La surveillance des équipements a permis à la mine d’améliorer sa disponibilité à l’aide de la maintenance préventive. Avec l’aimable autorisation de Hecla Mining
Lorsque Hecla Mining a lancé son offre pour Casa Berardi en 2013, une partie de sa présentation aux actionnaires de Mines Aurizon Ltée portait sur l’expertise qu’avait cette société, alors âgée de 120 ans, en matière d’exploitation minière souterraine en roche dure, comme en témoignaient ses exploitations en Idaho et en Alaska. À l’époque, la capacité moyenne du concentrateur à Casa Berardi était de 1 600 tonnes par jour. Fin 2017, cette capacité avait pratiquement doublé pour atteindre 3 551 tonnes par jour.
La production à Casa Berardi a commencé en 1989 ; son exploitation s’est poursuivie jusqu’en 1997, date à laquelle la mine a été placée en mode de soins et maintenance. La production commerciale a repris en 2007. Aujourd’hui, l’usine de traitement reçoit du minerai de deux zones minières souterraines ainsi que d’une mine à ciel ouvert peu profonde, dont la production a commencé en 2016. Les méthodes d’extraction employées dans la mine souterraine sont l’exploitation transversale par gradins en trous profonds pour les minéralisations plus larges, et l’exploitation rabattante longitudinale pour les corps minéralisés plus étroits. Actuellement, la durée de vie de la mine est estimée à neuf ans.
Alain Grenier, vice-président de Hecla Québec et directeur général de Casa Berardi, se dit satisfait des économies et des progrès réalisés. Il dirige la mine depuis quatre ans, et supervise un certain nombre de grands changements, notamment un remaniement complet du calendrier de production, le déploiement de machines autonomes et actionnées à distance, ainsi que l’installation de technologies de communication et de télémétrie qui permettront de stimuler la production et de renforcer la sécurité.
À DÉCOUVRIR : Pour accéder à l’or se trouvant sous terre à sa mine Goldex, Agnico Eagle a donné sa chance à un système de transport innovant
La première étape consistait cependant à améliorer le procédé minier avec les équipements existants.
La société s’est tout d’abord concentrée sur l’ordonnancement, la planification et l’amélioration de l’exploitation en s’appuyant sur son infrastructure existante. Elle s’est ensuite attelée à la construction du garage souterrain et du réseau de cheminées à minerais et à stériles, puis a investi « énormément de temps » dans la planification du calendrier de production. En 2015, la capacité quotidienne du concentrateur de l’exploitation avait augmenté de 600 tonnes, portant à 2 200 tonnes sa capacité de traitement quotidienne.
Des étapes franchies grâce à la technologie
Fin 2015, Hecla a investi 200 000 dollars dans un brise-roche actionné à distance par des employés en surface, et a développé en interne des technologies d’extraction automatisée et de chargement à distance. L’extraction automatique a permis de déplacer 120 tonnes de minerai supplémentaires par jour ; par ailleurs, ces trois technologies offraient toutes un environnement de travail plus sûr aux employés, qui restaient désormais en surface.
« La mise en œuvre de ces technologies a permis de combler le creux entre les postes du matin et ceux du soir, ces deux heures dont nous avons besoin pour évacuer la poussière et la fumée », déclarait M. Grenier, faisant référence à la plage horaire durant laquelle les employés changeaient de poste et les machines ne pouvaient fonctionner. « Nous avons ensuite décidé d’automatiser le forage d’exploitation. Ceci nous a permis de gagner au moins 15 mètres par jour et par forage, et nous sommes passés de 335 mètres à 350 mètres par jour ; c’est un gain considérable ».
En 2016, Casa Berardi devient la troisième exploitation au monde (derrière la mine Finsch de Petra Diamond en Afrique du Sud, et la mine Hemlo de Barrick en Ontario) à investir dans les nouveaux camions articulés TH540 à benne basculante de 40 tonnes de Sandvik pour ses mines souterraines. Ce camion, commandé et actionné depuis une salle en surface, améliore les charges utiles de 8 % et réduit l’utilisation d’énergie de 17 %, ce qui, d’après M. Grenier, est un grand avantage.
