Rio Tinto’s growing fleet of fully autonomous haulers in the Pilbara iron ore district of Australia is now just one example in the spectrum of options for operators looking to automate. Courtesy of Rio Tinto
Industry observers would be hard-pressed to ignore Rio Tinto’s success with the Mine of the Future project in Australia’s Pilbara iron belt. With 71 driverless haulers moving ore, Rio Tinto reported it cut operating costs there by 13 per cent and upped utilization rates 14 per cent in 2015.
This is a winning proposition, but in a difficult economy, not all companies can afford to outfit their operations with brand-new autonomous haulers, nor are the sites necessarily well-suited to accommodate fully-autonomous vehicles. Nevertheless, some have made the leap, electing to retrofit their equipment to allow for driverless operation, while others are taking a more measured approach, phasing in autonomous features to assist operators or take them away from the working face.
Some of the interest may have been driven by the economic downturn, but Joshua Marshall, a Queen’s University professor and consultant whose research focuses on automation and field robotics, said there are other forces at work.
“There is a desire on the part of this up-and-coming generation of workers and managers to use technology to improve mining activities, whether it be to increase productivity, improve safety, or simply make things more efficient and convenient,” he said.
The argument for autonomy
There are several reasons why autonomous vehicles have caught the industry’s attention. “Autonomous vehicles in general have a higher utilization of availability rate,” meaning the machines can skip breaks and run through shift changes, said Drew Larsen, the director of business development for mining at Autonomous Solutions Inc. (ASI).
Automated vehicles may also avoid human errors that can decrease the lifespan of a vehicle, and could be particularly useful in an area that is a risk to a human operator’s safety – in a worst-case event like a pit slope failure, only the vehicle may be lost.
Several major equipment manufacturers, including Komatsu, Sandvik and Caterpillar, now offer autonomous vehicles to companies.
Marshall noted that some original equipment manufacturers (OEMs) are willing to retrofit their equipment to operate autonomously or remotely, but OEMs are not the only companies getting in the business of making autonomous haulage accessible. Third-party companies have developed OEM-agnostic methods to automate mixed-brand haulage fleets, which means operations that want to go autonomous could do so without making a major capital expenditure to replace a fleet before its time.
How it works
Trucks driven by software need the same thing a human driver needs – information about the surrounding environment.
Autonomous haulers rely on sensors to send information to a computer unit. Software processes that information and signals the machine about how to act. GPS and inertial sensors must be able to cope with the potentially challenging environmental conditions of a mine site and are supplemented with specialized radar systems and cameras to monitor the surroundings and stay on course.
In some cases, the software cannot control the machine directly; the machine must have a drive-by-wire system installed, allowing a computer to control the hauler through electrical or mechanical signals.
Most machines built in the last eight to 10 years have built-in electronic controls – basically, drive-by-wire capability – but many older models do not. The make and model of the machine itself determines exactly what needs to be done during a retrofit. “It really runs a whole gamut from a fairly electronic interface to lots of mechanical interfaces,” Larsen said.
Those interfaces present the biggest challenges for a retrofitter, said Mehran Motamed, CEO of Rigid Robotics. “Think about it. In a sense, you’re trying to build a human (surrogate) to control the truck, which is not efficient,” Motamed said. Rigid Robotics will be at MINExpo, showing off their DriveAssist autonomous solution, which can be rolled out in stages beginning with assisted braking and cruise control for haul truck drivers to comprehensive vehicle autonomy.
ASI began a partnership with Anglo American to retrofit several vehicles in 2014. Both Anglo American and ASI declined to share specific data about the impact of ASI’s work, but Anglo spokesperson James Wyatt-Tilby confirmed that the company had seen a “a very significant productivity uplift and major safety improvements where we have been testing it in our operations.” The company has tested the technology at open-cut coal sites.
