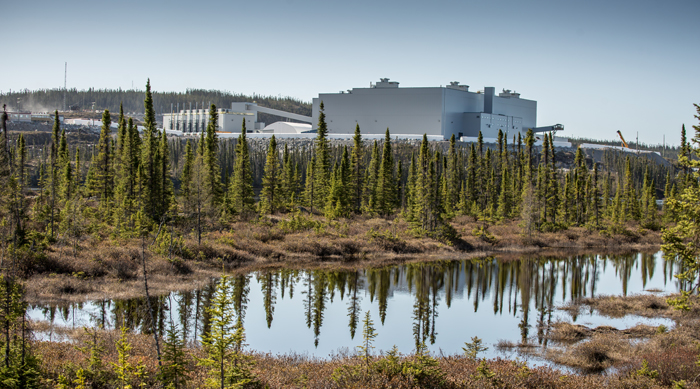 |
À la fin du mois de mai, l'usine de traitement Renard a été dotée des principaux équipements et commandes de processus industriels | Toutes les photos sont aimablement fournies par Stornoway Diamonds |
La mine Renard est située dans la région de la baie James, au Québec, à environ 250 km au nord de Mistissini. Peu après avoir fait l’acquisition du projet en 2007, Stornoway a bénéficié de programmes provinciaux de soutien au développement de l’industrie minière. Le programme de financement par actions accréditives du Québec a permis à la société de financer ses activités d’exploration pendant la crise du crédit. En 2011, lors du lancement du Plan Nord, ambitieux programme de développement des régions nordiques de la province, Renard était l’une des propriétés vedettes nécessitant, à juste titre, un investissement provincial dans les infrastructures régionales. L’étude de faisabilité publiée cette année prévoyait que la durée de vie de la mine serait de 11 ans, en fonction de réserves minérales probables de 18 millions de carats. Dans un plan d’exploitation dont la mise à jour a été publiée en mars, la durée de vie de la mine a été portée à 14 ans, par suite d’une augmentation des réserves, qui se chiffrent maintenant à 22,3 millions de carats.
Stornoway a fait équipe avec d’autres sociétés minières et diverses collectivités pour planifier la construction d’une route de gravier utilisable en toute saison. Ce projet, le premier à être approuvé dans le cadre du Plan Nord du Québec, prolonge la route 167 de 260 km en direction nord et « fait de Renard la seule mine de diamant avec une route toutes saisons au Canada », a souligné Matt Manson, chef de la direction de Stornoway. La Société a utilisé un prêt de 77 M$ du gouvernement provincial pour construire les derniers 100 km de la route ainsi qu’un aéroport pour transporter le personnel et les entrepreneurs.
Une fois la route terminée en 2013, Stornoway a réuni tout son budget d’investissement à temps pour entreprendre les travaux de construction en juillet 2014. M. Manson a déclaré : « Nous avons pu dire aux investisseurs : “Écoutez, tout est prêt, la route, l’aéroport, les permis, nous pouvons y aller. Nous avons juste besoin d’argent.” »
Le montant total des immobilisations nécessaires pour lancer la production commerciale à Renard se chiffre à 776 M$. Sans la route, nous n’aurions disposé que d’une courte période de six semaines pour les livraisons en hiver, sans compter tous les problèmes de surconstruction et de surstockage et les erreurs éventuellement coûteuses que cela aurait.
La route a non seulement permis d’effectuer les livraisons en temps opportun, mais aussi d’utiliser une source d’énergie novatrice : le gaz naturel liquéfié (GNL). « Le fait d’être la première mine de diamant au Canada desservie par une route a aussi permis d’en faire la première mine au pays dotée d’une usine fonctionnant au GNL », a mentionné M. Manson. Puisqu’un raccordement au réseau électrique aurait coûté quelque 170 M$ en infrastructure, l’étude de faisabilité de 2011 préconisait l’utilisation de groupes électrogènes diesel classiques. Cependant, grâce à la route, on peut transporter quotidiennement par camion depuis Montréal le GNL qui permet d’alimenter des groupes électrogènes Caterpillar au coût de 0,18 $/kWh, au lieu de 0,30 $/kWh avec le diesel.
