Systèmes en phase

Le secteur minier innove peut-être, mais de façon archaïque et fragmentée. Il lui reste encore à se doter des outils du XXIe siècle capables de donner naissance aux innovations de ruptures et aux percées technologiques qui ont catapulté d’autres secteurs vers l’avenir – jusqu’à aujourd’hui.
Les technologies des systèmes d’information, de communication et de contrôle s’étendent aux moindres aspects d’une exploitation minière. Plus que jamais, les usines de traitement du minerai ont recours à l’automatisation pour repousser les limites de l’optimisation à un rythme accéléré. Les technologies numériques, parmi lesquelles le GPS, le sans-fil et les capteurs, sont utilisées sur l’équipement minier mobile pour améliorer la sécurité, la productivité et l’efficacité, de même que pour réduire les collisions et optimiser le fonctionnement et l’entretien.
Une des percées les plus fameuses dans le secteur a eu lieu dans le domaine de l’équipement autonome, comme l’ont démontré à grande échelle des sociétés minières importantes telles Rio Tinto, BHP Billiton et Fortescue Metals Group. Au centre des opérations de Rio Tinto, à Perth (Australie), 400 employés contrôlent à distance, à quelque 1 000 kilomètres en amont, l’ensemble des 15 mines de minerai de fer de Pilbara ainsi que son imposant système de roulage ferroviaire. Sur le site du projet minier Solomon Hub de Fortescue, en Australie-Occidentale, 47 camions autonomes Caterpillar sont à l’oeuvre 24 heures sur 24, 7 jours sur 7. BHP Billiton mène aussi des essais avec un parc de 15 camions autonomes Caterpillar sur l’un de ses sites miniers, à Pilbara. En outre, l’entreprise est en train de mettre en place 20 foreuses de trous de mine autonomes, fabriquées par Atlas Copco, dans cinq de ses sites miniers de Pilbara ; elles seront mises en service d’ici à la fin de l’année, commandées à distance depuis le centre des opérations de l’entreprise, à Perth.
Et ce n’est que le début. « À mesure que la technologie des capteurs évoluera, les outils de chargement automatisés deviendront la norme (et continueront d’évoluer), tout comme les camions, les foreuses et les tracteurs miniers automatisés, a souligné Michael Murphy, ingénieur en chef des techniques minières à Caterpillar. La mine autonome a beaucoup plus progressé que ne le reconnaissent la plupart des entreprises minières. »
Tous ces progrès prennent place isolément. Chaque fabricant met au point son propre équipement et utilise ses propres logiciels et systèmes. Les usines de traitement ont leurs propres systèmes. Les sites d’excavation minière ont leurs propres commandes et opérateurs.
« Notre entreprise mène actuellement plusieurs projets d’automatisation qui visent à améliorer la sécurité, à accroître la productivité et à réduire nos coûts d’exploitation globaux », a indiqué Graeme Mitchell, directeur du service d’automatisation minière à BHP Billiton. Par exemple, un programme d’essais menés sur le parc de foreuses autonomes de BHP Billiton, à Pilbara, a entraîné une réduction de plus d’un quart des coûts d’exploitation. Cela dit, la mine autonome seule n’est pas le but ultime de BHP Billiton. « Toutes ces initiatives sont des outils clés dans la quête d’un écosystème minier intégré. »
Informations incomplètes
Une exploitation entièrement intégrée qui permet d’optimiser la sécurité, le rendement et la production et de réduire substantiellement les coûts par l’intégration et le partage des processus, des systèmes et de l’information à l’échelle des fonctions d’exploitation et qui se traduit par une prise de décision en temps réel améliorée. Cette optimisation « de bout en bout » constitue la prochaine étape importante pour les sociétés minières. Selon Colin Farrelly d’Indago Partners, une société de conseil en gestion spécialisée dans l’innovation dans le secteur minier, de tels progrès pourraient aider le secteur minier à passer d’un processus de traitement par lot à un processus continu qui réduirait considérablement la nécessité d’accumuler des piles de stockage. Pour y parvenir toutefois, les sociétés minières doivent avoir accès aux données de tous les capteurs, GPS et systèmes logiciels de chacune de leurs activités, autrement dit, du plan d’exploitation minier aux activités de dynamitage, de l’excavation au transport et du traitement à la livraison. Le problème, c’est que chacun des systèmes exclusifs des fabricants d’origine limite de façon très stricte la quantité de données auxquelles les systèmes et l’équipement d’un autre fabricant peuvent avoir accès. L’équipement autonome de Caterpillar fonctionne mieux avec le système Cat MineStar. De même, une foreuse Atlas Copco fonctionne mieux si l’on utilise le système d’exploitation d’Atlas Copco. Aujourd’hui encore, sur le plan de l’échange de données entre les systèmes, une exploitation minière est dans une large mesure une tour de Babel.
