Miniature minersThe rise of microbes in the mining industry
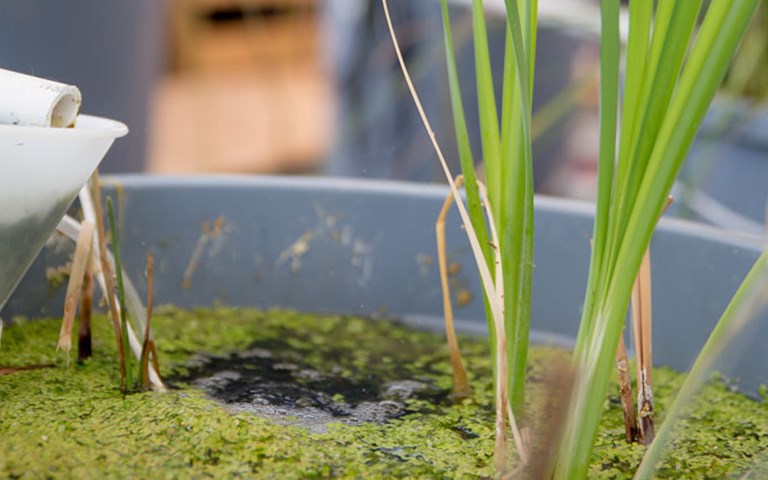
The mining industry largely concerns itself with the inanimate resources of nature: rocks, metals and chemicals. However, there is an increasing interest in how living organisms – small, singlecelled microbes – can breathe life into the mining cycle and limit its environmental impacts.
Monique Haakensen sees a lot of microbes in her role as president and principal scientist at Contango Strategies. Using DNA-sequencing technology, the company provides a microbial community profiling service which identifies the microbiological population at mining projects and provides lab results, guidance on remediation strategies or even suggestions on which living plants will add to an ecosystem to help microbes thrive. And according to Haakensen, microbes are finally getting the respect they deserve for their role in remediation.
“Until this type of technology came about, it was a guesstimate, and because of that there have historically been a lot of failures in passive water treatment because they were not based on informed decisions,” said Haakensen. By using tools now available, Haakensen said she can understand how the environmental system at a project works, what is influencing the system and develop a more robust remediation project.
Remediation is just one of several applications of biotechnology, which rely on microbiology and microbes found in the environment to help extract metal from ore bodies or neutralize contaminants from waste material. Microbes can also be deployed in hydrometallurgical applications to aid in the leaching process.
In recent years, the potential environmental and financial benefits of biotechnology and the increasing precision with which it can be applied have made it attractive to mining companies looking for new approaches to engineering problems. The field is set up to grow, with new efforts to understand which microbes can be the most effective partners for a specific mining operation at their basic, genetic level.
Small microbes, big rewards
Bioleaching and biooxidation are two common biohydrometallurgy techniques, explained Corale Brierley, consultant and vice-president of the U.S.-based National Academy of Engineering. Both are microbe-based metal production processes that use a water-based solution. By adding specific microbes to a traditional heap leaching system, bioleaching can extract base metals like copper, nickel and zinc. Biooxidation is a similar process, typically applied to refractory gold ore prior to cyanide leaching. The main difference is that in bioleaching, the targeted metals are brought into solution whereas in biooxidation they remain in a solid state.
The microbes used in bioleaching catalyze the chemical leaching redox reaction, helping electrons move between types of iron during a chemical reaction from which they obtain the energy they need to grow. The movement of these electrons transforms sulphide minerals into sulphur, sulphate or both, releasing the metals from the surrounding deposit into a solution and restarting the oxidation process. This process produces higher recovery rates that would otherwise be difficult to achieve for low-grade ore in sulphide-based deposits.
Bioleaching already produces between 18 to 20 per cent of the world’s mined copper, Brierley estimated, and about 26 copper heap bioleaching plants have been built since the 1980s. BHP Billiton used the technique at its Cerro Colorado mine in Chile in 1993, and Teck, Freeport-McMoRan, Anglo American and Vale all have experience with the process.
