Le nouveau crible vibrant portable de la série Tyler F Class de Haver & Boecker vise à faciliter le changement rapide des supports de crible. Avec l'aimable autorisation de Haver & Boecker
En matière d'optimisation, le criblage, s'il est essentiel au processus d'extraction, est souvent considéré comme acquis. « La direction prête peu attention au criblage car il s'agit d'une dépense mineure », déclarait Les Naday, directeur de la stratégie d'entreprise chez Polydeck Screen.
C'est une erreur qui peut coûter cher. En effet, le criblage peut engendrer des frais très élevés en termes d'inefficacité, de révision et de temps d'immobilisation, surtout lorsque ce dernier n'est pas prévu.
« Dans une grande exploitation, tout doit être planifié ; ainsi, il est important que les supports de cribles durent au moins le temps des cycles d'entretien de l'équipement de proximité », indiquait M. Naday. « Les coûts de mise à l'arrêt d'un broyeur SAG peuvent atteindre 500 000 $ l'heure. Lorsqu'un élément aussi peu coûteux qu'une grille de crible se brise, et que ce problème entraîne l'arrêt d'une machine qui coûte autant par heure d'immobilisation, les sommes perdues sont énormes. »
Les mêmes difficultés à plus grande échelle
L'une des principales raisons des bris des cribles vibrants est ce que l'on appelle le colmatage, à savoir lorsque des fines restent collées à la surface du crible. « Le colmatage rend pratiquement impossible l'utilisation de la machine », indiquait Claes Larsson de Metso Minerals. Le goujonnage (ou piquage), à savoir lorsque les roches bloquent la surface, est un autre problème.
« C'est de loin la plus grande difficulté », expliquait M. Larsson, « où que l'on aille. »
Les inefficacités liées au criblage peuvent également entraîner d'autres problèmes, par exemple l'envoi d'une quantité excessive de fines dans le broyeur. « Les fines qui ne sont pas éliminées par le criblage finissent par fatiguer le broyeur, car ce dernier ne peut pas broyer une masse solide de matériaux. Il faut de l'espace entre les roches qui sont envoyées dans le broyeur. Peuvent en découler des centaines de milliers de dollars de coûts d'entretien, mais la source du problème ne sera pas toujours facile à déterminer par l'opérateur », ajoutait M. Larsson.
Si les cribles sont résistants, ils peuvent aussi être sensibles. « Lorsqu'on répare les cribles, la machine peut se retrouver en situation de très léger déséquilibre », déclarait Peter Kilmurray, vice-président des ventes chez Haver & Boecker Canada. « Ceci suffit à perturber la distribution égale des roches dans le châssis, rendant l'opération inefficace et générant une usure irrégulière. »
Alors que le compteur tourne en termes de dollars, le remplacement des grilles de supports de cribles même dans le cadre d'un entretien prévu à quelques semaines d'intervalle n'est une procédure ni rapide ni simple. « On doit généralement retirer environ 18 pièces simplement pour remplacer le support d'un crible », expliquait M. Kilmurray. « C'est une procédure coûteuse et délicate. »
De nos jours, les exploitations minières optent en outre pour des broyeurs semi-autogènes (broyeurs SAG) et des concasseurs à cône à plus grande capacité, aussi les cribles deviennent de plus en plus grands pour pouvoir s'adapter aux capacités croissantes. « Il y a vingt ans, le plus grand crible sur le marché mesurait environ 2,5 mètres. Puis on est passé à 3 mètres ; aujourd'hui, les cribles de plus de 4 mètres sont monnaie courante, et ils deviennent de plus en plus grands », indiquait M. Larsson.
Ceci signifie que l'innovation en matière de conception de cribles vise de plus en plus à faciliter l'entretien et à le rendre plus rapide, ainsi qu'à réduire le poids des cribles, tout en améliorant leur résistance à l'usure, leur performance et leur fiabilité.
Conception basée sur la réalité virtuelle (RV, encore appelée conception en zigzag) d'autonettoyage des cribles de Polydeck, présentée ici à côté de grilles traditionnelles à trous carrés. Avec l'aimable autorisation de Polydeck
Des matériaux plus performants
« Ces dix dernières années, Polydeck a créé des matériaux présentant une dureté variable, aussi nous faisons face aux problèmes d'obturation et de colmatage en proposant différentes conceptions de grilles dotées d'une fonction d'autonettoyage », indiquait M. Naday.