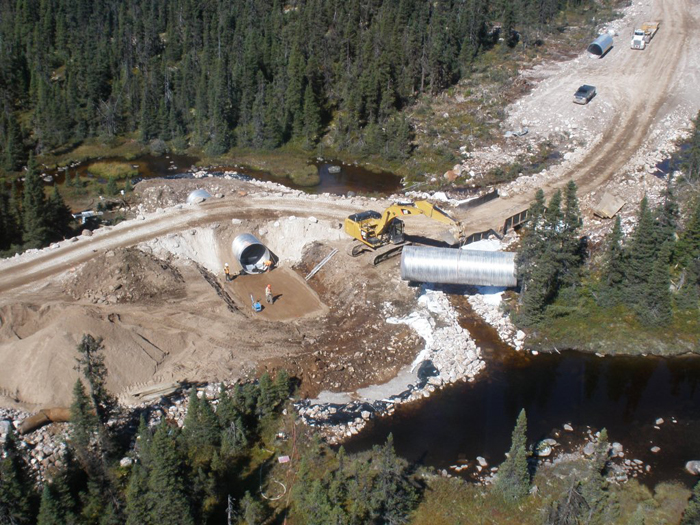 |
Une route utilisable en toutes saisons (ci-dessus en construction en 2012) a permis de résoudre la plupart des difficultés logistiques que rencontrent encore certains autres producteurs de diamants canadiens. |
Récupération de diamants de grande taille
Renard se distingue également d’une autre façon : elle est la première mine de diamant au monde à inclure la récupération de diamants de grande taille (LDR, pour « large diamond recovery ») dans son schéma de traitement primaire. « La méthode normale pour calculer la teneur et la valeur d’un gisement diamantifère n’attribue qu’une part très peu importante des recettes estimées aux diamants d’un poids supérieur à 10,8 carats », a déclaré M. Manson. Cependant, l’une des kimberlites du projet – Renard 2, d’où proviendra la plus grande partie de la production pendant les dix premières années – peut produire des pierres de plus grande taille. Les échantillons recueillis jusqu’à présent laissent présager qu’à tous les 100 000 carats, on pourrait récupérer une à deux pierres de plus de 100 carats et de trois à six pierres pesant entre 50 et 100 carats. En période de production à plein régime, on pourrait récupérer 100 000 carats à Renard en quelques semaines.
Les mines ayant une distribution granulométrique grossière sont nombreuses dans le monde, mais M. Manson a indiqué qu’elles ont tendance à installer la technologie nécessaire pour récupérer les pierres de grande taille seulement après en avoir perdu quelques-unes par fragmentation dans le circuit normal de broyage. « Parce que nous avons cette possibilité et parce que celle-ci pourrait avoir une incidence importante sur nos revenus – on parle de sommes importantes ici –, l’usine est conçue de façon à permettre d’emblée la récupération de tels diamants, s’ils existent », a poursuivi M. Manson. Il a insisté sur le fait que, même si on peut prévoir la taille des diamants, on ne peut en prédire la qualité; Stornoway ne communique publiquement aucune estimation des revenus supplémentaires que des diamants de grande taille pourraient rapporter. N’importe quel diamant de grande taille, ce serait excellent.
Après qu’un concasseur à cône a réduit le minerai en particules de moins de 45 mm, tout ce qui mesure plus de 19 mm passe par le cycle complet du circuit LDR, machine de transmission à rayons X fournie par la société européenne TOMRA. « La machine TOMRA XRT est constituée essentiellement d’une courroie à haute vitesse pouvant traiter de gros volumes de minerai », a expliqué M. Manson. « Tout ce qui apparait fluorescent aux rayons X est soufflé par un jet d’air. »
Les autres équipements d’extraction et de traitement du minerai sont les mêmes que ceux utilisés habituellement dans les mines de diamant. Trois kimberlites seront exploitées pendant la première décennie, à la fois sur des sites à ciel ouvert et (à partir de 2018) par une rampe d’exploitation souterraine. De 1,5 million à trois millions de tonnes de minerai seront envoyés par année à l’usine de traitement ; la capacité nominale de traitement de l’usine est de 6 000 tonnes par jour. Le premier cycle de concassage et le passage dans le circuit LDR sont suivis d’un nouveau concassage, d’une séparation par milieu dense pour produire un concentré, d’un autre passage entre des cylindres de broyage à haute pression, puis d’un nouveau cycle dans le séparateur par milieu dense.
