Teck Resources took its first foray into dual fuel technology with the conversion of a total of six Komatsu and Caterpillar haul trucks at Fording River. Courtesy of Teck Resources
In North America, the technology to turn liquefied natural gas (LNG) into fuel for vehicle engines has shifted from a stall in the 1960s, to first gear in the early 1980s and then second gear in the last decade as oil prices and climate change concerns soared. LNG is now being used as a clean- burning fuel for thousands of transport and garbage trucks, public transit, school buses and ships. In fact, there are more than 15 truck and bus manufacturers in Canada alone that sell vehicles with integrated LNG dual-fuel engines. No one sells LNG-fuelled mining haul trucks, however. They don’t exist yet – or at least not straight from the factory.
Within the next few years, that is likely going to change. “If you’re looking at the next 25 year cycle,” said Sudhanshu Singh, product manager, large mining trucks for Caterpillar. “This is going to be one of the key areas of focus on haul trucks to reduce fuel cost for our customers at sites with LNG infrastructure.” LNG fuel is simply natural gas cooled down to minus 162 degrees C. The technology was originally developed to transport gas on ships and trucks safely as it does not ignite in its liquid form. For fuel purposes, the liquefied natural gas has to go through vaporizing technology that returns it to its gaseous form. “By the time it gets to the engine, the LNG has been vaporized to its gaseous state at normal temperatures and pressures. So we’re not using the fuel as a liquid directly into the engine the way that you use liquid diesel or gasoline,” said Jason Green, president and chief technology officer for GFS Corp., which has specialized in natural gas conversion technologies for diesel engines since 1988.
LNG produces between 20 to 35 per cent fewer greenhouse gas emissions than conventional transportation fuels and prior to the price of diesel plunging, it came with a 30 per cent fuel cost reduction. Even before the drop in energy prices, dual fuel technology for mining haul trucks lagged behind despite diesel being one of the top two costs of a mining operation. The reason for this is that mining haul trucks are gigantic and operate in extreme and demanding environments. The technology had to be scaled up and ruggedized without compromising the haul truck’s required high torque and horsepower. And it had to work with existing diesel engines.
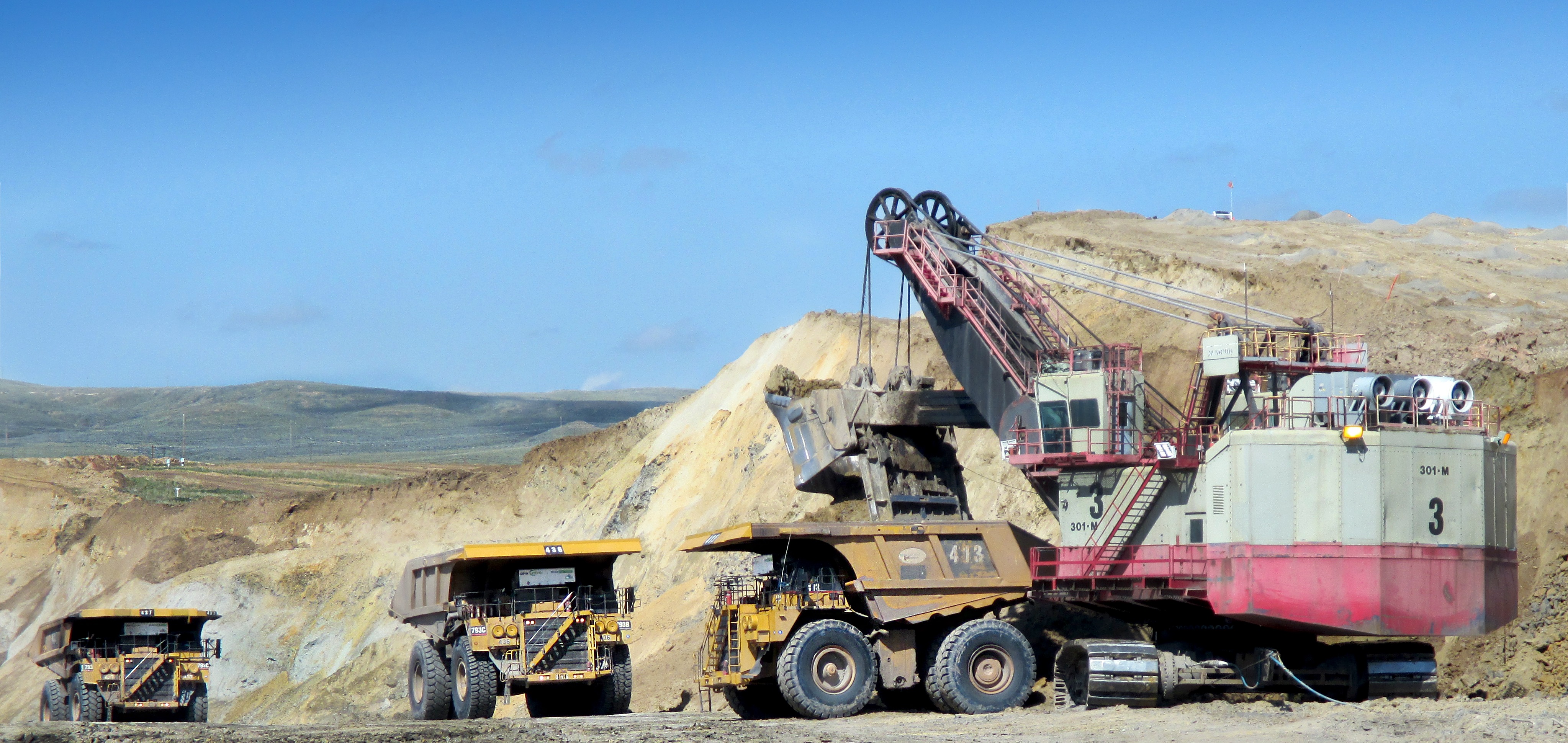
Currently, the quickest route to the fuel savings of a natural gas/diesel mix is through aftermarket conversion, but engine manufacturers are busy developing dual fuel and 100 per cent LNG options. Courtesy of GFS
Retrofitting
“With existing haul trucks, you have to figure out how you introduce this gaseous fuel while keeping all that hardware designed for diesel in place because the truck has to be able to operate on 100 per cent diesel fuel as well,” said Green.