Contrairement aux supports de cribles métalliques traditionnels, les cribles autonettoyants sont fabriqués avec des matériaux flexibles, qu'il s'agisse de fils gainés qui vibrent indépendamment ou des grilles de cribles de Polydeck en caoutchouc fabriquées par moulage par injection, de manière à pouvoir libérer les fines du colmatage ou les roches trop grandes bloquées par piquage. Polydeck utilise le moulage par injection plutôt que par compression ou par havage de manière à garantir une cohérence et une fiabilité optimales. « Le moulage par injection permet d'éviter les variations dans le matériau de manière à ce que chaque grille soit utilisable pour la même durée », expliquait M. Naday.
Les plastiques traditionnels en polyuréthane sont également de plus en plus remplacés par des caoutchoucs synthétiques et naturels. « Le caoutchouc aide beaucoup pour les problèmes de colmatage car les membranes des grilles de cribles recouvertes de caoutchouc souple vibreront, aussi l'effet de nettoyage du support de crible est renforcé, et le colmatage est considérablement réduit », indiquait M. Kilmurray.
Cependant, aucune grille de crible n'est universelle et ne s'adapte à toutes les applications. C'est la raison pour laquelle de nos jours, on trouve une multitude de supports de cribles différents sur le marché, sans oublier que les experts ont tous des opinions divergentes quant à la meilleure option, qui n'est pas forcément toujours la plus agressive. « Un compromis est toujours possible, aussi nous avons plusieurs façons de nous attaquer à chacune de ces questions en fonction de l'application ; en effet, si on les fabrique trop souples, la durée de vie du crible sera écourtée », indiquait M. Naday. « Il faut les faire juste assez souples. »
Un entretien plus rapide et plus simple
Les sociétés fabriquant des cribles travaillent depuis un certain temps sur les conceptions afin de réduire le temps et les efforts nécessaires à l'entretien de leur équipement. Polydeck, par exemple, a remplacé les inserts métalliques par des inserts synthétiques qui réduisent le poids de la grille de près d'un kilogramme (kg) par 0,09 mètre carré (m²). « Sachant que l'on compte 240 grilles par plateforme, la réduction de poids est considérable », indiquait M. Naday. « L'impact sur la durée de vie et les autres pièces du crible sera positif. »
Il y a deux ans, la société Haver & Boecker a lancé son système de fixation des godets formés de deux parties de la série Tyler F Class, qui permet de réduire de moitié le temps d'immobilisation nécessaire à l'entretien en offrant un accès facile aux pièces essentielles. « En cas de problème, il nous fallait auparavant deux jours et trois ou quatre personnes pour démonter l'arbre en raison des grands bras fixés de part et d'autre de la machine », expliquait M. Kilmurray. « Nous avons donc conçu un godet formé de deux parties. Ceci nous permet de diviser les bras en deux, et ainsi de n'avoir à en retirer qu'un seul. »