Biohydrometallurgy has clear environmental advantages over conventional mineral processing, according to Bangor University professor Barrie Johnson, especially when it comes to preventing the release of arsenic into the atmosphere during smelting. Treating the ore with biological techniques sidesteps that risk because it avoids high temperatures which could volatilize arsenic and turn it into a gas. Instead, the ore can be treated at temperatures between 20 to 50 degrees Celsius. “You don’t have to worry about separating or blending concentrates with high arsenic contents, and the danger of putting arsenic gases into the atmosphere is eliminated,” explained Johnson. “It ends up in the liquid and is then immobilized as an inert solid. The environmental impact is contained.”
Biohydrometallurgy is also more energy-efficient than a traditional smelter. “Smelting usually involves very high temperatures and therefore high energy requirements and carbon emissions,” Johnson said.
One final environmental benefit comes from the microbes themselves. The organisms used in this process need carbon dioxide to survive, so they consume rather than produce the greenhouse gas.
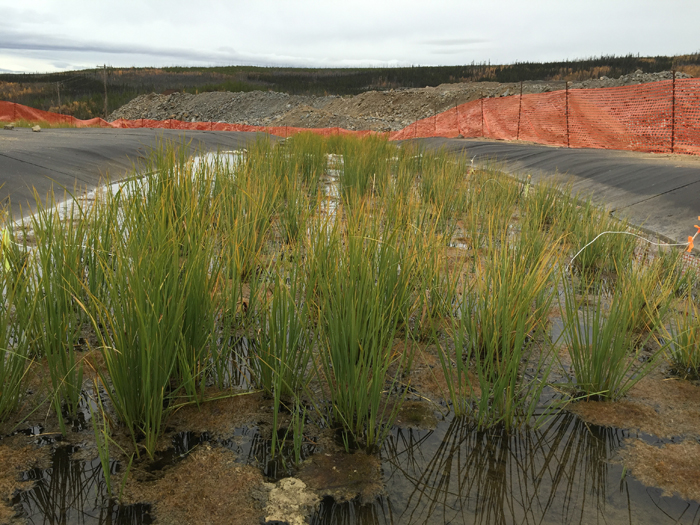
The economic equation
Mineral extraction using biological processes, or biomining, came of age in the mid-1990s when mining companies were looking for a way to cut copper production costs. Prices and grades were falling, “sort of similar to what’s happening today,” Brierley noted. Most of the easily accessible and weathered deposits had been discovered and exploited, leaving mining companies with large but less-weathered (and more difficult-to-exploit) supergene deposits.
Making the most of these deposits was a tall order in a tough economic climate, Brierley said, especially when factoring in the cost of crushing, grinding, floating and smelting the metals. “The cost of doing all these processes was more than the ore was worth,” she said. “So bioleaching was a no-brainer.” Combining heap leaching with some useful microbes was a financially viable option to bring recovery rates up without raising capital costs.
Unlike smelters and flotation circuits, the microbes did not need to be brought in to remote areas or squeezed onto a small site. “These particular micro-organisms appear all over the world,” Brierley said. “What you have to do is create the kind of conditions that the organisms will thrive in, and they’ll multiply and divide quickly and they’ll break down the ore as rapidly as possible.”
There are a variety of microbes that can do the trick, according to Johnson, who also leads the Bangor Acidophile Research Team. All of the microbes used in bioleaching and biooxidation are known as acidophiles, because they can survive in low-pH conditions required for the chemical reactions that separate valuable metals from waste.
Though every microbe used in biomining shares this characteristic, each has its own particular function and each has its preferred environment, Johnson noted. “They occupy different niches, in many cases. Some will work at high temperatures, up to about 80 degrees [Celsius]. Others will work down to about 10 or even five degrees or so,” he noted.
While biomining can be considered for any operation extracting ore from a sulphide-based deposit, Brierley noted, there are a few situations in which it is a better choice. The amount of space that can be allotted for a biologically-based heap leaching pad might not be feasible in mountainous areas, for example, because there are technical limits to the height of heap leaching pads. Biomining is also considered more suitable for remote operations. “When accessibility is an issue, it is difficult to transport autoclaves and smelter components to the site,” said Brierley. A sophisticated workforce is also not necessary for bioleaching, but decent water quality at the site is, she added.
