“If [innovation] made sense three years ago it makes more sense now,” said Dan Wicklum, chief executive of Canada’s Oil Sands Innovation Alliance (COSIA), as he ruminated on the slide in crude prices and profitability. Indeed, with few analysts predicting a healthy rebound any time soon, a powerful new form of energy is emerging in the oil sands: an accelerating drive to innovation and technology. Although the nature of bitumen extraction has always demanded innovation, the price plunge is bolstering efforts to new highs. At the RBC Capital Markets 2015 Global Energy and Power Executive Conference in New York in June, the industry’s leading players backed the momentum. “Our focus going forward will be on technology developments,” said Paul Masschelin, senior vice-president of finance and administration at Imperial Oil Ltd. “Going forward, we are going to need a lot of technological help,” added Doug Proll, executive vice-president at Canadian Natural Resources Ltd. The following month, Steve Williams, president and CEO of Suncor Energy, said at the company’s second-quarter results webcast, “We are looking at the next generation of technology.”
Considerable energy is pouring into the cause, whether it is to boost labour efficiency, cut water consumption or solve the enigma of mature fine tailings. Many innovations were already well under way before the recent price downturn, but the drastically reduced operating margins have put them under the microscope. “[The downturn] puts a stronger emphasis on the need to do [innovation],” said Michael Singleton, executive advisor at Kinetica, part of Innovate Calgary, the technology-transfer and business-incubation centre for the University of Calgary.
How to turn that motivation into results can be tricky, however. Singleton, an old Suncor oil sands hand who has been in the business since 1978, said that much innovation comes through continuous improvement rather than a eureka moment. “The industry has constantly been innovating,” he said, citing two watershed breakthroughs as examples: the conversion of oil sands mining from bucket wheel to truck and shovel – key to making oil sands mining economical – and steam-assisted gravity drainage (SAGD), which unlocked billions of barrels of resources deeper beneath the surface. “Each of these examples is composed of smaller technologies that enabled them. In the case of truck and shovel it was the technology around tires and the steels they were using for the trucks and shovels.” SAGD is very similar, he said. “It began with the AOSTRA (Alberta Oil Sands Technology and Research Authority) test facility where they sank a shaft and ran an adit out under the limestone and drilled that into the tar sand. So it was recognized you could soften the bitumen with steam and get it to flow out.” But the cost structure was not there yet. “Then along comes horizontal drilling,” he continued. “And it was horizontal drilling that enabled SAGD to become a cost-effective technique.”
Kinetica helps accelerate the process of achieving breakthroughs. “You don’t just turn a switch on and off,” Singleton explained. “The majors and the medium-sized companies have a suite of technologies they have been working on for decades in some cases.” They define efficiencies they want to achieve but often lack access to the technology solutions they need. Conversely, smaller innovative companies may have the solutions but not the connections to implement them. That in part is where Kinetica comes in; finding some of these missing links to feed into that innovation chain, said Singleton. “Innovations could come from a single inventor in a garage, a service company or a major corporation.”
Breakthroughs are often long-term developments, but Singleton said he has seen a trend over the past 12 months. “The emphasis is on energy efficiency, which also [addresses] carbon emissions.” One area he has seen gathering momentum is the movement away from using water in extraction facilities. “People are working on solvent extraction technologies, but again that’s not new,” he pointed out. “It has been looked at for 20 or 25 years. But with people making small advances day by day, we might be able to realize it.”
Indeed, Suncor’s Williams said in the second-quarter webcast, “We’re very encouraged with what we see in solvent technology. Hopefully, we will be able to move to essentially water-free extraction. That’s why we are working so hard on this new technology.”
Importantly, many new technologies need assistance for market acceptance. Kinetica tries to make sure the innovators are ready. The technology has to work, to be fundamentally sound. “We find that with a lot of the smaller companies they don’t have a good management structure or experience,” said Singleton. “They don’t have the normal requisites like financial strength or good governance. So we move them through various stage gates of selection, making sure that when they get to market with their technology that they are going to succeed.” Kinetica already has two or three small innovations ready for field trials, according to Singleton. Citing confidentiality considerations, he declined to release details but did say that “right now there are 12 or 13 technologies moving through our stage gate process.”
Petroleum Technology Alliance Canada (PTAC), has also observed the downturn influencing the pace and direction of new innovation. “It has certainly put significant focus on reducing costs,” said Soheil Asgarpour, PTAC’s president. “Innovation plays a major role in being competitive with countries like Saudi Arabia and [those in] the Middle East. So the industry is putting more focus on cutting costs and finding technologies that would enable sustainable development while reducing the environmental footprint and negative social consequences, but at the same time increasing production efficiency and profitability.”
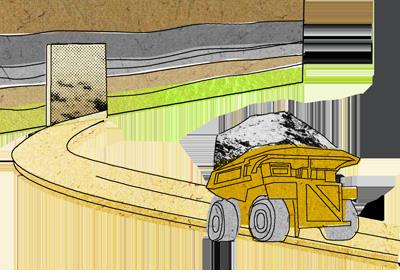
To that end, PTAC has its Phoenix Network, a group of six oil sands companies focusing on cost reduction following the advent of low commodity prices. Originally known as the Oil Sands Leadership Initiative (OSLI), Phoenix is concerned with developing technologies related to non-environmental areas of SAGD. “It’s about reducing cost, increasing production rates, increasing reserves,” Asgarpour explained.
Phoenix holds several workshops each year for articulating challenges and finding technologies for SAGD development and production. “At the workshops we clearly define what the challenges are and then conduct a search to find technology solutions,” said Asgarpour. “These searches could be done at an international level to see if any other organization or industry has technology that can help us.” A potential solution is initially identified and then a consortium is formed from the members of the Phoenix Network. The consortium takes solutions all the way from concept to commercialization including field tests and financing.