Afin de réduire les coûts, Stornoway a remis à plus tard le forage du puits de mine qui était prévu dans la mise à jour de son étude de faisabilité de 2013. La rampe descend en spirale autour de l’emplacement futur du puits, jusqu’à une profondeur d’environ 700 m, soit la base des ressources indiquées. Comme l’a expliqué M. Manson, lorsque le coût d’utilisation de la rampe en profondeur deviendra prohibitif, le puits prendra la relève. Les cheminées kimberlitiques de Renard semblent différer de la forme typique en carotte ; l’une d’elles mesure la même largeur à 1 000 m sous terre qu’à la surface, ce qui incite fortement à construire des infrastructures plus profondes. « Mais il y a beaucoup à faire d’ici là. On pourra y penser quand le moment sera venu », dit-il.
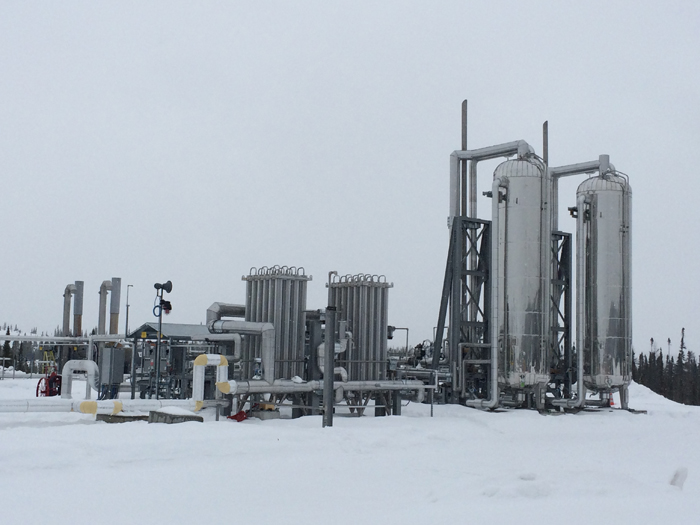 |
La mine produira de l'électricité à partir de gaz naturel liquide (GNL), qui permet de réaliser de grandes économies par rapport au diesel. |
Gestion de l’eau et des résidus
Pour régler la question des résidus à la mine Renard, on a choisi de construire une installation en lisse sèche, ce qui s’explique en partie par l’absence d’une autre solution.
« Au milieu des années 2000, le gouvernement fédéral a décidé de réviser les normes en vertu desquelles il autoriserait le dépôt de résidus miniers dans des plans d’eau », a expliqué M. Manson. « Le gouvernement a donc aboli toutes les normes existantes et commencé à en créer de nouvelles pour l’industrie minière. Il l’a fait pour les métaux communs, pour l’or et pour les métaux précieux. Cependant, en 2008, quand la crise financière a frappé, De Beers Canada a décidé de suspendre temporairement sa production à Snap Lake et à la mine Victor, et le gouvernement fédéral s’est servi de ce prétexte pour cesser de financer l’équipe du ministère de l’Environnement chargée de réécrire les normes pour le dernier secteur minier qui restait, celui du diamant. »
Toujours en l’absence de normes en 2011, Stornoway n’a pu obtenir de permis pour la solution qu’elle privilégiait, une vallée avec un ruisseau. « Nous avons alors choisi comme stratégie de laisser les résidus en lisse sèche », a expliqué M. Manson. « Heureusement, nos résidus ne contiennent pas de métaux. Il n’y a pas de sulfure dans la roche, et donc aucun potentiel d’acidification. Après tous les essais, nous en avons conclu que nous pouvions le faire à un coût très bas. »
Martin Boucher, vice-président, Développement durable, à Stornoway, a souligné que la solution en lisse sèche comprend des avantages inhérents : pas de barrage ni de talus à construire, une demande réduite en eau douce, et une responsabilité moins contraignante après la fermeture du site. « La plupart du temps, quand il faut développer de nouvelles idées, la décision finale est meilleure », a-t-il fait remarquer.
