Mining within a mazeThe complex process of extracting ore from karst
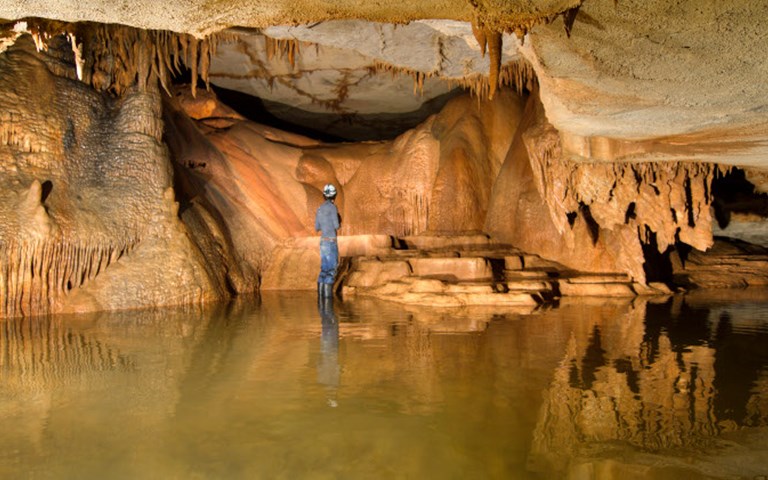
Water is one of the primary concerns in mining. Unless they are correctly managed, water inflows can destabilize pit slopes, flood underground mines and have a dramatic effect on production schedules. In fact, in some cases, water management can be the largest external cost of a mining operation – anywhere from five to 25 per cent of a mine’s operating budget and occasionally higher, says Geoff Beale, a mining hydrologist at Schlumberger. Some of the most unpredictable hydrogeologies – but also some of the most lucrative ore deposits – exist in areas of karst.
Karst is a topography formed in geographies containing carbonate rock, particularly limestone and dolomite, which can be selectively dissolved by water that has become acidic during precipitation and infiltration of the ground. This dissolution of rock creates underground drainage systems characterized by solution-enlarged fractures, sinkholes, disappearing streams, shafts and caves that together can quickly capture an enormous amount of water, discharging it at karst springs. Although these networks include some of the most spectacular caving destinations in the world, they can be daunting for mining hydrogeologists.
Karst exists worldwide – anywhere that carbonate rock is exposed to surface or subsurface water. The properties of karstic features – especially large-scale jointing – make it an excellent host for metallic mineralization. The limestone belt in the Peruvian Andes, for example, stretches for more than 2,000 kilometres, accounts for only 13 per cent of the Andes’ surface area, but contains over 50 per cent of Peru’s metal mines, including Antamina, according to David Evans, managing director at FloSolutions. His company is a Peru-based hydrogeology consultancy specializing in karst. Projects from Nevada to Zambia and from Poland to Indonesia deal with karst and feature some of the biggest dewatering operations on the planet.
In karstic regions, cavities and channels in the carbonate rock are the primary mode of subterranean water transport. The complex fault and fracture systems of karst create discrete, high-volume groundwater flow paths that do not conform to standard hydrogeological permeability models. And worse for the would-be miner is that hydrogeological features in these regions can be so interconnected that the region may have a hydraulic drawdown area in excess of 400 square kilometres. In fact, Barrick Goldstrike monitors water levels over an area of 15,000 sq. km around its mine, in part to ensure mining and dewatering activities do not adversely affect nearby aquifers. Such extensive monitoring is necessary because karstic sources and drains are so difficult to find and correlate, and precise modelling of the subterranean network is nigh impossible.
Nonetheless, for miners, characterizing karstic geology is vital. Everything from drilling and dewatering to slope design and siting of tailings dams depend on the ability of hydrogeologists to map and manage the groundwater systems around a mine. The very economic viability of the mine may depend on the hydrogeologist’s ability to confidently characterize a karstic region.
Formations such as the Haskell Sims cave (pictured) can be spectacular, but also present a major challenge for hydrogeologists attempting to understand them. Courtesy of Chuck Sutherland
Drilling and dewatering
Despite the challenges, however, modern characterization techniques and dewatering capabilities have made mining possible in the most inhospitable of hydrogeological conditions.
Dewatering has significant benefits for many mines, even for those that could operate without it. In open pit mines, dewatering the ground around the pit can help stabilize pit walls, meaning steeper slopes may be possible. “For a large open pit, one degree on the slope angle can mean half a billion dollars in stripping,” says Schlumberger’s Beale. “You can’t change the structure, you can’t change the rock. All you can change is the water pressure.” He figures that, on average, for every dollar spent on dewatering or depressurizing the slope, a mine can reap a $5 payback in slope performance.