PTAC provides funding for up to 15 per cent with no expectation of intellectual property (IP) ownership. “That puts us in a unique position to be a neutral broker to negotiate the IP ownership between the funder and the research provider,” said Asgarpour. Funding is from PTAC’s own sources, government grants or other sources such as the Natural Sciences and Engineering Research Council of Canada.
Making the connection
There have recently been a slew of innovation-focused events in Calgary designed to connect small companies with the money they need.
This year’s Innovation in Technologies Awards at Calgary’s Global Petroleum Show in June showcased some of the new innovations coming to market. One of the nominees, QS Energy Inc., specializes in a new viscosity-reduction technology. Harnessing the principles of electrorheology – the application of a high-strength, high-intensity electrical field to change the mechanical behavior of fluids – the system decreases the viscosity of crude oil by causing particulate matter to clump together. Hundreds of samples, ranging from bitumen to superlight condensates, have been lab tested. The company projected that a decrease of 20 per cent to 25 per cent in viscosity would lead to a gross benefit to the operator of $560,000 to $700,000 per month, or $6.7 million to $8.4 million annually.
The most recent testing has been on dilbit, or diluted bitumen, which is typically the form oil sands products take as they flow through pipelines to market, said Gregg Bigger, chairman and CEO of QS Energy.
In a major new innovation gathering just before the Global Petroleum Show, COSIA held its first Innovation Summit in Banff, Alberta. Delegates – many international – attended sessions on COSIA’s four environmental priority areas (EPAs): land, water, tailings and greenhouse gases (GHG). One presentation at the summit featured an innovation by InLine Dewatering Ltd. Its principle is that dewatering total oil sands extraction tailings as they travel via pipeline from extraction to deposition – while retaining all the fines and sand – will allow for a reduced environmental footprint and would immediately recycle hot water back to the extraction process. The dewatered tailings would eliminate future fluid fine tailings formation and allow for early reclamation of these deposits – both a cost and an environmental advantage.
One more recent and early-stage innovation, also driven by cost and environmental advantages, is Steam Environmentally Generated Drainage (SEGD), the brainchild of Bernard Chung, president and owner of Valence Energy and a long-time oil sands expert. His SEGD solution involves three horizontal wells and recently received Canadian patent approval. Produced water injected into an upper well is drained downward to a second well, where it is vaporized by the combustion gases of an in-situ gas burner. The steam and gases flow outward, heating and mobilizing the bitumen. Bitumen and water (primarily steam condensate) are collected in the lower production well; produced water is reinjected, and combustion carbon dioxide (CO2) is automatically sequestered. The concept is being proved using numerical reservoir simulation and laboratory physical modelling this year and into 2016, Chung said. Design and shop testing of the downhole burner are scheduled for completion in 2017, and field piloting to demonstrate commercial viability is expected between 2018 and 2020. Chung is currently seeking industry interest and participants for funding these latter phases. “SEGD can be retrofitted into existing SAGD and heavy oil projects as new SEGD wells and well pads,” he explained.
Chung said he reckons savings from using SEGD over SAGD include reduction in initial capital costs of about $10,000 per bpd of oil due to significant reductions in plant and steam pipeline costs for water treatment, steam generation and pipelining. In other words, 1,000 bpd of oil production would save $10 million in upfront capital costs. And comparable or lower operating costs are realized due to decreased energy needs, no CO2 emissions tax, less water treatment, no surface steam generation and lower facility maintenance costs.
The search for oil sands innovation is increasing worldwide. In July 2014 GE launched its GHG ecomagination Innovation Challenge: Energy Efficiency Solutions for Canada’s Oil Sands. Awards were offered in two categories: Higher Value Uses of Low Grade Heat and Improved Efficiency of Steam Generation. It is an indicator of the worldwide nature of oil sands innovation that in addition to entrants from Canada and the United States, among the eight winners were innovators from India, the Netherlands, the United Kingdom, France, and Italy. Awards totalled C$1 million in development grants and cash prizes.
COSIA too is proactively identifying and tapping international sources for good ideas. For example, last fall, COSIA sent a team into Israel and scoured its innovation systems – private and public sectors, small and large organizations – and triaged its innovation capacity, said Wicklum. “They had a series of scoping meetings with a whole suite of innovation organizations,” he noted. It is an example of what COSIA calls “innovation hubs,” which enlist associate members, already numbering almost 40. “It is a way we can really extend the reach of our oil sands companies very effectively and efficiently around the world,” he said.
The drive for new innovative ideas has boomed in the past year, but there are still many barriers. Even when proven and funded, adopting new innovations can be fraught with risk. “You are making a targeted assessment as to what benefit you’ll get out of it,” said Allan Fogwill, president and CEO of the Canadian Energy Research Institute. “Any time you make a change to a process there is a risk of something going wrong. You don’t want to get in a position where you have an efficiency improvement – say 10 per cent reduction in energy use or 10 per cent increase in recovery rate – when putting that change in place could have you not producing for weeks or months.” And it is more critical with today’s thin margins; there is less room to recover.
Fogwill said he thinks success often relates to company management experience: “If management has a history of implementing new projects well, then the risk of something going wrong is lower.”
What is on the horizon for oil sands innovations? “Companies don’t make investments in this industry with just a three- or five-year vision,” said Singleton. “It is 10, 15, 20.” He said he reckons the present downturn will be longer than past ones, adding, “So we don’t just batten down the hatches for a short period. It is changing the way we do business.”