How do we fill the skills gap?Creative solutions to mining's skills shortage
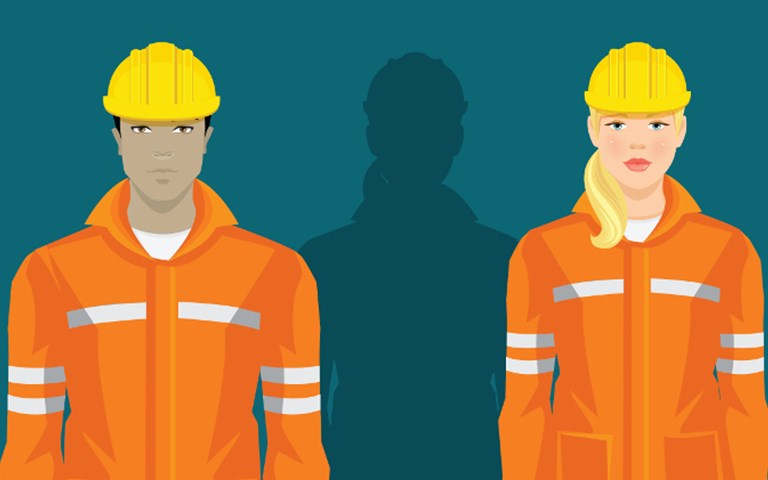
Canada’s aging population is sapping its future workforce. Last year the Conference Board of Canada reported that every new job created in a Canadian organization in 2016 had to account for the loss of 1.8 retirees.
Mining is no exception. Its looming skills shortage is exacerbated by a pernicious cocktail of factors more specific to the industry. These include the remoteness of many operations, the sector’s economic volatility and its sluggish embrace of diversity.
Mining Industry Human Resources Council (MiHR) executive director Ryan Montpellier said that when combined, these factors have the potential to be “a recipe for disaster.” MiHR predicts that over the next 10 years, 88,000 new workers will be needed to make up for 50,000 retirement exits, alongside other shortages. And that is just MiHR’s baseline estimate, based on current industry trends and forecasts – in an expansionary economic scenario, the figure reaches 130,000.
Despite these bleak figures, Montpellier is confident the industry will address its human resources challenge. And overall industry sentiment is positive. Across Canada, national, international and provincial collaborations have been born out of a collective need to sophisticate, streamline and standardize training approaches, all while harnessing the power of new technology. Experimental career development programs are being rolled out at mine sites like Agnico Eagle’s Meadowbank mine in Nunavut and New Gold’s New Afton mine in British Columbia. At other mines, third-party training programs have been implemented to attract underrepresented demographics and develop the local workforce.
![]() |
Opening the door to new workers
Women and immigrants are two huge segments of the population that have traditionally been shut out of mining and remain critically underrepresented. And while the mining industry is the largest private sector employer of Indigenous people, MiHR’s 2014 10-year outlook report revealed that the talent group remains underused and in general limited to entry-level, support and front-line production roles. Moreover, promoting Indigenous careers in mining is sensible, given that they are the fastest growing segment of the Canadian population, bucking the national trend, in which seniors outpace youth.
A key part of MiHR’s mandate is to work with industry to identify and entice all sources of labour to mining. One of its programs is the Mining Essentials initiative, which is run in partnership with the Assembly of First Nations and focuses on pre-employment skills for Indigenous communities. It is a win-win scenario, according to Montpellier: Indigenous people are provided with the “foundation skills, the pre-employment skills, the attitude and industry knowledge to enter the industry,” and mines benefit from a skilled local workforce. The self-sustaining program, funded by each individual industry partner and “various pots of Indigenous training funding,” is likely to have a long future, said Montpellier.
The Mining Essentials program is always 12 weeks long and includes 12 to 18 participants, but every delivery is “unique and adapted to the needs of the community and the local employer,” said Montpellier. Four deliveries at Goldcorp’s
Musselwhite mine between 2015 and 2017 gave participants the opportunity to gain work experience at a site on a fly-in, fly-out, two-weeks-on, two-weeks-off basis. On the other hand, the experience for Métis and non-Indigenous students at the École secondaire catholique Thériault in Timmins in 2017 was more theoretical, providing students with 240 hours of in-class “curriculum-based training” on top of 120 hours of “experiential learning opportunities.”
Women are the most critically underrepresented segment of the Canadian population in the mining industry, making up only 17 per cent of mining’s labour force despite making up over 48 per cent of Canada’s overall labour force. MiHR’s Gender Equity in Mining program works with mining companies to identify the systemic barriers, such as policies and procedures, to joining the mining industry that women face. Issues identified by the first cohort of participants include not having a woman on a panel for an interview and gender-specific language in job advertisements.
As part of its work on diversity and inclusion, MiHR provides mining labour market information and resources to immigrant service agencies across Canada. New immigrants make up 21 per cent of the Canadian workforce, but only 14 per cent of the mining workforce.
MiHR is not alone in this endeavour; Derrick Schmuhl has been facilitating new Canadians’ entry into the industry for decades as the manager for training programs at the Edmonton Mennonite Centre for Newcomers (EMCN). Schmuhl said the EMCN’s programs have “become more and more relevant as the years have gone on,” given the rising number of immigrants. Despite being able to provide companies with a “wealth of experience, methods and skills,” many immigrant engineers arrive in Canada ill-equipped to enter the job market because their qualification is not recognized, they are not familiar with Canadian workplace culture or they do not know how to find or compete for positions, explained Schmuhl.