Underground mines, meanwhile, may choose to work under the water table, and so exclude water from the mine, or they may encourage inflow for the purposes of dewatering in order to lower the water table to below the level of mining. But either way, the water management plan has to account for labyrinthine karstic hydrogeology. In both underground and open pit mines, the existence of karst complicates dewatering plans.
In Nevada, for example, mine operators at Newmont Mining Corporation must contend with limestone-hosted karst features that store huge volumes of water. The company pumps 16,000 gallons per minute (roughly 1,000 litres per second) from its Gold Quarry open pit, and a further 15,000 gallons per minute at its Leeville underground facility. Next door to Newmont, neighbour Barrick Goldstrike pumps another 16,000 gallons per minute (down from a peak of around 70,000 gallons per minute in the 1990s) from its well-developed karst. The companies have achieved a drawdown of more than 500 metres near the mines since pumping began. Dewatering that volume requires the use of 1,500-horsepower submersible motors driving nine-stage pumps at Gold Quarry, each of which can move between 2,000 and 2,400 gallons per minute against a hydraulic head of roughly 2,000 feet (600 metres). The deeper wells at Leeville mean a pair of 1,500-hp eight-stage pumps must be used to remove 2,500 gallons per minute each against a head of 2,300-2,400 feet.
Related: Monitor, share, innovate, reduce and repeat. This is the new water cycle for mines
The geometry, hydraulic properties and interconnectivity of a given karstic network are often poorly understood and so must be inferred. Drilling is extremely unlikely to find major karstic drains because they are so discrete, and many channels cannot be accessed by cave specialists (known as speleologists) because they are too small to enter or they extend below the water table. Complicating things further is the fact that hydraulic properties can vary by orders of magnitude over very short distances. “We rarely model the individual karstic channels because we rarely know the exact geometric details of the karst plumbing, in terms of size, depth and orientation,” says FloSolutions’ Evans. “Rather, an equivalent hydraulic conductivity is assigned to the principal mapped faults, which are commonly karstified. We can, however, stochastically estimate what the karst system might look like based on known factors and include the karstic drains in the model.”
Dye tracing allows researchers to follow flows through karst formations. Courtesy of Chuck Sutherland
Solving the puzzle
Evans says a preliminary conceptual hydrogeological model must be developed upon which a field program can be built. In parts of Peru, the field program will consist of detailed remote sensing, geological and hydrogeological mapping, speleology, baseline water quality testing, geophysical surveys, dye tracer testing (the gold standard for understanding where flows start and end), drilling, and installation of water pressure-monitoring piezometers. In other areas, the system can be characterized by carefully analyzing large-scale pumping trials. Finally, 3D site-wide numerical modelling can be carried out to predict flows, estimate seepage losses from tailings facilities and run impact analyses.
Despite the many techniques available, there is as yet little agreement on the best way to tackle the challenge of modelling karstic terrain. “There are different philosophies in the industry as to whether you can use standard groundwater models to reflect the fact that a site has karst or not,” says Patrick Corser, the country manager for Canada at MWH Global. “Whether you can characterize the range of variabilities that you’d get in karst, by doing sensitivity [analyses] on fractures, permeabilities and locations, is an issue that is debated a lot in industry right now.”
![]() |
Courtesy of Natural Resources Canada
|
Research on that question and others is ongoing. The Karst Commission of the International Association of Hydrogeologists aims to “promote a defensible scientific basis and professional practice for the sustainable management of karst water resources.” The commission publishes research in the field and organizes conferences and training courses to help promulgate knowledge and best practices.
For now, characterization of karstic geology does not mean knowing exactly what will happen with water flows. But it should mean narrowing down what can or cannot happen, according to Evans. The narrower the range of possibilities, the more precise a dewatering plan can be in terms of required capacity and adequate monitoring.
Dewatering itself is relatively straightforward, once suitable well locations have been determined. Peripheral wells around the mine are out of the way of operations but by necessity deeper, while in-pit (or underground) wells can be shallower but can potentially interfere with operations. The water collected from dewatering wells may be used in the mine plant or simply discharged downstream, sometimes after filtration or treatment.
Nothing is Easy
In Nevada, Newmont’s Gold Quarry and Leeville operations and Barrick’s Goldstrike are located in a relatively dry area of the world with low levels of recharge. Most of their dewatering is storage removal – a semi-permanent drawdown. The Konkola copper mine in Zambia, by contrast, pumps more than three times as much water as Gold Quarry – over 3,000 L/s – from almost 1,000 metres underground, and the Grasberg open pit in Indonesia has to deal with three to five metres of rainfall each year. “They say that water at Grasberg can get from the sky to the dewatering tunnel in as little as a week,” marvels Beale. That compares to a scale of tens of years in non-karstic rock.
