In May, Hecla Mining Company announced it had introduced Sandvik's AutoMine Lite system to tele-remotely operate load-haul-dump (LHD) loaders at its Greens Creek mine in Alaska. Courtesy of Hecla Mining Company
Three years ago, Hecla Mining Company, a 126-year-old Idaho-based precious metals mining company, began looking into automation technology for its four mines: Lucky Friday in northern Idaho, Casa Berardi in Quebec, San Sebastian in Mexico, and Greens Creek mine on an island off the coast of Alaska. “We’re not a huge company,” said Mark Board, the company’s vice-president of technical services. “So rather than simply diving in and saying we want to automate everything in the mine, we looked at all of our operations and asked ourselves where our bottlenecks were, what made sense economically for a company our size and the type of mining we do.”
Without the deep pockets of mining giants such as Rio Tinto or Anglo American that have championed, developed and implemented automation, Hecla was forced to be very strategic, thoroughly analyze its operations and identify where automation would bring the greatest benefit and return on investment. It also looked externally at technologies being successfully employed by other mining companies.
Board and his team travelled to Europe, where they spoke with vendors and visited other mines that had implemented various automation technologies to solve similar issues they faced, including Boliden’s mines in Sweden and Dundee Precious Metal’s Chelopech mine in Bulgaria.
Back at home, they developed a unique and customized staged approach for each mine and budgeted for the gradual implementation of automated tools. “We have been working on implementing things we thought made sense for Hecla on a step-by-step basis,” said Board. Earlier this year at Greens Creek, the company introduced Sandvik’s AutoMine Lite system to tele-remotely operate load-haul-dump (LHD) loaders. It made sense for the mine because Greens Creek staff have a 45-minute commute by ferry to get to work for their shifts. “It’s a long day and there’s a lot of lost time between shifts,” said Board. “Mainly, we use the autonomous LHD loaders to muck the headings at shift changes so we can clear a heading out and speed up the process to get the people back in and start putting in ground support and drilling the heading.”
At Casa Berardi, they introduced Atlas Copco semi-automated drill jumbos, including computer-controlled rig guidance of drill patterns and drilling control as well as a Sandvik automated longhole production drill, automated hoisting and tele-remote rockbreakers controlled from the hoist room. In the fourth quarter of this year, the company will have autonomous trucks moving ore and waste from the main mining zones to the shaft.
And at Lucky Friday, the company is testing automated haul truck driver assist technology. It is also working on a longer-term step in its strategy with Atlas Copco to develop a mechanical mobile miner for vein mining. Initially, the machine will be tested using on-board personnel, but it will be equipped for tele-remote control with automated muck haulage should Hecla decide to go that route in the future.
Hecla is just one of many mining companies that has put its money on an automated future. And while automation may be the newest tool for mine operators to extract minerals and metals as safely and efficiently as possible, it will only be useful if those who implement it do so with two hands firmly on the wheel. Innovation presents risks – technological over-reach, network security, and social impacts, for example – and the key is to anticipate and mitigate as many of these as possible.
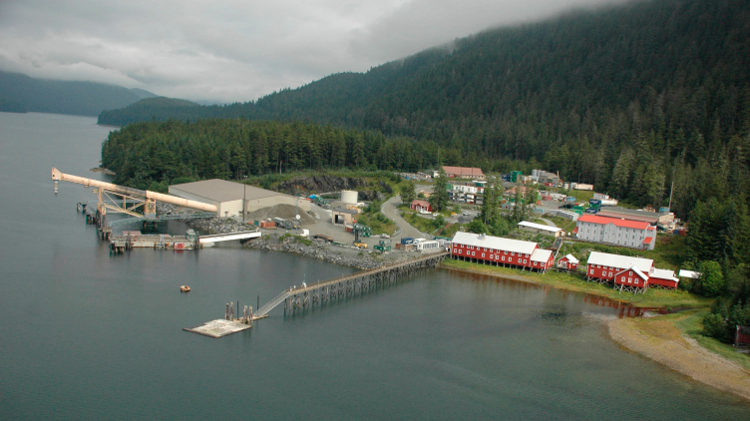
Hecla is developing a customized approach to automation for its four mines: Lucky Friday in northern Idaho, Casa Berardi in Quebec, San Sebastian in Mexico, and Greens Creek (above) on an island off the coast of Alaska. Courtesy of Hecla Mining Company
A staged approach
There may not be a tried and true blueprint for companies that want to start automating their operations, but Hecla’s step-by-step approach is in fact the implementation strategy experts recommend mining companies take.