L'année dernière, la société est allée encore plus loin lorsqu'elle a présenté Ty-Rail, un système qui élimine les boulons et verrous traditionnels en les remplaçant par un dispositif de tension qui maintient le support en place et réduit de moitié le temps d'entretien. « Ce dispositif contient des pièces non démontables et se glisse vers l'intérieur ou l'extérieur », indiquait M. Kilmurray. « Nous n'avons plus besoin de deux, mais d'une seule personne.
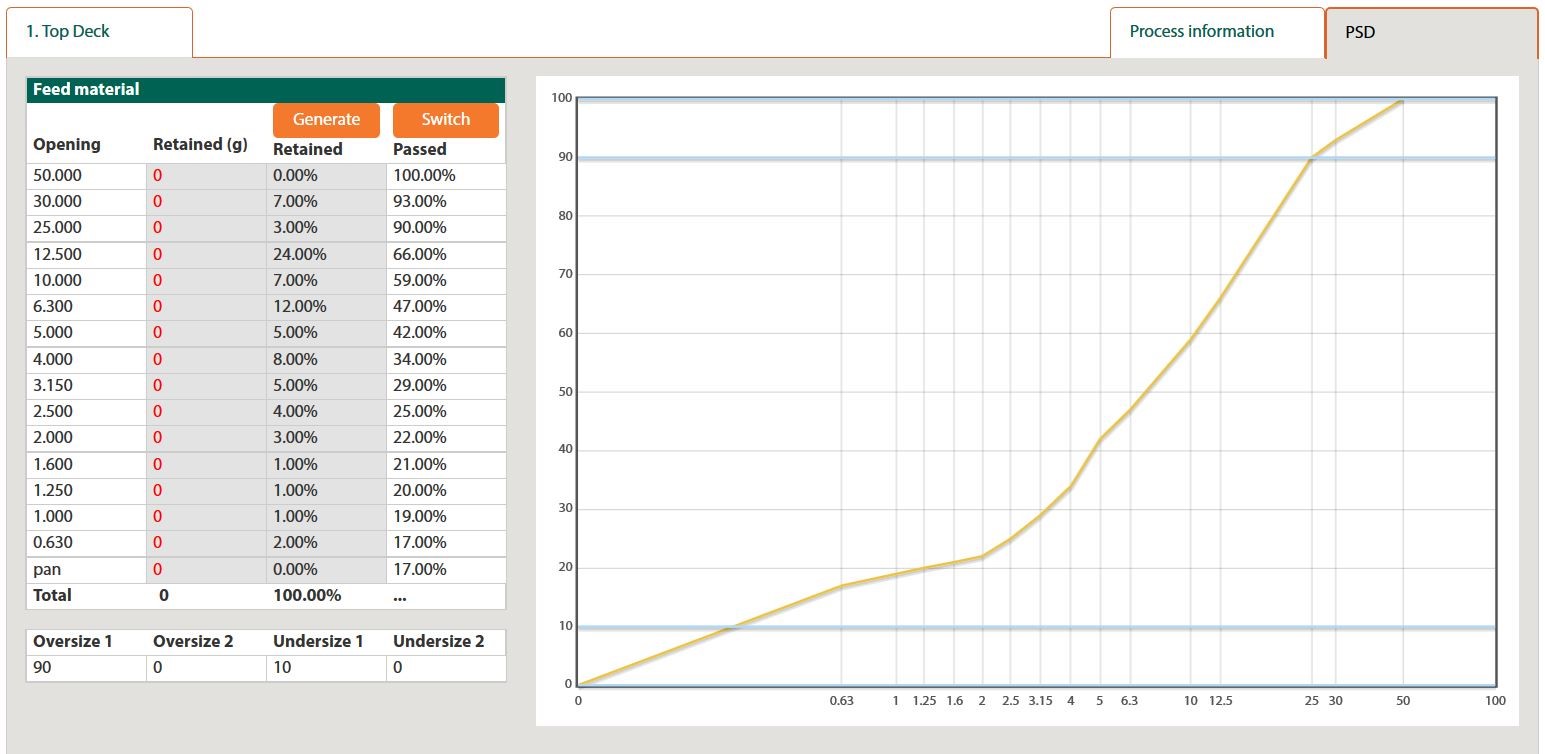
L'application Screen Planner de Metso surveille les performances des supports de cribles et leur durée de vie en fonction de l'usure | Avec l'aimable autorisation de Metso
En route vers la haute technologie
La haute technologie est aussi arrivée dans la sphère du criblage. FLSmidth dispose d'un analyseur de mouvement à écran mobile qui enregistre les vibrations du crible et offre une analyse immédiatement après que les données aient été recueillies. Le service d'analyse des vibrations Pulse de Haver & Boecker offre une solution matérielle et logicielle à l'exploitant minier permettant d'enregistrer la vibration du crible. Les données sont envoyées aux ingénieurs de la société, qui les analysent et émettent leurs recommandations.
Ensuite, nous avons le contrôle en temps réel. Le système ScreenWatch de Metso utilise des capteurs sans fils autoalimentés pour surveiller de manière continue les performances et l'état du crible vibrant, puis pour alerter l'exploitant en temps réel dès qu'un problème est détecté, qu'il s'agisse d'une alimentation irrégulière, de boulons desserrés, de ressorts cassés ou de supports usés. « On peut donc s'assurer que tout fonctionne comme prévu », ajoutait M. Larsson.
Screen Planner, le logiciel le plus récent de Metso, permet de suivre l'usure en temps réel et d'analyser la performance pour une optimisation. « Lorsqu'on met le crible en marche, on saisit dans le logiciel tous les paramètres de performance que l'on souhaite surveiller ; on peut ensuite contrôler numériquement l'usure en ligne », indiquait M. Larsson. « Toutes les données de surveillance sont recueillies, ce qui permet d'analyser l'historique. Après un certain temps, on peut distinguer des tendances. Par exemple, on peut identifier les pièces affichant la durée de vie la plus courte et déterminer la marche à suivre pour y remédier. »
Nombre d'experts sont d'avis que la technologie de surveillance pour le criblage deviendra une tendance prédominante dans les années à venir. Dès que l'on recueille et que l'on analyse des données, l'optimisation devient bien plus réalisable et vérifiable, ouvrant ainsi la voie à davantage d'innovation.
Traduit par Karen Rolland