Sensors such as this were deployed at McEwen Mining’s El Gallo operation in the heap leach to monitor irrigation, as well as on a crusher to pinpoint the cause of downtime. Courtesy of McEwen Mining
Last year, McEwen Mining learned something from a small experiment at its El Gallo gold mine in Mexico. Moisture monitors buried in the heap leach betrayed a dearth of cyanide solution on the side of the heap, which meant recoverable gold was being left behind. The company also made another valuable discovery: it is possible to monitor conditions from thousands of miles away, using buried sensors and a WiFi connection.
The individuals working on bringing the industrial Internet of Things into the mining space see no limit to the spaces and devices that could conceivably be instrumented. Once transmission becomes truly wireless, sensors can be fitted to anything: a person, a vehicle, a tool. The information they provide offers numerous ways to optimize mining operations.
Scanimetrics
“People have talked about this for twenty years, but it’s only in the last couple years that it’s actually been practical to do this,” said Steven Slupsky, President and CEO of Scanimetrics, the electronics company that McEwen engaged to help monitor its heap leach.
Slupsky pointed to three critical advances in technology: low-power electronics that can run off a battery, low-power wireless protocols for duty cycling a transmitting device and analytical software that interprets vast quantities of data. At the same time, certain sensors, including accelerometers, have improved in quality and dropped in price. Much of this work took place to meet a consumer-driven demand for smartphones and reliable server farms.
Scanimetrics originally developed its completely wireless condition monitoring solution for the oil and gas industry. Sensor pods run off a battery, lasting up to a year on one charge, and transmit to a repeater, data capture unit, or Internet gateway 10 metres away. That information is sent to the Scanimetrics office in Edmonton to be analyzed and made available as simple visualizations in a web browser.
Following an initial collaboration on crusher condition monitoring, McEwen and Scanimetrics worked together on the El Gallo heap leach project. A full-scale trial is now underway. “We’re going to a pristine area of the leach pad,” said Nathan Stubina, managing director of McEwen Mining. “We’re putting two cells side by side. We’re trying to put the same amount of ore and the same type of ore on both sides, and one we’re going to monitor the way we do now, and the other is by installing a moisture detector and a compaction detector to learn more. We’re going to see whether we’re going to get an improvement in gold recovery by monitoring it.”
The sensors had already been ruggedized for underground pipeline monitoring. In the heap leach, they are laid out in a cable-connected grid across the bottom of the heap, about 10 to 20 metres apart. A tube running from the cable to open air gets the signal out where it can be picked up by a data capture unit.
Watch : The internet of things and predictive analytics at the mine site
While the moisture sensors pick up on how well the cyanide leach is distributed, compaction sensors can tell Scanimetrics whether the heap is stable. Slupsky sees this as a source of insight for future design criteria and a potential help to miners’ struggle for social licence.
“The same technology can be used in tailings dams,” he pointed out. “A tailings dam breach was being reported in the media, and I thought, ‘Aren’t we measuring the same things that are important to understanding whether one of these things is going to suffer a stability issue?’”
Smart Rockbolt
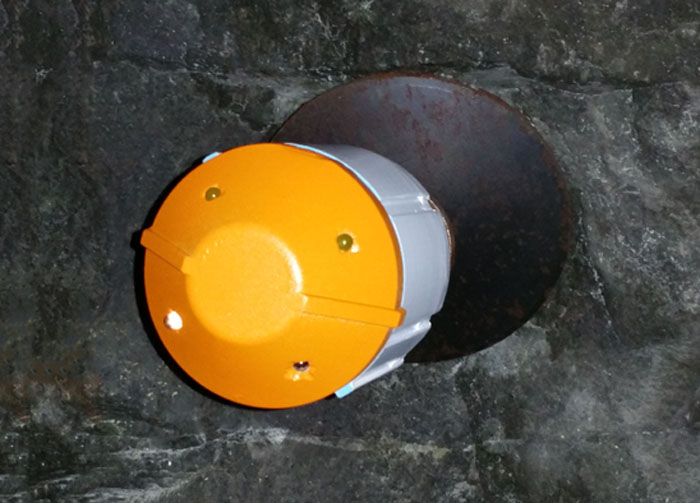
The Smart Rockbolt mounted on a standard rockbolt head. Courtesy of ThingWave
More than a decade ago, a manager at the Swedish iron ore company LKAB wished for technology that would tell him how rockbolts were holding up. A research team led by Jens Eliasson, associate professor at Luleå University of Technology, is almost prepared to grant that wish.
The Smart Rockbolt consists of a normal rockbolt fitted with a strain sensor, an accelerometer and electronics to record and transmit data. Light-emitting diodes on the head can be programmed to signal the rockbolt’s status, warn miners of dangerous ground conditions, or provide illumination in an emergency.
“When we detect deviations, something that the rockbolt feels is strange, that will generate an alarm,” said Eliasson. “The data that we detect is then made available to existing software to be analyzed by the mining experts in seismicity or rock mechanics, for example.”
