d’une unité commerciale destinée à l’usine de pâte à papier Resolute Forest Product au Québec est en cours ; elle devrait être opérationnelle d’ici la fin de l’année et injectera le CO2 capté dans une serre voisine. La société a étroitement collaboré avec le secteur pétrolier pour démontrer le bien-fondé de sa technologie. D’après Evan Price, président et chef de la direction de CO2 Solutions, cette technologie peut être adaptée, et le capital et les coûts d’exploitation ne sont pas aussi élevés que pour la technologie à base d’amine.
La méthode de captage du CO2 par une enzyme, mise au point par la société québécoise CO2 Solutions. Avec l’aimable autorisation de CO2 Solutions
Cette technologie repose sur l’anhydrase carbonique, une enzyme également utilisée par les poumons des humains et des animaux pour assimiler le CO2 dans le corps. CO2 Solutions compare sa technologie à un poumon industriel. « Nous utilisons une solution saline carbonatée très simple qui ne génère ni aérosols ni déchets toxiques », expliquait M. Price. « Nous puisons la chaleur nécessaire à notre technologie dans de l’eau chaude provenant de l’usine, et non de la vapeur comme c’est le cas pour les procédés à base d’amine. La vapeur a une grande valeur ; ainsi, utiliser de l’eau chaude et non de la vapeur confère à notre technologie une grande différence de coût, très avantageuse. »
Accélérer la remise en état des exploitations de sables bitumineux est aussi un projet pressant qui a engendré tout un éventail d’approches de la part de l’industrie et d’autres secteurs. Parmi les sociétés en lice figure Technika Engineering de Calgary, qui s’est penchée sur les problèmes rencontrés avec les technologies traditionnelles d’assainissement des résidus fins mûrs (RFM) à l’aide de dragues et de chalands équipés de pompes submersibles.
« Nous étions convaincus qu’il existait une meilleure approche », expliquait Radé Svorcan, président de la société. « Aussi nous avons décidé de la concevoir. »
Technika a développé ce que la société appelle un système de récupération des résidus (TRS, de l’anglais Tailings Recovery System). Les RFM provenant des sables bitumineux présentent une résistance au cisaillement et une viscosité élevées qui augmentent en fonction de la profondeur des bassins, lesquels atteignent généralement 30 mètres. En raison des débris dans les RFM et de leurs propriétés rhéologiques, les technologies traditionnelles d’assainissement à l’aide de dragues et de chalands équipés de pompes submersibles rencontrent des problèmes d’obstruction et de dilution des RFM au point d’aspiration. La technologie TRS utilise une structure en coque télescopique de type caisson située à la surface du bassin et pouvant descendre jusqu’à plus de 15 mètres de profondeur, qui permet d’exploiter le principe de l’équilibre de la pression hydraulique afin de ramener les RFM à la surface. « Les RFM se trouvant en surface dans le TRS, il est bien plus facile de les récupérer et les problèmes liés à la dilution des RFM et à l’obstruction des pompes sont résolus. Nous utilisons la pression hydraulique naturelle pour faire remonter les RFM vers le haut », indiquait M. Svorcan.
Cette technologie, qui a d’ores et déjà prouvé son bien-fondé dans une exploitation de sables bitumineux où elle a été déployée, présente des avantages ; elle permet notamment une récupération fiable sans obstruction tout au long de l’année. Elle est totalement préparée aux conditions hivernales et peut être actionnée à distance. D’après la société, avec un système d’alimentation en RFM de 2 500 mètres cubes par heure (m3/h), le TRS permet de réaliser des économies de l’ordre de 10 à 20 millions de dollars en coûts d’investissement, et de l’ordre de 5 à 10 millions de dollars en coûts d’exploitation, par rapport aux technologies reposant sur les dragues et les chalands.
Une extraction in situ innovante
Stephen Robinson et Graham Manders, deux entrepreneurs spécialisés dans la technologie de l’imagerie, ont décidé de faire équipe avec Osman Malik, un vétéran du secteur pétrolier et gazier, et ont commencé à demander à des sociétés pétrolières de la région des sables bitumineux de l’Alberta quels étaient leurs besoins. De leurs retours est née la société DarkVision Technologies. « Tout le monde souhaite voir ce que contiennent les puits », déclarait M. Robinson. « Ce sont des environnements complexes ; les opérateurs veulent voir ce qu’il se passe à l’intérieur pour pouvoir régler les problèmes et optimiser la production, mais les puits sont profonds, sombres et remplis de fluides opaques. »
En 2013, DarkVision a mis au point une technologie d’imagerie acoustique à haute résolution permettant aux opérateurs de voir à l’intérieur de leurs puits au travers des fluides épais. L’année dernière, la société a installé des bureaux à Calgary et compte désormais cinq clients, dont Suncor, MEG and ConocoPhillips. « Nous avons encore beaucoup de produits complémentaires à développer, et nous sommes très loin du but », déclarait M. Robinson.