Haul trucks also use a lot of fuel, so enough storage capacity to get the haul truck through at least one full shift is critical. In the past, finding the right place and sufficient space for that in haul trucks has been a challenge.
GFS is confident it has overcome this and all the other challenges. “Our systems allow existing engines to operate safely on natural gas,” said Green. “And then alongside that, for mining products, we’ve designed all the engine hardware and controls and a lot of proprietary LNG storage and vaporization technology to safely store liquid natural gas onboard a mining haul truck.”
In 2013, GFS was one of the first to introduce a retrofit kit for mining haul trucks to the market. Its EVO-MT System is specifically designed to convert the Caterpillar 777 B, C and D; the Caterpillar 793B, C and D; Komatsu 830 DC/AC and Komatsu 930E haul trucks to a natural gas/diesel dual-fuel engine. The system substitutes up to 60 to 70 per cent of the diesel the engine would otherwise use with LNG and has enough storage to keep the engine running 12 hours before it needs to be refuelled with LNG. It comes at a cost of between $150,000 and $300,000 for each conversion depending on truck model. “The performance of the truck is not impacted. In mining there’s no tolerance on the part of the customer even if the system saved them a significant amount of money,” said Green. “If it impacted production or the ability of the trucks to operate, it would be a nonstarter.”
Putting it to the test
This January, Teck Resources launched the first pilot program in Canada testing six Komatsu 830 and 930 haul trucks retrofitted with GFS’s system at its Fording River coal mine in BC.
A critical partner in the project is FortisBC, which owns and operates the only two LNG facilities in British Columbia, one in Delta that goes back to 1971 and the other on Vancouver Island, which was built in 2011. The energy company helped Teck cover the costs of the truck engine conversion as well as providing them with an affordable solution in terms of capital cost: it built an LNG refueling storage facility at Fording River, which it owns and operates. Once the project is complete, Teck will have the option of buying the facility or continuing with the service by FortisBC.
Refueling technology has come a long way and today it is proven and reliable, said Will Smith, LNG and CNG sales manager at FortisBC, although it requires some additional safety measures and training. “You need to wear cryogenic gloves and long sleeves and pants and a face mask in case of splash back,” said Smith. “Fortis does safety awareness and training so they can fuel their trucks.”
He thinks dual-engine technology for haul trucks has arrived. “I don’t believe there’s a technology issue now,” he said.