Comprehensive closure
In Yukon, Haakensen and Contango Strategies are helping Capstone Mining Corp. develop wetlands as part of its long-term bioremediation strategy at Minto mine to take out copper, selenium and cadmium from its wastewater. (The mine has a traditional wastewater treatment plant for its on-site water treatment needs during the operational period.) “Closure is where we really see the benefits of using bioremediation,” said Ryan Herbert, Minto’s environment manager.
Reduced operating costs is one such benefit, Herbert said. “You don’t really require the same sort of manpower to operate the wetlands that you would need to operate a treatment plant. There is still some monitoring and maintenance required, but it’s definitely not a 24-hour manned treatment system,” Herbert said.
Capstone is also exploring site-specific bioremediation research at Minto, partnering with Contango. Parts of that research include examining the impact a cold climate and a freeze-thaw cycle could have on the plants in the wetlands and on contaminant re-release. Herbert noted preliminary results from an on-site test area should be collected this summer.
Today, the potential productivity of microbes is attracting more attention, particularly in remediation and water treatment systems. Laurentian University announced in May it would dedicate $630,000 to fund a research chair in biomining and bioremediation. The chair will work with Vale, Glencore and other partners in industry.
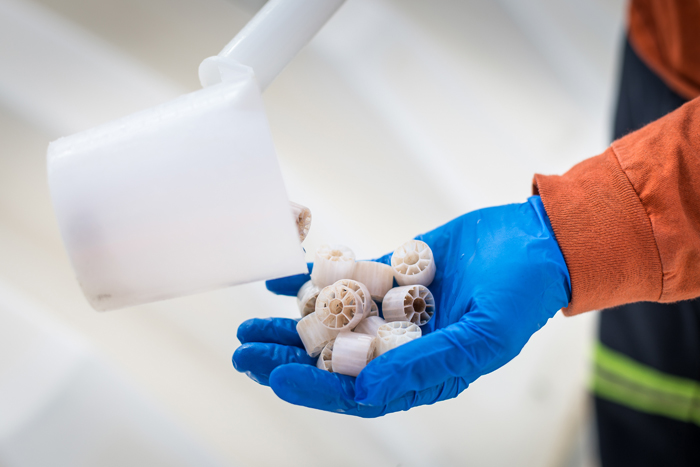
Case studies
Microbes have done a lot for engineers at Agnico Eagle’s LaRonde gold mine in Quebec. The mine stopped releasing the final effluent into the environment in 2000 when the company identified high levels of thiocyanate (SCN). It needed to treat the effluent, so it put the water into tailings ponds while turning to a biologically-based remediation technique, using microbes to break down these toxic compounds into other harmless chemicals.
“For us, this technology was the safe choice,” said water treatment coordinator Patrick Laporte. “We have many elements creating toxicity [at LaRonde],” he said, including SCN, cyanate (CNO), nitrite (NO2) and ammonia (NH3). “Biological treatments are the only ones that could treat all of them. Other technologies could pass one or two toxicity tests with our waste water, but not all of them.”
LaRonde set up a plant with two stages in 2004, one with bacteria of the Thiobacillus genus to hydrolyze CNO and SCN, and another with Nitrosomonas and Nitrobacter bacteria to handle NO2 and NH3. Technicians at the company refined the process through trial and error over three years until going full-scale in 2008.
“We needed to learn more about the bacteria,” Laporte said. “We needed to find the bacteria’s limit and optimize the conditions in the plant.”
Trial and error helps get new techniques like biotechnology into the field and the market, Brierley said, partially because connecting people in the lab and in the field is not always a sure thing. “At a lot of the technical meetings that we have, there’s not a real good mix of the people who work in research and do discoveries and those that can take those discoveries and apply them or the engineering that is required to make them work,” she said.
That dynamic is evident in the field as well, noted scientist and bioleaching expert Marja Riekkola-Vanhanen. “These are processes where you need all kinds of people: metallurgists, biohydrometallurgists, biologists, geologists and so on,” said Riekkola-Vanhanen, who most recently worked on a Finnish nickel bioleaching project.
Commercializing the chemistry
For companies that do not want to design their biomining system in-house, as Agnico Eagle did, there are commercial options that can be customized to the site. South African-based BIOMIN produces BIOX, the system used at most current commercial biooxidation operations. The process works on the sulphides in the minerals, oxidizing them and exposing the gold before it undergoes cyanide leaching. Bacteria catalyze the reaction, regenerating the ferric acid that is needed to break down the pyrite by attaching to the surface of the mineral and creating a microenvironment, said BIOMIN’s managing director Jan van Niekerk.