Autrement dit, Stornoway a cherché à devancer le gouvernement. À l’heure actuelle, les règlements fédéraux et provinciaux sur la gestion de l’eau exigent uniquement que les eaux de ruissellement provenant des installations de stockage des résidus soient recueillies et traitées, mais M. Boucher entrevoit des règlements d’une plus grande portée à l’horizon. « Nous détestons les surprises », a-t-il précisé. « Il est bien plus économique de concevoir le site de stockage et de l’aménager pendant la construction plutôt qu’après. Cela coûte deux ou trois fois plus cher alors. »
Stornoway a donc dépensé un peu plus pour aménager un système de fossés de drainage entourant tout le site minier. « Chaque goutte de précipitation, sous forme de neige ou de pluie, qui atterrit sur le site est recueillie dans ces fossés, envoyée à une installation de traitement des eaux où les solides en suspension sont filtrés avant que l’eau soit relâchée dans l’environnement », a indiqué M. Manson.
Le plan de traitement des eaux usées domestiques du projet Renard a également été réévalué en prévision de règlements fédéraux plus sévères sur les toxines. Après avoir soumis le budget à l’attention de deux conseillers pendant une journée, l’équipe de M. Boucher a abandonné l’idée d’une lagune d’aération et opté pour une série de bioréacteurs à membrane produisant de l’eau potable.
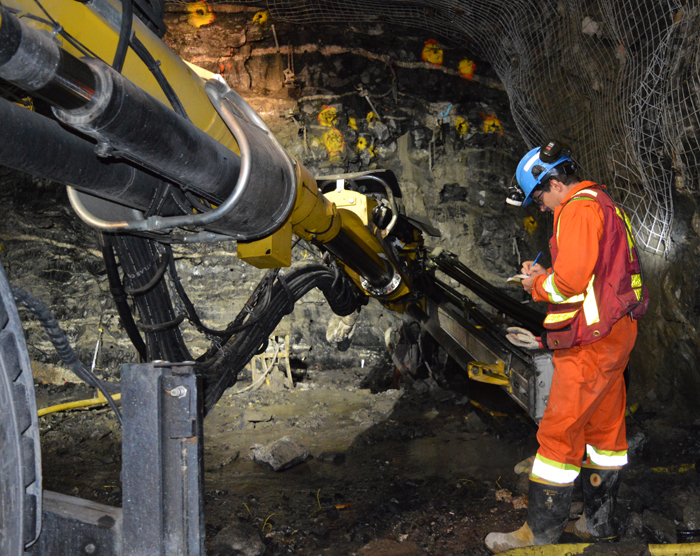 |
La construction d'un plan incliné pour la mine souterraine s'est prolongée sur 1 635 mètres à la fin du mois de mai. À l'automne, l'avancement des travaux en souterrain s'accélérera grâce à l'arrivée d'une seconde équipe de développement. |
Le bon moment
Toutes ces constructions sont allées bon train. Selon M. Manson, la faiblesse du marché minier a fait en sorte qu’il est plus facile de trouver des fournisseurs et des entrepreneurs locaux de qualité qui peuvent travailler dans les limites du budget de Stornoway et qui sont disponibles immédiatement. « Entre le projet de Rainy River à Red Lake, en Ontario, et l’Atlantique, nous sommes la seule mine en construction », a-t-il souligné.