“When we start talking about automation in the mining industry, right away people think about a fully autonomous fleet of machinery,” said François Gariépy, director of technology solutions for Peck Tech Consulting. “Instead of going for fully automated machines, there are many things companies can automate that will provide more value per dollar than making the fleet fully autonomous.”
But you cannot start blindly automating, even if it is little by little. According to Drew Larsen, mining business development director for Autonomous Solutions Inc. (ASI), companies need a long-term strategy in order to be successful. “What is it they want to see happen in their operation?” he said. “How can they get the most value through the technology? What would that future state look like? They may have to take that vision and break it up into smaller pieces. But each one of those pieces needs to be structured such that they can scale or gradually keep building toward that vision.”
Related: Peck Tech's François Gariépy on the road to automation
A successful strategy also requires building a strong business case for automation initiatives, according to Larsen. “At the end of the day, it’s really about bringing the whole organization to get buy-in from the operations and line up the needed capital to make this successful,” he said.
Al Poole, chief electrical designer at Stantec concurred. “Getting the project and operations teams aligned with the automation philosophy is critical. Unfortunately, sometimes project teams want to implement a new automation system, yet the operations group isn’t interested in using it. This can lead to cost overruns and schedule delays to get the teams aligned on how to best operate the facility,” he said.
Change management is also critical, said Larsen. “It includes things like a review of their internal procedures and processes. Technology provides the ability to replicate something and have a high degree of repeatability, but to really leverage that, they have to pair it with the operational rigour in their own processes in order to maximize that technology,” he said. “The old adage ‘garbage in, garbage out’ applies. If you’re going to automate a junky process, it’s just going to be an automated junky process.”
One eye on the problem
A big deal has been made about the potential for machines to take jobs away from humans, and rightly so. In theory, the number of workers who could be displaced across sectors is staggering. A study by McKinsey & Company and the Brookfield Institute concluded about 40 per cent of tasks currently done by humans could end up being automated. However, the original driver for automation in mining was never to eliminate human operators, according to Gariépy. Rather, it was to solve a specific problem. “In Western Australia, they were short on labour so for them, full automation was the solution. In other cases, mines were dealing with dangerous terrain. They had to be able to operate their machines without sending people into the pit. In that case, a remote-controlled solution was just as suitable as an autonomous vehicle, and could be less expensive. What we’ve found is the mines that automated and increased productivity and realized the most savings were the ones that deployed an autonomous solution to solve a specific problem.”
A successful automation implementation strategy, said Gariépy, leverages the best of artificial intelligence and the best of human intelligence. “In anything that’s complex that requires some thought process, people are the cheapest and most efficient solution for addressing the problem. If it’s just computation or accuracy, there’s probably no one who can beat a machine at that. So let’s use people for what they are good at. Where machines can do better, well, this is where it is worth investing in the autonomous technology.”
GMSG Future Mining Forum Edmonton: Bringing global mining automation and innovation priorities into the regional context
There is no cookie-cutter automation answer for all mines, he said. The optimal and most cost-effective solution with the highest return on investment will differ from mine to mine and could include various levels of semi-autonomous and autonomous solutions.
Artificial intelligence is excellent at repetition. Human beings are brilliant at problem solving, dealing with the unexpected and complex thinking. The key is to develop solutions that leverage the best of both. “Hauling is quite a repetitive task and most people are looking at that area,” he said. “Digging in and of itself, picking up material, is repetitive but choosing what you are picking up requires some thought process. For shovels, you probably don’t want to remove the operator, you just want to add auto-dig and auto-dump. That would prevent shovel operators from boom-jacking or hitting the trucks every now and then, for example. So, with that level of automation, you’d be more efficient, reduce wear on your equipment and could make operators more proficient with much less training.”
Risky business
Cybersecurity is already a concern for mining companies, and it has been for several years. As more operations automate, this risk only increases. “[Automation] means there are more machines and all those machines are connected online,” said Daniel Tobok, CEO of Toronto-based cybersecurity firm Cytelligence. “Anything that is online can be hacked.”