Dans le monde de l’extraction in situ des sables bitumineux, on parle beaucoup des technologies à base de solvants, qui pourraient remplacer les technologies traditionnelles d’injection de vapeur requérant beaucoup d’eau et de gaz afin de rendre moins visqueux le bitume trop profond pour être extrait, de manière à le recueillir et à le pomper vers la surface.
La société américaine Harris a développé HeatWave, une technologie qui repose sur la méthode avancée d’extraction par solvant au moyen de chaleur électromagnétique (ESEIEH, de l’anglais Enhanced Solvent Extraction Incorporating Electromagnetic Heating) associant des solvants, de la chaleur électromagnétique et une antenne radio placée dans le sol qui réchauffe le bitume.
Nsolv, une autre société basée à Calgary, a mis au point un système à base de solvants sans eau qui a été testé pendant trois ans dans les sables bitumineux. Ce projet a pris fin en 2017, après avoir permis la production de 130 000 barils de pétrole. La technologie est prête au déploiement commercial.
Nsolv injecte dans le dépôt de bitume de la vapeur pure et chauffée de propane provenant d’une usine à basse pression. Lorsque la vapeur atteint le bitume, elle le condense et le réchauffe légèrement. « Le propane liquide et le bitume légèrement mouvant se mélangent très bien », expliquait Joseph Kuhach, chef de la direction de Nsolv. Cette vapeur permet de suffisamment liquéfier le bitume pour le faire remonter en surface.
Par rapport au drainage par gravité au moyen de vapeur (DGMV), expliquait M. Kuhach, ce procédé présente l’avantage de réduire les émissions de GES de 70 à 80 %, et la construction d’une grande centrale hydraulique s’avère inutile. Ceci permet de réaliser des économies de 40 % en termes de coûts d’investissements.
Par ailleurs, ajoutait M. Kuhach, le procédé développé par Nsolv élimine les asphaltènes et les séquestre dans le dépôt.
Par rapport à une production classique, ce bitume partiellement valorisé requiert moins de la moitié du diluant nécessaire pour répondre aux spécifications relatives au transport par canalisation. À l’heure actuelle, les canalisations de l’Ouest canadien doivent respecter un indice de gravité établi par l’American Petroleum Institute (API, l’institut américain du pétrole) de 20 à 22 degrés. De nos jours, le bitume affiche généralement un indice de 8 à 10 degrés API ; les indices du bitume produit par Nsolv sont de 13 à 14 degrés API.
Pour les sables bitumineux, les répercussions d’une réduction de la quantité de diluant dans les canalisations vont bien au-delà d’une simple réduction des coûts des diluants. De fait, entre 30 et 40 % du bitume transporté par ces canalisations n’est pas du pétrole, mais des diluants, une pratique inefficace qui est encore plus prononcée étant donné les tentatives infructueuses de développer le réseau de canalisations.
Augmenter le débit de pétrole pour réduire le goulet d’étranglement
« Comment peut-on augmenter le débit si l’on ne construit aujourd’hui aucune nouvelle canalisation ? », déclarait Mme Millington. « L’une des façons d’y parvenir est de réduire la quantité de diluant que requiert le bitume afin de répondre aux spécifications relatives au transport par canalisation, de manière à ce que le diluant n’utilise pas outre mesure la capacité précieuse des canalisations. »
Des sociétés d’exploitation des sables bitumineux et des innovateurs œuvrent au développement de technologies de valorisation partielle qui permettent d’augmenter la quantité, la qualité, et par là même la valeur du bitume transporté à partir des gisements de sables bitumineux.