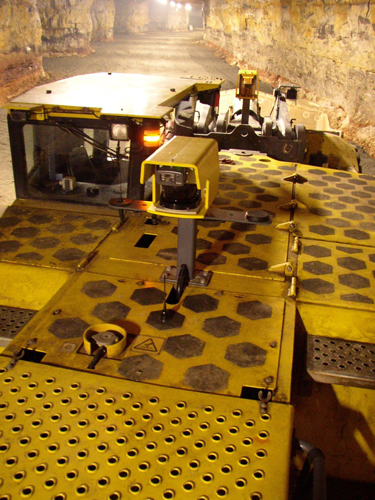 |
Underground operations pose a particular challenge to automated haulage because of the frequently changing underground environment. Courtesy of Joshua Marshall
|
Building a work-around
Autonomous operation has been OEM driven up to this point with each of them developing the software and user interface. Underlying each piece of software is a set of application program interfaces (APIs).
For third party technology, that has complicated the task of integrating a drive-by-wire system.
For now, retrofitters have found a way around not having access to the APIs, installing equipment with their own software and allowing machines from several brands to work together well. For example, ASI’s command and control system, Mobius, will work with any make or model. “It is that agnostic piece,” Larsen said, which can translate to more flexibility for mine operators.
Retrofitting haulers to operate without a driver in the cab does not necessarily have to take a lot of time. Ryan Siggelkow, senior vice-president of Hard-Line, which specializes in remote control and automation for open-pit and underground equipment, estimated that they could retrofit a hauler, end-to-end, in about two weeks.
“If you go into other machines, say a drill or one of the more complicated ones, we could be looking at upwards of a few weeks,” he noted. The company can also retrofit any type of machine, make or model for tele-operation.
The best layout for an autonomous hauler is an environment that is stable. “Ideally, for automation to be the most successful, a machine has to do something repetitive for a long period of time. That’s the basics of automation,” said Siggelkow. An underground mine site with a drift that is changing every day is not the ideal place for an autonomous hauler.
“A lot of sites we talked to, they love the technology, they want to try it, but they’re not set up for it,” Siggelkow added.
While not fully autonomous, tele-operation and driver assist systems still fall on the automation spectrum. “A mine which has a plan to go to full automation could actually start with some technologies that would benefit a manned fleet, and then can progress towards an autonomous fleet,” Larsen said. That is the strategy for Rigid Robotics, said Motamed because the human aspects of the shift to autonomous operation are every bit as challenging and important as the technical ones.
Obstacles ahead?
Third-party retrofitters still face several challenges. For example, there are some efforts to try to bring APIs into the light, either through publication or standardization. “I don’t know that the vehicle manufacturers will ever all agree on a common standard set of APIs, but the industry is certainly pushing for that,” Larsen said. “And we would certainly welcome it.”
Related: Interoperability has the potential to spark innovation in mining unlike ever before
As with any software, cybersecurity could be a concern. Publishing an API could also expose security vulnerabilities in the software. Car companies have already seen the need to ensure applications around cars are well-secured; in February, Nissan had to disable an application for their electric car, the Leaf, after a security issue allowed hackers to turn on and off the fans, download information about trips and drain the battery remotely.
“With proper software development provisions, you can minimize security risks,” Motamed said. “Additionally, autonomous systems by definition have to be very safe. If they fail, they have to fail in a safe mode.”
Finally, Marshall noted, automating an existing fleet will likely not make economic sense. “I would argue that retrofitting may not be advisable for some types of equipment and some types of automation. Retrofitting for teleoperation may work well, but retrofitting to automate a heterogeneous fleet of LHD machines may require a lot of customization work that, in the end, may not work as well as a fleet designed and ‘ready’ for automation,” he said. Caterpillar spokesperson Mark Sprouls agreed, noting that a fleet that is older than ten years and would require conversion to electronic controls may not be an economical option.
Larsen acknowledged that complexity does drive costs for retrofitting. “For each vehicle type, there is some specific and unique characterization and development that has to be done,” he explained. “The more standardized a fleet is, the simpler and less costly it can be [to retrofit].”
Ultimately, each company and each operation must evaluate if an autonomous haulage solution is right. “Everyone wants to increase the efficiency of their operation,” Siggelkow said. “If we can be more efficient and get more productivity, there’s not a site that wouldn’t need that.”