Given the world we live in, it does not take much imagination to think of the catastrophic possibilities of an autonomous machine being hacked and the havoc it could cause in a mine. “Mining companies tend to rely on IT for this, but they are not the people to look after security because it isn’t an IT problem,” said Tobok. “It’s an operational problem. A million fire walls and intrusion detection systems and fancy stuff works to a point, but the best way to address it is to be proactive and build cybersecurity from the ground up that has proper security and protocols in place.”
Related: Rob Labbé of Teck Resources believes collaboration is key to fighting cyberattacks in mining
Another potential risk of replacing human operators with robots has to do with safety and equipment damage or loss. “Humans are just brilliant at detecting things that are not normal, whether it’s a strange smell or a black smoke,” said Jonathan Moore, ASI’s chief engineer.
And despite advances in sensor technology, it still cannot replicate human senses. “When you remove the operator, you lose all that [human] forewarning and diagnostic [for the equipment],” said Moore.
The human brain is also finely tuned to react to the unexpected and make quick judgment calls. “You hope an unforeseen emergency situation never happens, but when it does, you know you’ll do the right thing.” If, for example, a human is driving a car and the breaks fail, they will react quickly by honking to warn others, steering and trying alternative ways to stop the car. “For robots, we don’t even attempt to train those scenarios,” said Moore. That is because robots are limited by the situations their programmers can anticipate, and equipment failure is not always predictable.
Moore points out that the airline industry has very high levels of automation and high levels of reliability. “The failure rate in airlines is very low. But there is a cost to that in the development and analysis,” said Moore, who said he believes this issue will need to be addressed by the mining industry with new, higher standards for failure rates.
Shared value
Last February, imagining the massive revenue loss in income taxes that a reduction in jobs performed by humans would represent for governments, Microsoft co-founder Bill Gates suggested they should tax companies that replace human workers with a robot. But the implications of large-scale automation displacing countless workers are more far-reaching than government revenues.
“A lot of mining companies think they are going to be hiring fewer people when they automate,” said Jeff Geipel, venture leader for Mining Shared Value – a venture of Engineers Without Borders Canada – and one of the authors of a recent research study led by the International Institute for Sustainable Development on the influence of technology on local employment and procurement. “But they may be overlooking the fact they could end up buying fewer things, such as uniforms and camp services, and that loss in local procurement is going to add up to a significant amount that will impact the host economy.”
This is important because a company’s pitch to local communities to operate a mine in their backyard often includes some form of local employment and procurement in order to foster a mutually beneficial relationship, a concept known as “shared value.” If machines perform many of the jobs, both local employment and procurement go down while local governments receive less money from income taxes from local residents. This could in turn make it harder for companies to convince jurisdictions to let them operate within their borders.
Rather than doom and gloom, Geipel said he believes mining companies and governments need to begin planning for these impacts and develop new structures and relationships that build on the concept of shared value.
Related: Operators and tech suppliers are mapping multiple paths to the autonomous mine
Whether or not automation will result in dramatic job losses remains to be seen. And, in fact, there is no certainty automation will even solve the labour shortages predicted for the mining industry. For example, the Mining Industry Human Resources Council (MiHR) has found that while automation will certainly reduce the need for certain types of workers, the industry’s hiring needs have been shifting toward more university-level training and away from those with high school or no diploma, certificate or degree.
“It can be challenging to predict a monumental shift in technology such as automation, especially with very few previous historical observations to point to,” said Ryan Montpellier, executive director at MiHR. “It is also difficult to predict the impact automation will have on the composition of the workforce, the new skills that will be needed from future generations and the adoption rate from mining companies, communities and workers.”
On the edge of this monumental shift, many mining companies, according to Stantec’s Poole, are interested in automation but not moving toward it. “In some cases mines don’t want to be first,” he said. “Instead, they prefer to be fast-followers.”
The fast-followers, however, are already implementing their automation strategies. Hecla is one of them. “For companies our size, adopting even incremental automation and innovation strategies has a significant bottom line impact. And other mining companies that have already begun this process have been amazingly generous toward us with information,” said Board. “There’s a certain camaraderie among mining people and a willingness to share information with others, and that’s helped our application go in a relatively straight forward way. Hecla is the same. We don’t see it as a competitive advantage. We too will share all the information we have with other companies.”