En réalité, « une mine de renseignements se trouve stockée dans des machines intelligentes et dans des systèmes de planification minière, a expliqué Graeme Mitchell. Mais en règle générale, ces données sont isolées dans des systèmes exclusifs qui communiquent difficilement entre eux, ce qui rend tout aussi difficile le partage et la circulation de l’information entre les systèmes. »
C’est aussi l’avis de Peter Carter, un ingénieur minier qui a collaboré avec Komatsu à la conception des premiers camions de roulage sans conducteur. Il est aujourd’hui responsable du secteur des métaux et des mines pour OSIsoft, entreprise technologique dont le dispositif PI System élimine les obstacles en établissant un lien entre les données de capteurs et des systèmes pour aider les entreprises à optimiser leurs opérations. À son avis, le potentiel d’optimisation des mines à partir des données utilisées dans l’équipement et les systèmes est énorme. Il donne l’exemple suivant :
« Lorsque les foreuses creusent des trous de mine, un grand nombre de données peuvent être recueillies sur les caractéristiques de la roche rencontrée. Ces données, fondées sur la dureté de la roche et le couple utilisé par la foreuse, peuvent être corrélées avec le modèle géologique d’origine et permettre ainsi de cartographier plus précisément l’emplacement du minerai et de déterminer les techniques d’abattage et de fragmentation à privilégier, a expliqué Peter Carter. Toutes les autres étapes du processus suivent ensuite ce forage. L’information est transmise avec le matériau alors que celui-ci circule le long de la chaîne de valeur, du forage au roulage en passant par le chargement. »
De la même façon, les capteurs placés sur les camions de roulage pour le guidage des machines autonomes recueillent des données pouvant être utiles pour établir une cartographie géologique ou d’autres fins, comme l’entretien des chemins. « Si on constate des vibrations excessives sur un camion pendant le transport, le problème vient probablement du moteur, mais si les vibrations sont présentes sur plusieurs camions, il se peut que la route en soit la cause, et la difficulté consiste à le comprendre », a expliqué Colin Farrelly.
Une solution prête à l’emploi
intégration, selon un avis largement partagé de nos jours, est l’interopérabilité. Colin Farrelly, d’Indago, définit ce terme comme étant « la possibilité pour les systèmes des technologies de l’information et des communications, les systèmes techniques d’exploitation et les processus d’affaires qu’ils hébergent d’échanger des données et de permettre le partage d’informations et le transfert de commandes. Cela permet alors aux systèmes et aux entreprises de collaborer harmonieusement (l’interopérabilité). »
Bien qu’il existe différentes définitions de l’interopérabilité, celle qui est proposée ici a été élaborée par Indago à l’issue de consultations et d’études menées auprès 88 personnes représentant 66 organisations de l’ensemble du secteur minier, dont principalement des sociétés minières et des fournisseurs, notamment d’équipement, ainsi que des consultants, des ingénieurs et des fabricants de technologies d’exploitation. Les conclusions de son étude – réalisée pour le compte d’AMIRA International, organisation mutuelle mondiale de sociétés minières et de fournisseurs – ont été publiées en avril 2016.
Schématiquement, l’interopérabilité consiste à connecter harmonieusement entre eux l’ensemble des équipements et systèmes d’une exploitation minière de sorte qu’ils communiquent et fonctionnent ensemble, sans égard à leurs fabricants. « C’est lorsque les choses peuvent s’accorder et échanger entre elles et que des systèmes variés peuvent être mis en contact et fonctionner comme un tout plutôt que comme des solutions isolées, a résumé Tim Skinner, président de SMART Systems Group et consultant travaillant depuis des décennies sur le défi sans cesse renouvelé que représente l’interopérabilité dans les mines. Vous connectez tous ces éléments, et ça fonctionne. Voilà ce que nous cherchons à réaliser. »
C’est assurément ce que des sociétés minières comme Rio Tinto et BHP Billiton cherchent à faire. Mais, en ce qui concerne l’interopérabilité, a fait remarquer Colin Farrelly, le secteur minier a 20 ans de retard sur les autres secteurs, notamment ceux de la fabrication, de l’agriculture et du pétrole et du gaz.
Il existe cependant une exception : le traitement du minerai.