C’est également vrai en matière d’approvisionnements mondiaux. Caterpillar fournit la flotte mobile de la mine. « Quand nous avons réalisé notre étude de faisabilité en 2011, le délai pour obtenir l’équipement de Caterpillar était d’environ dix-huit mois, alors qu’il ne faut maintenant que quelques semaines pour leurs tombereaux de chantier », a déclaré M. Manson.
La rapidité du processus d’approvisionnement et de passation de contrats a réduit de trois mois l’échéancier de la construction à Renard. La productivité à elle seule a permis de gagner un autre mois. En outre, il semble que le délai supplémentaire d’un mois, prévu pour tenir compte des risques, soit superflu. Stornoway s’attend à ce que la mine Renard produise à 60 % de sa capacité nominale d’ici le 31 décembre 2016, soit cinq mois plus tôt que prévu. Par conséquent, le budget d’investissement initial est passé de 811 M$ à 776 M$.
Les coûts d’exploitation pendant la durée de vie de la mine devraient se chiffrer à 56,20 $ par tonne, ou 84,37 $ par carat. Dans sa mise à jour de 2016, Stornoway a estimé que la marge d’exploitation serait de 59 % et, compte tenu des conditions du marché, a revu à la baisse le prix du diamant pour le fixer à 155 $ US le carat. Le second semestre de 2014 et l’année 2015 ont été marqués par une chute importante des prix au comptant, attribuée en grande partie au ralentissement de la demande des consommateurs. Cependant, des signes plus positifs sont apparus en 2016 : le service d’information sur l’industrie des gemmes, Rapaport, a constaté une hausse de la demande des courtiers et du prix des diamants taillés au premier trimestre, tandis que De Beers révisait de nouveau à la hausse son cours vendeur. Le directeur général de De Beers, Philippe Mellier, a évoqué une « reprise fragile » dans une entrevue accordée au Financial Times.
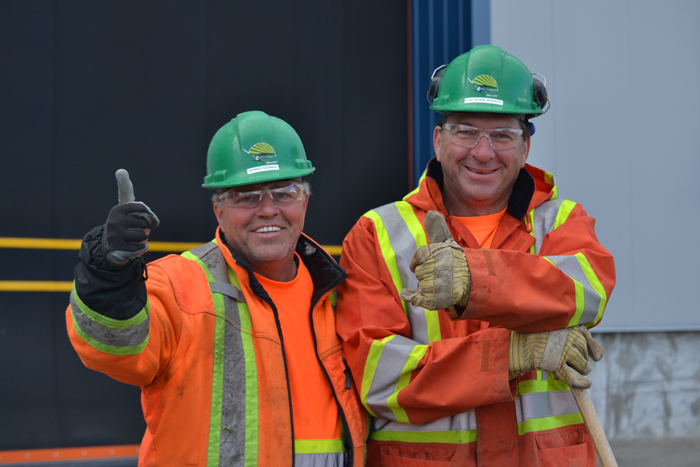 |
Plus de trois quart des dépenses d’investissement, d’une valeur totale de 400 millions $ pour l’année 2015, ont été engagées au Québec | Avec l’autorisation de Stornoway Diamonds |
« Tout le monde veut construire ses projets pendant un cycle baissier et les exploiter pendant un cycle haussier, et nous avons réuni tous nos capitaux au printemps de 2014 », a indiqué M. Manson. « Nous sommes un modèle de bon synchronisme dans le secteur minier. Nous l’espérons. Pas vrai? », a-t-il ajouté en riant. « Nous profitons certainement du cycle baissier pour la construction. Nous espérons profiter du cycle haussier pour l’établissement du prix de notre produit. »
Tant que la mine Renard pourra supporter un peu de volatilité, M. Manson n’est pas inquiet. Il voit de la stabilité dans la valeur culturelle des diamants et dans la relative difficulté de construire de nouvelles mines. « Les diamants sont vraiment difficiles à trouver, et la mise en production d’une nouvelle mine est un long processus. Pour notre mine, il aura fallu 16 ans entre l’étape de la découverte et celle de la production. »
Traduit par CNW et Karen Rolland