Outotec’s PSI particle size analyzers employ laser diffraction technology to measure ore after the grinding circuit. Courtesy of Outotec
When commodity prices were strong and rising, mining companies could afford minor inefficiencies in their plants. That is rarely the case in these days of lower-grade deposits, lower metal prices and economic pressure from every direction. “We have to do better with lower costs,” said Philip Thwaites, manager of process control for XPS Consulting & Testwork Services and a long-time champion for improved process control. “If we’re not efficient, we’re not going to be around. And our industry can be a lot more efficient.”
Part of the problem is that the mining industry has historically lagged behind other sectors, such as the oil industry, in implementing automation and measuring instrumentation – a big mistake. According to Thwaites, measurement is the cornerstone of control and efficiency. “If you have a poor measurement, or no measurement, you can’t do good control,” he explained.
But this is changing. More and more mining companies are conscious of improved measurements and endorsing control, automation and next-generation technologies.
What is more, there has been significant progress in automated instruments recently. These measure crucial parameters in the processing circuit and equipment to allow operators to monitor and adjust process control as needed. In particular, measurements relating to particle size in the grinding circuit, flotation variables and thickener bed mass have come a long way.
Particle size measurement in the grinding circuit
Historically, measuring particle size after grinding was done infrequently, if at all, because it required too many samples to be sent to a lab. Yet this measurement is key to plant efficiency and performance. Over-grinding wastes energy and under-grinding leads to particles that are not liberated or are too coarse, which in turn cuts the effectiveness of flotation and results in minerals lost to tailings. “Often the grinding capacity also turns out to be the production bottleneck,” said Jari Moilanen, director of Outotec’s automation product line, which specializes in process technology. “So if you can squeeze out more tonnes by grinding just enough, you’re not only saving energy and reducing chemical cost and use, which has environmental impact, but also increasing your capacity.”
It is no easy task to accomplish on its own, according to Moilanen. Because the ore body can have so many variations, operators need a measurement that responds immediately to changes in the feed for control purposes. The measurement technology needs to correspond accurately to the laboratory measurement and it must be robust enough to enable continuous grinding control and optimization.
In this, there has been progress. Today, it is possible to monitor particle size more reliably in real time at the plant. Outotec PSI particle size analyzers, for example, employ laser diffraction technology. The analyzer automatically takes samples from process streams every three minutes and sends a laser beam through them. When the light beam hits a particle, it diffracts slightly. Based on that diffraction, the particle size and distribution can be calculated immediately. Because it is a non-contact technology, the analyzer is not affected by dust and buildup. More importantly, constant measurements, fast sample analysis and automated adjustments allow for optimum grinding balance, said Moilanen.
In order to enable optimal mineral liberation in flotation, particle size needs to be measured in the grinding circuit product stream that is feeding flotation. Typically, the best sample point is the hydrocyclone overflow stream after secondary grinding. If there are several parallel grinding circuits, it is necessary to measure the end product of each grinding circuit. The PSI500i analyzer is available in 1-stream, 2-stream and 3-stream configurations.
Flotation-level measurement
“Flotation cells have been around for more than 100 years and, over that time, minimal automation has transpired that would enable the flotation process to run in a highly efficient manner,” said Robert Stirling, managing director of FloLevel Technologies.
Measuring flotation levels to achieve the highest possible high grade recovery is a daunting balancing act. The goal is to create just the right depth of froth at the top, which Thwaites compares to the froth in a glass of beer. “The bigger the froth column, the cleaner the froth will be, which means a higher grade of the concentrated minerals,” said Thwaites. “The smaller the froth column, the lower the grade, but the higher recovery. Every second, there’s new feed coming in. Sometimes the density is changing and sometimes the grade is changing, but the flow is always changing.”
The difficulty is that the variables that need to be monitored to achieve the optimal balance between recovery and grade are in constant flux due to the ever-changing ore head grade characteristics of slurry and conditions within the flotation cell. From the chemicals to the water and airflow used to control the velocity and density for optimal separation, froth management is dynamic. Manual tests typically used in mills can be inherently flawed, such as the one metallurgists use to determine suspended solids density which is taken every four hours or so. “They weigh the content on a scale next to the flotation cell to determine the solids ratio. They then go to the control room and make adjustments to water addition, et cetera,” said Stirling. “Meanwhile, the suspended solids concentration has changed again in the time it takes to walk to the control room.”