« Les usines de traitement du minerai ont un degré d’automatisation et d’interopérabilité nettement plus élevé, mais ce n’est pas parce que le secteur minier a oeuvré en ce sens, a expliqué Colin Farrelly. Cela tient au fait que la construction d’une usine de traitement du minerai n’est pas fondamentalement différente de la construction d’une usine de fabrication ou d’une plateforme pétrolière. Toutes sont des variantes d’une usine de traitement; toutes les technologies qui sont mises en oeuvre dans une usine de traitement du minerai sont conçues par des fournisseurs qui les ont déjà créées pour d’autres industries, qui se situent à un niveau plus élevé de développement technologique sous-tendu par les normes de l’industrie. »
John Mulcahy, directeur de la division des systèmes miniers du groupe Croissance et Innovation de Rio Tinto, aimerait voir ce degré d’interopérabilité s’étendre au reste des activités minières. « Dans la salle de commande d’une usine de traitement bien conçue, un opérateur se sert d’un seul ensemble d’écrans qui lui permet de faire tout ce qu’il a à faire ; l’environnement d’exploitation est extrêmement intégré, et il n’est pas nécessaire de sauter d’un système à un autre : l’interface hommemachine, très structurée, est en phase avec tous les processus, a-t-il expliqué. Si l’on pense à des choses comme la gestion d’une mine à ciel ouvert et la gestion d’un parc, on a affaire à des systèmes et plateformes différents, et une personne doit constamment passer de l’un à l’autre. Une machine qui ne peut pas échanger avec d’autres, même si elle peut déplacer des montagnes, forer des puits ou faire quoi que ce soit d’autre, ne vaudra jamais une machine capable de faire la même chose tout en interagissant. »
Possibilités illimitées
Dans les années 1990, le World Wide Web souffrait de nombreuses limites et comprenait plusieurs réseaux concurrents. Aujourd’hui, grâce à l’interopérabilité, il change le monde et constitue une source infinie d’innovation qui a transformé notre quotidien en nous donnant des possibilités autrefois inimaginables. C’est grâce à l’interopérabilité que nous pouvons transférer des données de n’importe quel ordinateur personnel, peu importe son fabricant, à n’importe quel dispositif USB, ou encore télécharger d’innombrables applications sur des téléphones intelligents Android, peu importe, encore une fois, leur fabricant.
Selon Peter Carter, l’interopérabilité de type « prêt à l’emploi » permettrait aux sociétés minières d’automatiser davantage leurs processus en installant de nouvelles machines qui peuvent communiquer avec les systèmes déjà en place. « Cet outil élimine les obstacles à l’innovation et accélère le rythme de cette dernière, a-t-il expliqué. L’interopérabilité est un élément clé de l’innovation, car très peu de nouveaux investissements à grande échelle vont basculer d’un seul coup vers l’automatisation à 100 % (ou l’atteindre). Une telle démarche accroît les risques présents. Ainsi, les sociétés minières n’automatisent habituellement, au départ, que certaines parties des processus, par exemple le roulage, et ils automatisent progressivement les autres processus tout au long de la durée de vie de la mine. »
Toutefois, il ne s’agit pas là de la seule raison pour laquelle l’interopérabilité peut permettre la création d’un environnement novateur qui présente un fort potentiel de transformation et dans lequel les opérations sont accélérées.
« Si on dispose d’une connectivité et de données ouvertes et illimitées, on a entre les mains un environnement novateur qui ne présente pas de frontières », a déclaré Tim Skinner.
Cela s’explique entre autres par le fait que les plateformes, les directives et les protocoles ouverts et partagés attirent les petits acteurs et les entreprises en démarrage. On assiste alors à l’émergence d’un genre d’innovation propre à secouer tout un secteur, c’est à dire à la naissance de technologies révolutionnaires, à la formulation d’idées de nouvelle génération axées sur la transformation ainsi qu’à l’arrivée de nouveaux acteurs, partenariats et modèles commerciaux et opérationnels. « La plupart du temps, l’innovation (ou, à tout le moins, l’innovation authentique et transformatrice) finit par venir des petites entreprises et des entreprises en démarrage, a déclaré Colin Farrelly. Lorsque l’on dispose d’un environnement technologique interopérable ouvert, il est plus facile d’y intégrer un nouveau logiciel. Il y a 10 ans, l’écriture et le déploiement d’une application mobile étaient très difficiles. De nos jours, des jeunes du secondaire peuvent développer une application pour téléphone intelligent. Et l’application sera compatible avec le système d’exploitation en place et elle fonctionnera avec les autres données. »
Comme l’interopérabilité est fondée sur le partage, elle élimine également les barrières reliées à la mentalité du XXe siècle axée sur la compétition, le cloisonnement et l’exclusivité, pour plutôt favoriser l’esprit de collaboration. Dans le cadre de la démarche d’interopérabilité, une entreprise peut même faire équipe avec des entreprises concurrentes afin d’assurer le succès d’un projet donné, au bénéfice de chacune.