Instrumented bolts provide information impossible to obtain by other means: Is the bolt intact? And is it holding an acceptable load? These questions point directly to any potential failures, and they came up every time Eliasson spoke to a mining company about Smart Rockbolt.
A network of instrumented bolts – at a density of about one to two per cent of the total rockbolt count – would also add supplementary data points to existing monitoring systems. For example, mine planners could see a complete picture of a tunnel’s deformation and judge its safety accordingly. Instrumenting rockbolts would also be a comparatively cheap way of getting local seismic information that the mine’s geophone network could not provide.
The instrumentation on the rockbolt is designed to fit into the mine’s existing communications and data processing setup. A likely usage would see the bolt running on a battery and transmitting via low-power radio. The sensors would run continuously, but the bolt would sleep until its onboard processor detected an anomaly. Then it would wake up and start transmitting to the nearest network gateway within seconds. Each bolt would be identified by its own IP address on the network.
Data is always stored on the rockbolt so that breaks in connectivity will not disrupt recordkeeping. “When you add a new gateway, it will resynchronize and upload everything to our cloud system,” said Eliasson. From the cloud, mine management could access, process and visualize the data any way it chose.
A couple of planned test installations in Boliden mines will indicate what changes need to be made for usability in a working mine environment. Within a year, Eliasson said he expects to have something that could be deployed on a large scale and that could be installed manually or mechanically. The product will be sold by spin-off company ThingWave AB, of which Eliasson is CEO.
Vandrico Solutions
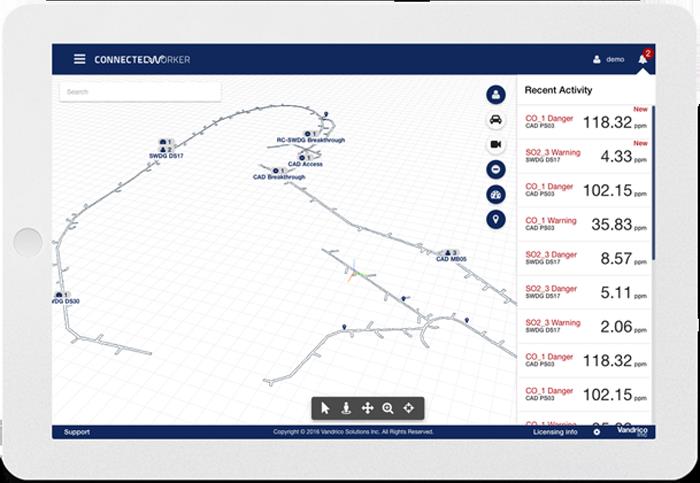
The tablet display for the Connected Worker by Vandrico Solutions. Courtesy of Vandrico Solutions
The sheer number and diversity of data-capture solutions can give headaches to mine management attempting to integrate everything – and that is in spite of the software and services designed to make data user-friendly. That is where Paola Telfer, co-founder and chief commercial officer of Vandrico Solutions, sees her company stepping in.
“What we’re bringing into the equation is this open communications platform, which is kind of a novel thing in the mining industry,” she said. “We’re not looking to reinvent the wheel, but we’re bringing together the best-in-class systems that mining companies have already chosen in a way that is consolidated and is a single pane to look at for the people who are making decisions in real time.”
Out in the field, that could mean that a mine worker puts on a wearable device at the start of his or her shift.
That device would be a single point of contact with all the condition monitoring systems in the mine; if ground control deemed an area unsafe, for example, a smartwatch could vibrate or blink an unmistakable warning to the person working there. The watch would also be the miner’s means of communication to the central office, by way of an IP camera or instant messaging.
The wearable device itself could contain sensors. One existing product has an embedded sensor that detects dangerous gases. If a drill operator drills into a pocket of gas, the device could prompt that operator to leave instantly.
At the level of operations management, Vandrico offers a three-dimensional visualization of the mine and its operations, based on relevant data from numerous monitoring systems. Telfer said that while plenty of third-party suppliers would like their interface to be the conduit for other services, Vandrico is unusual for designing with a strong emphasis on user experience and a philosophy of absolute openness.
“From the perspective of an actual mining company like a Rio Tinto, these (closed) systems are data islands,” said Telfer. “So whether the interfaces are for the operation supervisors on their computers or on these massive dashboards that they have on the wall at the operation centre, they have to keep switching plugs, they have to keep switching logins, and they can’t see everything at once, because these legacy providers are quite siloed from each other. This could lead to dangerous situations and a decline in efficiency and productivity.”
By contrast, Vandrico’s Connected Worker Software Suite uses an open-standard API built on the same architectural principle as the Internet, with the intention that it can share information as easily as it pulls information from other systems. Telfer also emphasizes that the user experience can be fully customized by and to the mine’s needs without the need to involve Vandrico.
With the sheer number of monitoring providers out there, some of whom have invested heavily in their own closed systems, it may not be possible to integrate everything just yet. But as more people, places and things come online, streamlining all these data sources will likely become as high a priority as acquiring them in the first place.
Vandrico has explored a number of different devices and is actively seeking hardware partners to develop more, but so far the pilot projects tend to start with smartwatches.