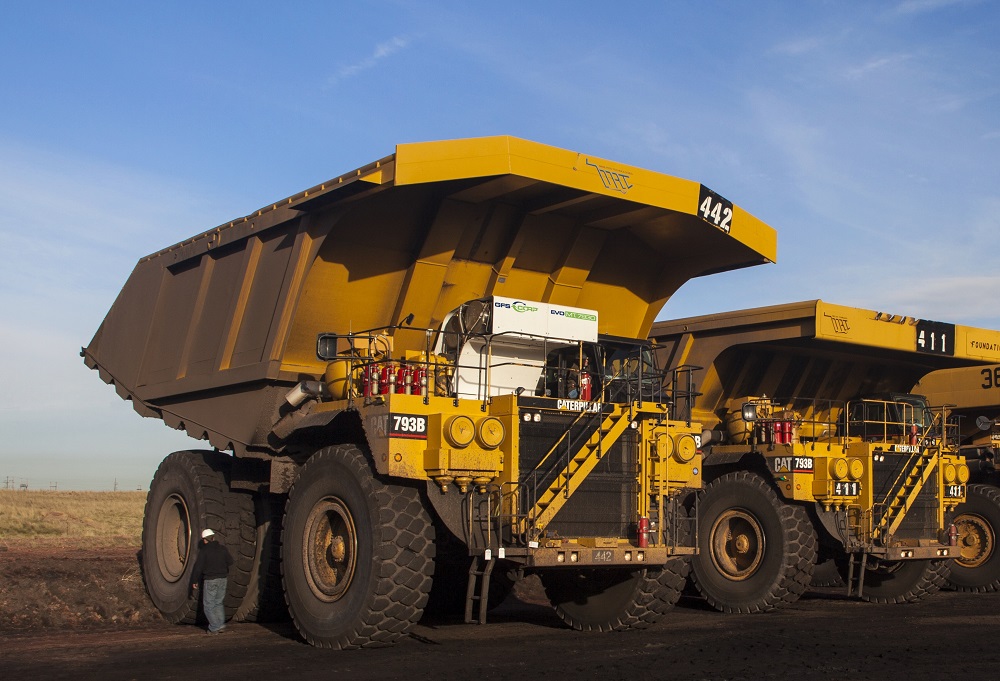
LNG produces between 20 to 35 per cent fewer greenhouse gas emissions than conventional transportation fuels. Courtesy of GFS
In fact, he believes the switch to LNG for mining trucks where LNG is available is coming. What is holding it back is the fact that there are only retrofits for a few models and that no haul trucks are being manufactured with original dual-fuel engines yet. “The biggest change will be an original equipment manufacturing offering from a company like Caterpillar,” he said.
Caterpillar has been testing trucks with LNG. The company has been successful in the petroleum industry with factory fitted LNG solution on engines and is now working on developing dual-fuel technology for haul trucks, including field retrofits for its trucks.
Over the last three years, the company has developed a system it calls dynamic gas blending (DGB) technology for haul trucks in the petroleum industry, which starts the engine with diesel, then switches to LNG and has a substitution rate of 60 to 70 per cent. Now Caterpillar is in the final stages of testing the engine for smaller mining haul trucks aimed at growth markets.
“We’re very pleased with the progress so far,” said Singh. “Our customers want the same experience in the power and torque [as the conventional fuel engine]. They want ease of maintenance. All these factors, and they want it at a lower total cost of ownership on the truck. So we believe our DGB solution on a lower end of the truck, on the 785 model, the 150 tonne size truck, achieves all that.” He added the caveat on conversion that “third party solutions may not deliver the similar level of performance and do not have OEM support with warranty nor a guarantee on the performance of engines.”
More recently, Caterpillar has been working on a LNG/diesel dual-fuel engine for its larger haul trucks, aimed at markets such as North America. It is currently testing this at its labs and working to take the substitution rate to a much higher level than 70 per cent. As well, “The technology will also have significant reductions in greenhouse gases,” said Singh.
According to Singh, the company’s tests so far have shown the new technology will provide the same standard of engine and torque performance as its conventional haul trucks.
“We’re taking the time to develop the technology so we can deliver the best performance to our customers and help them make more money with our trucks than with the competition,” said Singh.
Other manufacturers, however, are not convinced dual-fuel technology is as viable as it once was just two years ago when oil prices were in the $100 barrel range and the potential fuel savings of the dual-fuel engines was around 30 per cent. One of these engine manufacturers is MTU, a subsidiary of Rolls Royce Power Systems. This off-highway engine manufacturer does not believe current dual fuel engine technologies can provide enough natural gas substitution, given today’s low oil prices, to justify the cost of a retrofit and offset the added refueling complexity, according to Ran Archer, MTU’s senior manager of global mining.
As well, he said, not all mining companies have ready access to LNG, although obviously some mines do - in particular those in western USA and Canada. Despite restricted supply of natural gas and more challenging economics relating to low diesel prices, MTU is not abandoning LNG as a fuel source for mining engines. “At this point, MTU’s plan for mining is to offer a 100 per cent LNG engine solution,” said Archer.
Both GFS and Caterpillar believe their dual-fuel engines can still provide fuel savings. And the technology’s reduction in greenhouse gas emissions remains unaffected by oil prices. Teck Resource’s pilot project, for example, could potentially reduce the CO2 emissions at its six metallurgical coal mines by 35,000 tonnes annually. “Natural gas is just a cleaner-burning fuel. It has less particulates and less greenhouse gas emissions than oil. People who have longer term vision realize the advantages of making the move now, since haul trucks are around for so many years,” said Smith. “We’re hopeful Teck will move forward with additional trucks.” And if that happens, he said, other mining operations might follow suit.