Un micro exemple d’un tel projet est le camion 6900XD MBT-40 (« MBT » signifiant « Multi Body Transformer », et « 40 », « 40 tonnes ») de Western Star. Par exemple, ce camion peut se présenter initialement sous forme de camion citerne et être transformé rapidement en camion à remorque à benne à déchargement latéral ou en camion à benne basculante avec branchements hydrauliques, entre autres options. À l’intérieur de la cabine du camion se trouve un boîtier de commande générique sur lequel est déposée une matrice amovible qui indique toutes les fonctions de l’équipement en cours d’utilisation sur le camion. Cette matrice change donc d’une option à l’autre. Il y a trois ans, lorsque John Tomlinson de Western Star a imaginé ce concept, il savait que la meilleure manière de le concrétiser était de collaborer avec des concurrents. Son entreprise ne disposait pas de toutes les ressources nécessaires pour pouvoir y arriver seule. La commercialisation d’un véhicule qui peut se transformer en trois types ou plus de camions ne cadre pas avec la démarche d’un grand fabricant dont le modèle d’affaires consiste à vendre différents types de camions. Toutefois, elle peut être avantageuse pour une petite entreprise qui cherche à se démarquer de la concurrence grâce à une offre novatrice de pointe. « Notre arrivée dans le marché de la construction hors route est récente ; nous jouissons donc d’une bonne perspective », a affirmé John Tomlinson.
Au début, lorsqu’il présentait son projet, il avait souvent droit à des regards sceptiques. Toutefois, il a fini par convaincre Carco Industries et Palfinger de travailler au projet.
« Tout le monde a signé une entente de non divulgation. Chacun a convenu de ne pas voler les idées des autres, a poursuivi John Tomlinson. Chaque partie avait sa spécialité et a donc intégré son produit au concept du camion. Chacune des entreprises a de nombreuses bonnes idées, mais quand vous rassemblez toutes ces idées, le résultat final est encore meilleur. L’enjeu consiste à employer une plateforme neutre. » Dans la technologie de l’information et des communications, cette plateforme neutre est l’interopérabilité.
Pour y arriver
L’interopérabilité ouvre un champ de possibilités inédit ; toutefois, pour qu’elle devienne la norme, une collaboration doit avoir lieu à l’échelle de l’industrie. De tels changements ne se font pas par magie. Internet est devenu plus ouvert grâce au World Wide Web Consortium, lequel avait pour objectif de réunir un groupe d’acteurs internationaux provenant de divers horizons qui allaient convenir de plateformes ouvertes et de normes communes. La plateforme de téléphonie intelligente mobile Android est le résultat des travaux de 84 organisations et fabricants qui se sont réunis en 2007 pour créer le consortium Open Handset Alliance.
Le secteur minier n’a pas encore fait de pas de ce genre. Mais la situation est en train de changer. Pour le moment, ce sont des dizaines d’organisations et d’initiatives qui rassemblent les acteurs de cette industrie. AMIRA a récemment lancé un second projet appelé Interoperability Round Table, qui s’adresse aux sociétés minières, aux exploitants miniers contractuels et au gouvernement. « Voilà pour nous une excellente occasion, soit celle de participer aux balbutiements d’une initiative en matière d’interopérabilité qui pourrait prendre une grande ampleur dans le secteur », a déclaré Colin Farrelly.
Au cours de l’automne dernier, le comité technique sur les mines de l’Organisation internationale de normalisation (ISO) a créé un nouveau sous comité ayant pour mission de se consacrer aux activités minières autonomes et il a invité Tim Skinner, le représentant canadien de l’organisation, à présider ce nouveau sous comité. Une autre organisation dont les travaux portent sur l’interopérabilité, soit The Earth Moving Equipment Safety Round Table, est une initiative mondiale qui réunit de grandes sociétés minières et des fabricants d’équipement d’origine (FEO) et dont l’objectif consiste à améliorer les concepts d’exploitabilité et de maintenabilité. Elle élabore notamment des critères et des protocoles destinés à la mise au point de systèmes de détection et d’avertissement de proximité grâce auxquels tous les éléments matériels mobiles dotés d’une technologie de détection particulière pourraient communiquer librement les uns avec les autres.