Even the most basic of exploratory tasks, drilling for core samples or monitoring wells for instance, take on added challenges in karst. Cavities, either empty or filled, and fractures are impediments to drilling. Newmont typically uses a flooded reverse circulation drilling method, where drilling mud is gravity-fed between the borehole wall and the drill string, before compressed air carries the mud and cuttings back to the surface inside the drill rods. “When you’re drilling the wells, sometimes you’ll just lose circulation” as the mud flows out of the borehole and into a fracture or void, explains Bob St. Louis, the regional hydrology manager at Newmont. Without the hydrostatic pressure of the mud to move the cuttings away from the bit, the drilling assembly can get stuck. Solutions vary by situation, but all add cost, time and difficulty.
Decommissioning wells is similarly challenging, says St. Louis: “It can take a substantial amount of material to properly close them so that they’re no longer a conduit for water to move. Those open fractures or void spaces just consume material like nobody’s business.” One well drilled at Gold Quarry early in the mine life intersected a large fracture, and when the company tried to add stabilization gravel, several tractor-trailer loads of gravel simply disappeared into the well. “It was just pouring out into this very large fracture,” St. Louis explains ruefully. The problems did not end there, either. “When the well was commissioned, that fracture produced so much water that the entry velocities of the water coming into the well were so high that it caused the casing to erode.” The company has to continually rehabilitate the well to keep it in service.
Diligence and perseverance – and no small amount of money – have made seemingly impossible projects viable by removing vast quantities of water from the ground in karstic regions. But surprises can still happen. “Water management strategies have been effective,” cautions Beale, “but because of the discrete nature of the features, you can still get – I wouldn’t say catastrophic – but unanticipated large inflows.” Determining the risk of those potential incidents remains a critical aspect of the mining hydrogeologist’s job when working in karst. Preventing and mitigating them is up to the engineers, like Corser, who work closely with them.
Engineering and tailings
Dealing with waste material can hold surprises at any site, as the August Mount Polley tailings pond breach in British Columbia demonstrated. However, such incidents can be even more problematic in karstic geologies. The challenges are threefold. For one, unsealed surface or subsurface fractures in the foundation of a tailings pond may allow relatively large volumes of contaminated water to enter the karstic network. Once inside these flow paths, waste may travel unimpeded kilometres downstream in unpredictable directions. Secondly, any karstic flow paths near the base of a tailings dam can undercut the dam, washing away dam material and destabilizing the structure. And thirdly, as the tailings pond fills, the increased hydraulic head pressure may enhance development of new and existing conduits and create sinkholes, and can actually increase the downstream catchment area of the karstic network by increasing the height of the local water table. “Realize that with karst, you can’t use standard approaches or standard thinking as to where water or tailings could report to,” says MWH’s Corser. “You need to go into it with your eyes open.”
To meet the challenges of engineering tailings facilities in carbonate-rich regions, both prevention and mitigation strategies are necessary. Looking at what may be affected by a dam failure is the first step. The designer must determine what level of seepage is acceptable based on local geography, ecology and populations. Most importantly, it is critical to get the best understanding possible of the hydrogeological properties of a potential tailings site.
“When developing mine waste facilities in karstic areas, you don’t need a huge cavern to cause environmental and geotechnical problems,” David Evans says. “A karstic pipe just a few centimetres in diameter could cause piping of tailings or high seepage losses from a tailings facility.”
“The characterization of the hydraulic containment for the basin where you’re going to put a tailings facility is very important,” agrees Corser. “That’s your best mitigation against the two biggest risks with karst,” which, he says, are piping of tailings and uncontrolled pond water discharges. “Any tailing facility will leak some amount of water into the groundwater, but it’s a matter of scale. At a karst site, if you encounter a karst feature, you could lose your whole tailings pond.”
That would be disastrous for more than one reason. “Uncontrolled discharge to an unknown location is a problem from an environmental standpoint,” notes Corser, “but it’s also a problem because it could shut your operation down, because you’d have no water to operate with.”
Global distritbution of major outcrops of carbonate rocks (mainly limestone, except evaporites). Courtesy of Ulrichstill
Ideally, a suitable tailings site can be found that is not directly over karst. At a well-characterized site in other geological conditions, it is often possible to show that the surrounding water table is higher than the tailings pond, meaning that the pond is hydraulically contained, and that piping of tailings is unlikely. But that may not be possible for some mines. “The risk with karst is: have you drilled everywhere that there could be a karst feature?” asks Corser. Any undiscovered karstic feature may mean a low local water level and could result in a loss of hydraulic containment.