There are also some newer entrants to the biology-based technology field, including Canadian-based EnviraMet, which presented a paper on bioremediation at the CIM 2016 Convention in May. (The company has developed technology to target a number of common contaminants, including selenium.) “EnviraMet’s approach recovers elemental selenium from bioreactor sludge, allowing the waste to be applied to land as non-hazardous fertilizer,” said Altair Ioffe, president of Ioffe Biotechnologies and a biotechnology consultant for EnviraMet.
Bringing the science into the field can be very difficult, and getting it right can take time. While Brierley has worked extensively on new projects, her current focus is on biotech plants that are already running but may need a bit of help, she said. “It’s almost universal. You try to design them as best you can, but problems still happen.”
LaRonde’s treatment plant was no exception. A biofilm had to form in the reactor to allow the microbes to operate, but the film was so heavy in the first stage that it broke the equipment, which was already weakened by the microbes. Changing the system from a rotating, cylindrical biodisc to a moving-bed biological reactor solved that problem, which in turn created more ammonia than the second-stage plant could handle. (Their solution was to use a stripping pond. That pond has since been emptied.)
Tough to reach, tough to leach
Biotechnology has continued to evolve, but so too have the challenges. As supergene deposits are exploited, some are already looking deeper to hypogene deposits in difficult-to-leach chalcopyrite and enargite. “Eighty per cent of the world’s copper going forward is in these types of ores,” Brierley said. “The problem with these types of ores is not only that it is hard to leach them but they are very low grade and very deep, in some cases.”
New techniques and applications for biomining may help companies as they think about tackling these and other deposits as well as other types of ores. Talvivaara Mining Company’s open-pit nickel mine in northeastern Finland began using microbe-based heap leaching operations in 2008 – which Riekkola-Vanhanen helped develop – and started shipping nickel concentrate in 2009.
At Talvivaara, the ore is crushed and stacked on the leach pad, then irrigated with acidic water over 13 to 14 months, allowing the bacteria to act and catalyze the chemical reactions.
With biomining in place, the operation has seen an 85 per cent recovery rate for nickel, as well as 80 per cent for zinc even though the mineral composition of the deposit includes chalcopyrite. Riekkola-Vanhanen cited the low capital and operating costs as the reasons the technique was chosen.
“This is a special ore that was on the bottom of the sea about two billion years ago,” said Riekkola-Vanhanen, and the deposit has high levels of graphite. “For that reason, it is possible to make a concentrate, but that concentrate contains 1.5 per cent nickel. No one will buy such a concentrate.
“If you try to float an ore that contains so much graphite, the graphite will float in the flotation process,” she said, making bioleaching the most economical option for treating the ore. Many processes are performed – first taking out nickel and cobalt, then copper and zinc.
“Bioleaching works well, but it’s only part of the whole process,” she said. “For example, you have water insoluble metal sulphides, and then after bioleaching you have water soluble sulphates in solution, so you must have effective hydrometallurgical (or chemical) processes to produce metals from the solution.”
In-situ mining is one kind of technique that may be used to go after deep deposits, Brierley said, possibly with a biological boost. “In-situ mining is going to be an absolutely huge step because there’s going to have to be a great deal of not only engineering but science as well, because we’re not close to that yet,” she said.
Some of that engineering and science is being funded by the European Union through the BioMOre project, Johnson noted. The project is currently in the pilot stage, but focuses on both deep in-situ mining and “bacteria-assisted” deep in-situ mining.
While deep in-situ mining has been done before at Canadian uranium mines, those deposits have a basement rock that copper deposits lack, Brierley said. That basement rock is crucial to ensuring the solution used to leach the ore does not spread to unintended areas.