La société québécoise Fractal Systems, par exemple, a mis au point et testé une technologie de valorisation partielle baptisée Enhanced JetShear. En février dernier, la société annonçait que le système JetShear permet de réduire la quantité de diluant de 50 à 60 % et d’augmenter la capacité de transport de bitume par canalisation de 20 à 25 %. Le système JetShear repose sur le craquage thermique léger et par cavitation hydrodynamique pour modifier la structure des molécules d’asphaltènes du bitume sur le site d’extraction et réduire sa viscosité ainsi que sa densité apparente. Fractal Systems indiquait que sa technologie, qui inclut des tuyères d’éjection propriétaires, est prête à être commercialisée.
En outre, la société Alberta Innovates a établi un partenariat avec des sociétés dont les technologies de valorisation partielle se trouvent en phase de démonstration. Cette étape requiert l’exploitation de 1 000 barils par jour, expliquait Murray Gray, conseiller technique principal de la valorisation partielle du bitume à Alberta Innovates. L’une de ces sociétés, MEG Energy, possède un système qui fournit un bitume partiellement valorisé prêt à être transporté par canalisation sans utiliser de diluant. Cette technologie, baptisée HI-Q, associe le craquage thermique au désasphaltage. Une autre société, Nexen Energy, propose un procédé baptisé BituMax, qui associe le désasphaltage au craquage thermique, mais dans l’ordre inverse de la technologie HI-Q. La société Husky Energy, quant à elle, adopte une approche différente ; son système amalgame le bitume à du pétrole brut synthétique, puis traite ce mélange.
« Nous espérons que d’ici deux ou trois ans, plusieurs technologies de valorisation partielle seront prêtes à être déployées dans le commerce », déclarait M. Gray.
En ces périodes d’incertitude, la commercialisation devient difficile. D’après l’association canadienne des producteurs pétroliers (ACPP), les dépenses totales en capital dans les sables bitumineux ont considérablement chuté, de 34 milliards de dollars en 2014 à environ 15 milliards de dollars en 2016.
« Comment investir des capitaux dans une technologie qui n’a pas fait ses preuves à l’échelle commerciale ? », indiquait Mme Millington. « La première société à présenter une nouvelle technologie est toujours celle qui prend le plus de risques. Ainsi, la question est de savoir comment éliminer les risques inhérents à cette technologie pour accélérer la commercialisation du procédé. »
En février, le gouvernement de l’Alberta proposait au moins une solution partielle au problème ; il injectera au cours des huit années à venir un milliard de dollars en prêts et subventions dans la construction d’installations de valorisation partielle dans la province. « Nous considérons ce partenariat avec le gouvernement comme une étape très importante qui permettra de propulser ces technologies au-delà du rang de la démonstration à une échelle suffisante », indiquait M. Gray.
Une voie parsemée d’innovations
Aucune technologie ne peut à elle seule résoudre les problèmes liés à l’exploitation des sables bitumineux ; cependant, « le potentiel des technologies innovantes à révolutionner l’industrie des sables bitumineux est indéniable », indiquait Mme Millington.
Object reference not set to an instance of an object.
Plus dans la catégorie Technologie
La révolution de l'automatisation
Cela ne fait aucun doute, l'avenir de l'industrie minière passe par l'automatisation. Cependant, à quoi ressemble cet avenir et par quel chemin allons-nous y arriver?
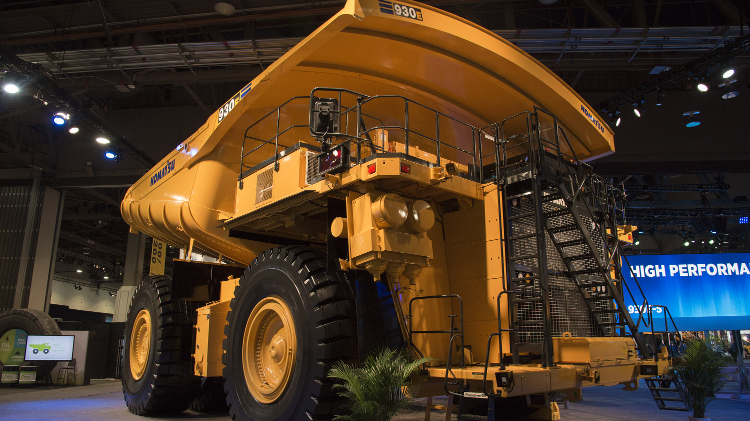
La conscience des coûts dans la ville que l’on surnomme « Sin City »
Efficacité et rendement : la philosophie du dernier Minexpo