In many cases, engineered physical barriers may be necessary. Open karstic pipes and conduits that are located in the waste site foundation can be plugged and grouted. Liners made of geosynthetic or, more commonly, geologic materials – low permeability soils – can be used to control the head pressure from the tailings facility. Monitoring and hydraulic control systems installed behind the liners or blankets can measure, collect and pump seepage and outflows before they reach karstic features. Corser also recommends that owners purchase as much land around their mines as possible, so they have access to any areas that karstic tailings flows might report to.
Good exploration and preparation, while expensive and time consuming, is the best approach. Remedial measures – that is, dealing with leaks after the pond is filled – are far more difficult and costly and less effective. “In my mind, it’s better to invest a lot before than trying to deal with it after,” says Neven Kresic, the hydrogeology practice leader at AMEC.
Managing risk
Safety factors must be used for various aspects of design, but like everything else in karst, the factors’ values depend on the local geology. “Safety factors are very site-specific and depend greatly on the degree of karstification, hydraulic gradients to surrounding rivers and springs, and hydraulic containment levels,” says Evans. “There is no rule of thumb yet. One needs to recognize that it is simply impossible to characterize these areas sufficiently to definitively say ‘the risks are low’ – particularly during the feasibility stage when budgets can be tight.”
A colleague of Evans, Petar Milanovic, adopted the mantra “expect the unexpected” after working on the Keban Dam hydroelectric project in Turkey. During that project, Evans says, 36,000 metres of exploratory drilling and 11 km of exploratory adits failed to detect an underground cavern the size of an indoor football stadium.
New sensing techniques may help. Borehole-to-borehole 3D imaging will allow more accurate mapping of features than ever before, with resolutions of potentially a decimetre or better, according to Kresic. “You can also do much better dye tracing tests now than you used to,” he adds, “because you have better probes and they’re cheaper now. So you can insert these probes at different levels or depths in different borings, and then trace between and see where the water is flowing.” Additionally, drilling is getting more advanced, allowing geologists to isolate smaller intervals and image them, looking for cavities. Meanwhile, cheaper processing power lets computer analyses synthesize much more data, creating more accurate models of hydrogeological conditions.
But in spite of everything done to characterize the local hydrogeology and so much careful design to manage and mitigate it, risk is something that miners must make peace with. “You have a lot of unknowns,” emphasizes Kresic. “You have to deal with the risk, and even after spending a lot of money characterizing the site and designing, you have to accept that there will be some risk associated with karst features. You will not be able to find all of them.”
More Environment
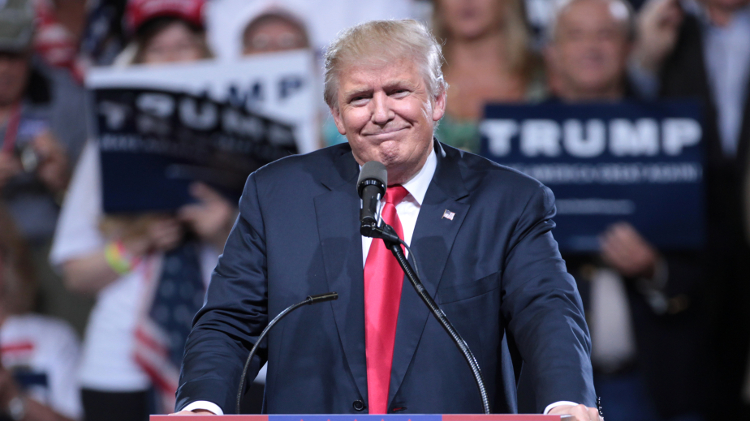
Campaign promises and economic pressures
Market watchers and policy advocates mull over what levers a new, coal-friendly president can pull
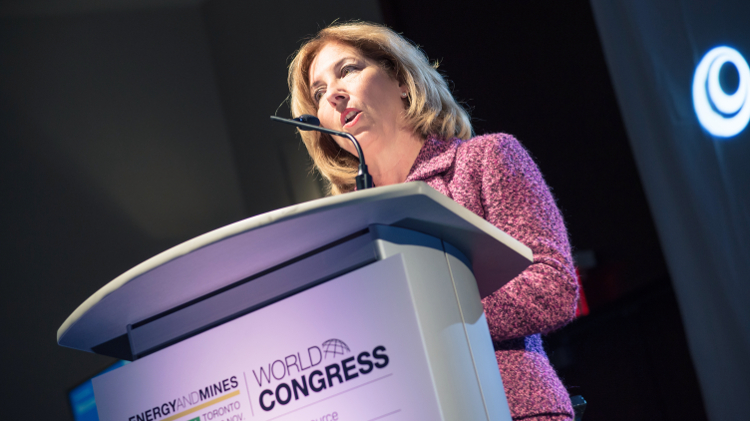
An alternative atmosphere
Renewable energy generates heat at the Energy and Mines World Congress