À DÉCOUVRIR : Les exploitants et fournisseurs de sables bitumineux cherchent des moyens de réduire les coûts d'exploitation et les émissions
« Pendant les huit premiers mois d’exploitation, le premier Sandvik TH540 automatisé a offert une disponibilité de 20 % supérieure à des coûts d’entretien de 25 % inférieurs à la moyenne pour un camion du parc automobile de la mine conduit par un humain », déclarait M. Grenier.
Au vu de l’achat des deux nouveaux camions Sandvik, l’ancien parc de camions de transport souterrain AD30 de Caterpillar sur le site a été réduit à neuf camions (treize initialement). Hecla a installé des capteurs pour la télémétrie sur deux des camions plus anciens afin de contrôler leur emplacement ainsi que les données relatives à la performance de chaque engin en temps réel. Les AD30 équipés de capteurs sont envoyés de la mine Ouest à la mine Est, car le forage d’exploration génère de nouvelles réserves dans la mine Est.
« Nous surveillons la température du moteur et de l’huile, les données de transmission, la charge utile et bien entendu, la pression des pneus », indiquait M. Grenier, expliquant les avantages de la maintenance préventive et la capacité à réparer des problèmes mécaniques ou à remplacer des pièces avant que ne se produise une panne ou que n’ait lieu l’entretien systématique. « Les mécaniciens sont désormais en mesure de régler des problèmes sur les camions avant les entretiens prévus. C’est la raison pour laquelle nous avons pu augmenter de 8 % le volume de minerai traité par l’équipement souterrain. »
La transition vers l’automatisation n’a toutefois pas été simple. Si le nouveau jumbo automatisé S2C d’Atlas Copco a permis une hausse de 17 à 20 % en termes de mètres forés par poste, et s’il a fait l’unanimité auprès des opérateurs, un problème s’est bel et bien posé lorsque Hecla a tenté de moderniser deux de ses anciens jumbos de plus de dix ans en 2017.
« L’une des difficultés que nous rencontrons est de nous assurer que les résultats soient conformes aux attentes », indiquait M. Grenier. « Si les [rénovations] fonctionnent comme convenu, les travailleurs seront contents ; dans le cas contraire, ils ronchonneront. »
Harmonie entre les hommes et les machines
En revanche, les systèmes d’extraction automatisée et de concassage de roches à distance ont été bien accueillis par le personnel, en partie car ils ont été conçus en interne. En surface à la mine Casa Berardi, les employés commandent à distance l’engin de lavage à pression et trois stations de concassage des roches souterraines qui ont été conçus, programmés et installés sur place.
« Nous sommes très fiers de notre système d’extraction automatisée », indiquait M. Grenier. « Nous avons obtenu de l’aide pour la programmation du treuil d’extraction minière, mais c’est notre équipe en interne qui a fabriqué tous les dispositifs permettant de l’automatiser, même la commande à distance pour les quatre unités hydrauliques de concassage des roches. »
Conformément à l’Occupational Safety and Health Administration (OSHA, l’agence gouvernementale fédérale des États-Unis dont la mission est la prévention des blessures, maladies et décès dans le cadre du travail), le taux de fréquence des accidents à la mine Casa Berardi en 2017, calculé à l’aide d’une formule relative aux normes de l’industrie, se situait à 4,1 % par travailleur, soit moins d’un tiers du taux qui prévalait en février 2014, lorsque la société affichait un taux record de 15,8 %. La télémétrie, expliquait M. grenier, a eu une grande incidence sur la sécurité des travailleurs. Dans des zones où le personnel continue de travailler en souterrain, nous avons installé des capteurs sur l’équipement de manière à reconnaître les employés, et des dispositifs permettant d’éviter les collisions sont ajoutés à l’équipement lourd.