Un des acteurs clés de ce secteur depuis 2012 est le Global Mining Standards and Guidelines Group (GMSG). Ce groupe, qui est établi au Canada et relève de l’Institut canadien des mines, de la métallurgie et du pétrole (ICM), a été fondé cette année là pour faciliter la mise en oeuvre de solutions et de technologies sectorielles dans le cadre de collaborations entre les acteurs du secteur minier à l’échelle mondiale. Il a lancé plusieurs groupes de travail dont le rôle est d’étudier différents aspects de l’interopérabilité. Il y a d’ailleurs eu, au sein de l’un de ces groupes, consensus entre exploitants et FEO concernant la définition d’ensembles de données embarqués à bord du matériel mobile qui devaient être librement accessibles aux propriétaires dudit matériel, en lecture seule et en temps réel. Cet accord visait à résoudre un problème persistant. Pour arriver au consensus final, le GMSG a tenu une série de cinq ateliers auxquels participaient de grands groupes provenant de sociétés minières et de FEO, et qui étaient dirigés par un facilitateur indépendant impartial.
« Nous avons réussi à réunir, dans un climat de sécurité et de neutralité, des gens ayant tous comme volonté de résoudre un problème de longue date », a souligné Heather Ednie, directrice générale du GMSG, dont les membres proviennent de l’ensemble du secteur minier, y compris toutes les grandes sociétés minières et la plupart des FEO.
« L’industrie fait face à de nombreux défis qui sont apparus en raison de la très grande importance accordée au principe de l’exclusivité dans le cadre des activités de développement de technologies. Notre principe directeur d’ouverture consiste à changer cette situation, a expliqué Heather Ednie. Il faut délaisser la mentalité de l’exclusivité ; c’est ce qui est d’ailleurs en train de se passer. Au GMSG, nous le constatons par le simple fait de voir tout le monde maintenant réuni autour de la même table. Une fois en place l’ensemble des directives, des protocoles ou des normes, il sera possible de mettre en oeuvre les activités de développement et l’innovation nécessaires pour propulser l’industrie vers l’avant. »
Certes, l’innovation se manifeste déjà à l’échelle du secteur minier. Toutefois, jusqu’à maintenant, il n’existe pas beaucoup de liens entre les différents efforts déployés en ce sens. Pour cette raison, l’industrie a maintenant de la difficulté à se défaire de la réputation qu’elle a d’être lente à adopter les nouvelles technologies. Il faut se servir du pouvoir de l’interconnectivité pour donner à l’innovation la vigueur voulue tout en réduisant les risques. Tous les experts s’entendent pour dire que l’interopérabilité s’en vient. Ce n’est qu’une question de temps, de travail et de collaboration. Une fois que l’interopérabilité sera une réalité répandue, le secteur minier et ses innovateurs pourront s’appuyer sur une force d’une grande puissance.
« C’est vraiment au cours des deux dernières années que tout a commencé », a déclaré Heather Ednie.
Traduit par CNW
Object reference not set to an instance of an object.
Plus dans la catégorie Technologie
La révolution de l'automatisation
Cela ne fait aucun doute, l'avenir de l'industrie minière passe par l'automatisation. Cependant, à quoi ressemble cet avenir et par quel chemin allons-nous y arriver?
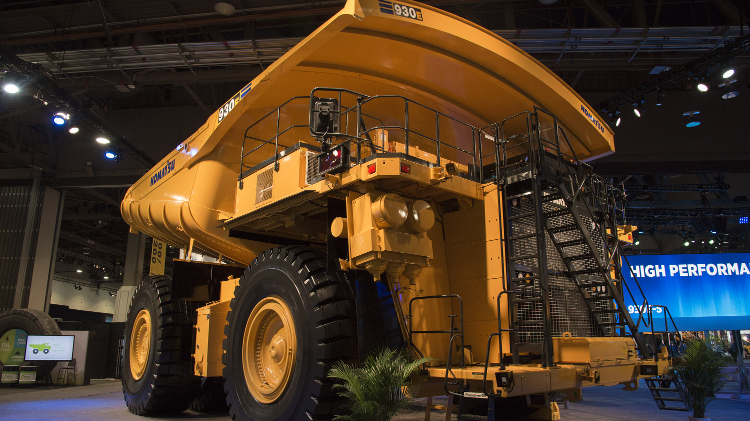
La conscience des coûts dans la ville que l’on surnomme « Sin City »
Efficacité et rendement : la philosophie du dernier Minexpo