Since the flotation pulp level has proved difficult to measure directly, traditional mechanical measuring technology such as floating balls also have their problems; for example, solids can cover the balls, altering their buoyancy and accuracy.
“The challenge for industry is to get a decent, accurate measurement – every second,” said Thwaites. “We also need to know if [the flotation level] is in control and trending down or up.”
Real-time flotation-level monitoring, done on each bank of flotation cells, is clearly the solution, but using the proper measuring instrument has had its own challenges. Particle buildup on the measurement instruments and the issue of going inside the flotation cell to take measurements of the froth column are particular cases in point. One product that has addressed this is the XPSFloat that uses ultrasonic technology to produce highly accurate measurements of the flotation pulp level. The flat-bottomed, conical float in the device sits on the pulp/froth interface, allowing accurate calculations of the froth column. “It offsets the exact level of the pulp, which can’t be measured visually or directly,” said Thwaites. Because there is no contact, it has minimal moving parts and only a small, angular surface, minimizing buildups. A retrofitted XPSFloat typically costs about $6,000 per bank.
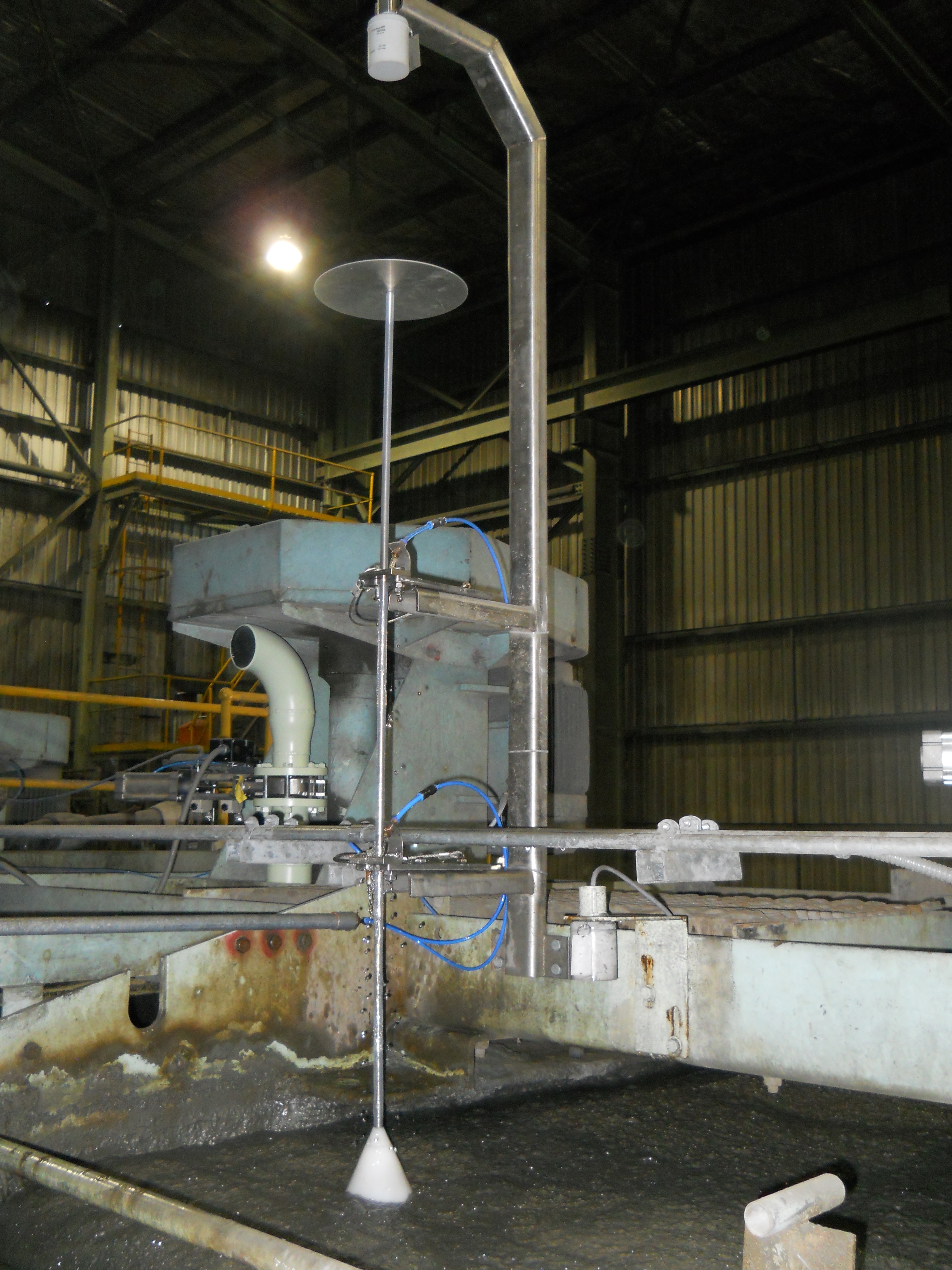 |
The XPSFloat uses ultrasonic technology to measure pulp level during flotation. Courtesy of XPS Consulting and Testwork Services
|
Another step forward has come from FloLevel Technologies. The company’s FloLevel system is self-cleaning, measures pulp and froth height and can measure process variables, froth density and suspended solids concentration in individual flotation cells. The technology uses transducers – devices that convert one form of energy to another – to emit sequential high-powered acoustic sound pulses into the flotation cell and receive them back. The different signals from froth and pulp allow the technology to track the interface between the two. Although immersed in the slurry and froth, the FloLevel transducers self-clean ultrasonically. According to Stirling, operators need one FloLevel system for every bank of cells and cost varies on the application and control range.
Outotec’s LevelSense measures slurry level and froth thickness using electrical impedance tomography technology, originally developed for medical imaging. The instrument consists of a probe with measurement electrodes attached to it that is immersed in the flotation cell and scans the different conductivities around it. It calculates where the slurry, froth and air meet and interact as well as the froth density and height. With no moving parts, LevelSense typically requires little to no maintenance. LevelSense instruments are normally used in each flotation cell.