« Si l’équipement devient de plus en plus volumineux, les hommes, eux, gardent la même taille », déclarait M. Grenier. En 1997, un camion de 15 tonnes constituait un équipement énorme ; à l’heure actuelle, la mine possède des camions de 40 tonnes et certaines exploitations envoient même sous terre des camions de 60 tonnes. Il est de notre responsabilité d’installer des dispositifs permettant d’éviter les collisions avec les hommes. »
Malgré la transition vers l’automatisation, la société a embauché 200 personnes supplémentaires. En mai 2018, la mine comptait 950 employés, par rapport à 2014 où l’effectif s’élevait à 750 personnes. Le groupe de travailleurs qui évolue le plus rapidement reste indéniablement les techniciens de l’information. Sur le site, quatre spécialistes des technologies de l’information travaillent aux côtés d’au moins 10 techniciens de la programmation, de l’instrumentation et du contrôle, et d’une quinzaine de spécialistes de la communication et du contrôle.
Déploiement d’un réseau d’interconnexion par fibre optique
« Nous nous trouvons dans une nouvelle ère du mode d’exploitation », expliquait M. Grenier. « La prochaine étape pour nous consistera à nous doter de la technologie d’évolution à long terme (LTE), qui nous permettra d’utiliser les téléphones portables sous terre. » Hecla espère déployer cette technologie d’ici 2020 dans le secteur Est de la mine, ce qui permettra aux travailleurs sous terre d’échanger des données avec les employés en surface par le biais de téléphones portables et de tablettes.
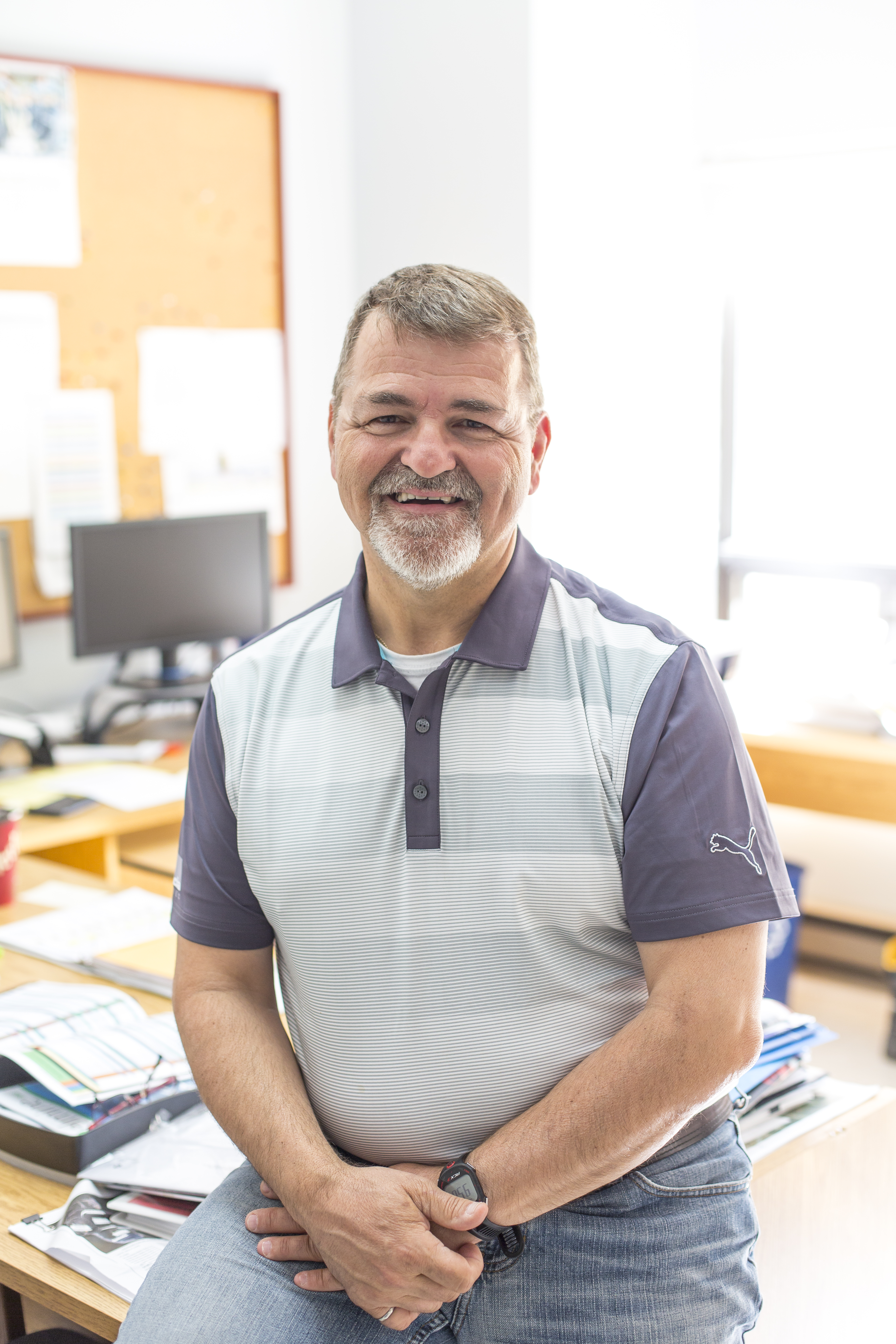 |
Alain Grenier. Avec l’aimable autorisation de Hecla Mining/Mathieu Dupuis
|
Afin d’assurer le bon fonctionnement des systèmes de télémétrie installés sur les engins mobiles, des points d’accès sans fil portables sont en cours de déploiement partout dans la mine et sont installés sur certains véhicules de service ou utilisés par les superviseurs. En outre, d’ici la fin 2018, 15 points d’accès sans fil (les hotspots) seront installés dans des lieux stratégiques, et le réseau sera développé en 2019 et 2020. Hecla prévoit de continuer à déployer le WiFi sous terre en installant « l’épine dorsale » d’un réseau de câbles à fibres optiques dans le secteur Ouest de la mine souterraine, et de déployer la technologie LTE dans la mine à ciel ouvert et le secteur Est de la mine souterraine. Hecla collabore avec la société montréalaise Newtrax spécialisée dans la technologie pour éliminer le fossé numérique qu’il existe actuellement entre les exploitations à ciel ouvert et souterraine. L’objectif est de parvenir à une meilleure communication entre les hommes et l’équipement. Grenier se dit satisfait de la série de nouvelles technologies d’automatisation désormais rassemblées à la mine Casa Berardi ainsi que des améliorations qu’elles ont permis en termes de sécurité, de production et d’environnement. Cependant, il attend aussi avec impatience la prochaine génération pour Hecla, celle de l’interopérabilité à la mine.
« Dans les trois années à venir, les camions et les pelles se reconnaîtront, j’en suis convaincu », déclarait-il. Globalement, le processus consiste à rapprocher la mine du concept d’« industrie 4.0 » (ou industrie du futur), un réseau interactif associant robotique, capteurs et machines régulés par des algorithmes informatiques guidés par les données et contrôlés par le biais d’Internet et par ses utilisateurs dans toutes les exploitations de Hecla, tout en restant très axé sur les résultats finaux.
« Notre décision de nous tourner vers l’automatisation a été motivée par notre désir de garantir la durabilité de notre exploitation et des emplois », indiquait M. Grenier. « Nous avons orienté nos efforts sur la manière de renforcer la production tout en améliorant la sécurité de nos employés et en ne portant pas atteinte à l’environnement, et nos coûts ont diminué. Nous avons désormais en main les outils qui nous permettront de faire face à divers cycles économiques. »