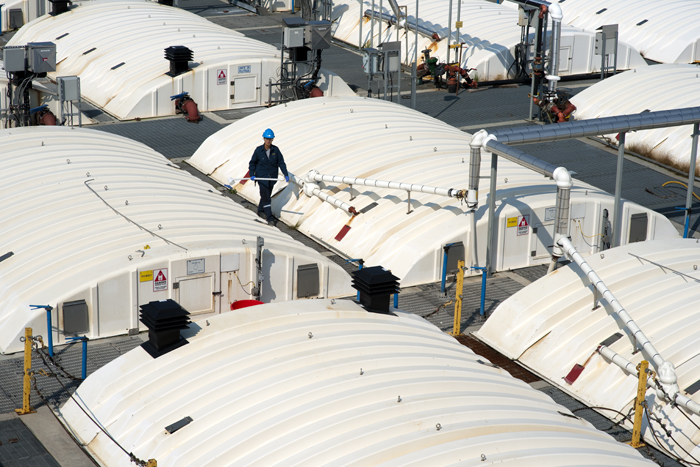
Genetic engineering
As microbes continue to prove themselves, the technology and research needed to optimize their use are finding more support. Haakensen highlighted the federal funds being made available through Genome Canada. Genomics studies the genetic makeup of species and organisms, and many projects are hoping to use new knowledge about the genetic makeup of plants and microbes to customize the organisms used in specific environments such as reactor cells or in remediation projects to tackle specific contaminants. A Genome Canada funding competition for genomics projects with mining applications is ongoing. One project seeking funding aims to sequence the genomes of 800 trees to find species that are well-suited to rehabilitating mine sites. Another is specifically looking at the genomes of bacteria in mining wastewater.
“I think the number of people getting interested in [this type of technology and process] is growing,” noted Haakensen. “There’s always been interest in it, but there weren’t a lot of tools. We are now seeing the number of tools increasing and the amount of academic research in the area has been increasing.”
With the variety of new developments coming up, and the impact biotechnology has had, it is clear that microbes may be minuscule, but they have the power to pack a big punch for mineral processing and remediation projects alike.
More Technology
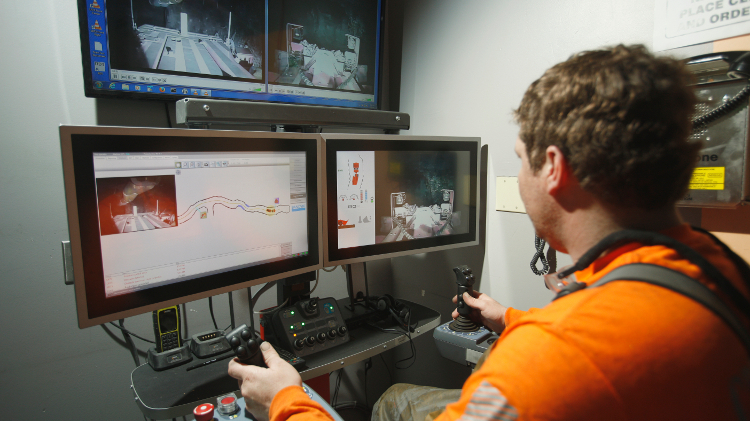
The automation revolution
There is no doubt the future of mining is automation. But what does that look like, and how will we get there?
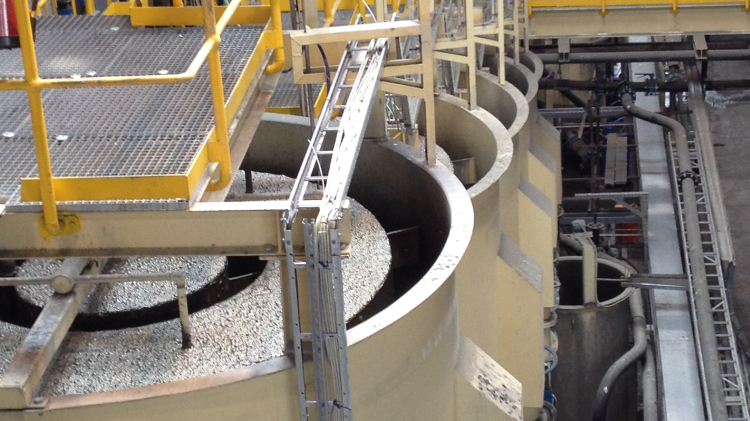
The future of flotation
Buoyed by pressure to cut costs and improve recovery, new flotation technologies are on the rise