Thickener levels
As with flotation, thickener optimization is all about balancing the equipment with the processing. From the feed’s flow rate, underflow (extraction), bed level and mass, to flocculent dosing and overflow clarity, there are many components and several measuring points. “The best way to optimize a thickener is to have the most information and measurements,” said Endress + Hauser Canada’s Rick Hemingway, whose company offers an integrated package that optimizes all the critical measuring points. Thickener bed levels are especially important; without good flocculent control and bed mass and height measurements, the thickener will not function properly. “If you put too much material in and fail to extract at an appropriate rate, you risk stopping the rakes and then having to shut down the plant and muck it out, which is a horrible, costly job,” said Thwaites.
Endress + Hauser’s Turbimax provides continuous measurement of the separation of liquids and sediment in the thickener beds using submersible ultrasonic level sensors. The time it takes for the ultrasonic signals generated by Turbimax to bounce back when they hit solid particles is used to calculate bed levels.Hawk Measurement Systems, which also has a range of integrated measurement and automation for thickener optimization, has developed the ORCA sonar system, which is attached to the top side of the thickener. “It’s able to penetrate down to the compacted bed level without interference of the lighter-density material,” said Steve Stone, Hawk Measurement’s vice-president of sales and marketing. The system also measures the lighter density material above the bed and the clarity of the water at the top level. That is because the ORCA sonar has the capability of emitting two different frequencies, one for measuring light density and the other for heavy-density interfaces.
Hawk Measurement Systems’ ORCA sonar system. Courtesy of Hawk Measurement SystemsClosing the loops with good measurements
Every milling plant has hundreds of potential measuring points that simply cannot be effectively monitored, measured and controlled manually, yet each one is critical to the overall efficiency. “You could easily be at 500 control loops in a big plant – so we are trying to do all these measurements continuously in order to do good control,” said Thwaites. “The operator’s job is then to set the optimum levels, or oversee the advanced controls and the equipment, but his job becomes much more complicated if the measurements and controls are not working properly or are not there at all. It’s all interconnected, interactive and it’s a multivariable control, but if you don’t measure the individual pieces, you won’t be able to run the circuit control and mill effectively.”