In the past, the motto of the mining industry was you had to move out to move up. We want to break that mould. We want to retain our employees and move them up internally. – P. Prochotsky
That was the impetus behind EMCN’s 11-month Engineers’ and Technologists’ Integration Program (ETIP), which has placed many people in mining companies over the 28 years it has been running, and “at least five in the last two years,” said Schmuhl. It is supported by Alberta Human Services and the Association of Science and Engineering Technology Professionals of Alberta.
Schmuhl said ETIP “helps engineers be engineers again,” by providing them with cultural, workplace and business communication skills, alongside a Canadian-issued qualification from the Northern Alberta Institution of Technology (NAIT) and a three-month supported job search.
Schmuhl said that, based on what he has seen, work experience is crucial to facilitating immigrants’ entry into industry. He is currently looking to set up more formal partnerships with mines to be able to officially incorporate work experience into ETIP.
While he admitted that setting up work experience programs at companies can be a logistical challenge and involve negotiation, the front-end work pays off. “Once they’ve done one, [companies] will do multiple,” he said.
Schmuhl is not alone in his advocacy for a hands-on experiential approach to training. Jill Tsolinas, executive director of the B.C. Centre of Training Excellence in Mining (CTEM), a group that works as a virtual hub for collaborative, innovative training opportunities, said that this “blended learning theory” is crucial to keeping training approaches effective. The issue is particularly pertinent in British Columbia, which has an older mining workforce than the rest of Canada.
CTEM also strongly advocates for local training for local jobs. “I call it the green-way approach to building a workforce,” Tsolinas said. “If you don’t train up your local workforce, you are going to have to import your expertise.” She added that training local helps mitigate mining’s diversity problem: “Every community has different demographics. Some are high in Indigenous individuals, others in skilled immigrants. If you are not being proportional to where your community is, then you are restraining your workforce.”
![]() |
The Meadowbank model: Inuit involvement
Hiring a local workforce in Canada’s remote northern mines involves hiring and training Indigenous people who may be unfamiliar with heavy industry and corporate culture, policy and procedure. It is crucial, however, given that it saves on the high cost of outsourcing employees from far-off cities – employees who are more likely to defect to mining operations closer to their families.
Gabriel-Antoine Côté, training coordinator for the Meadowbank gold mine in Nunavut, said hiring local goes beyond financial motivations. It is an issue of “respecting our commitment of developing the local workforce as we are mining on their land,” he said.
When Meadowbank opened in 2010, it was the only operational mine in the Kivalliq region of Nunavut. The local Inuit communities had not had exposure to the mining industry for more than 50 years, let alone entertained the idea of working at one. Experienced employees were flown in from other provinces to kick-start operations.
Today, 62 per cent of equipment operators at Meadowbank are Inuit, as is 34 per cent of the overall mine workforce. While this is still shy of the 50 per cent target stipulated in an agreement between Agnico Eagle and the local Inuit association, Côté said the number is “slowly, steadily rising, and sustainable.” That is thanks in part to the many other stipulations in the mine’s Impact and Benefits Agreement. For example, the mine has not hired a non-Inuit heavy equipment operator since 2012 as a result of its internal career path system, which ensures internal promotion.
In 2012, the company implemented several ladder-like “career path” programs to develop the local workforce. Possible career paths include mine operations, road maintenance, process plant operations, drill and blast, and field services, and each is carefully mapped out. When an employee masters one rung, they can start operating in their new skillset position, as well as act as relief operators and be eligible to apply for the next level of training.
The career path system was a “huge milestone,” said Côté, because it democratized hiring and training. Employees progress through their desired path based on their competency – a move that gave the Inuit workforce a fair chance toward upward mobility opportunities.
Côté attributes the mine’s success to a flexible attitude in which the particular needs of the local community are carefully listened to and accommodated where possible.
For instance, initially there was a problem of no-shows on site during caribou and seal hunting season. “Hunting is their life. It’s part of their culture and we have to understand and respect that,” said Côté. Because animal migration dates are unpredictable, Inuit staff could not request the days they wanted off far in advance – as stipulated by company policy. To cater to this, management loosened policies around the notice period employees could give to get time off. “We keep [the notice period] a deliberate grey zone to show we will be more flexible,” said Côté.
The average salary at Meadowbank is $107,000, and Inuit employees initially struggled to manage their newfound earnings. To remedy this, Agnico Eagle ensured that financial literacy was incorporated into the pre-employment five-day “work-readiness program” all new employees must take. This “work-readiness” is delivered off site with the help of community partners and includes numeracy, problem-solving and literacy skills, alongside information about employers’ unspoken expectations.
Those who complete the work-readiness program then complete a five- to seven-day site orientation. They see all the different trainee schemes available and spend time shadowing employees working in their desired career path, while also getting a feel for sleeping in a camp, eating in a cafeteria and working 12-hour shifts. This ensures that workers know what they are getting into, said Côté, saving the company from abrupt resignations later.
Agnico Eagle’s commitment does not come cheap. According to Agnico Eagle, the company annually invests about $5 million on training current employees, and $280 million on local business procurement. But Côté said the approach spearheaded at Meadowbank is a “matter of stability,” adding that the hope is that Nunavut operations will eventually be “100 per cent Inuit – and that includes the mine manager.”
![]() |
The New Afton approach: hire local and train up
In Canada’s more populated regions, mining has to face off with other industries for talent. Developing the local workforce involves being adaptive to the demands of employees and providing them with career prospects beyond a mine’s finite life. This sometimes involves overhauling outdated ideas about what miners value.
New Gold implemented a hire-local program at its New Afton mine in Kamloops in 2008. The mine “wanted to have people who were engaged with the local community and wanted to stay here and would be long-term employees,” said mine superintendent Peter Prochotsky. The mine benefitted from its proximity to the populated community of Kamloops, and a bank of workers with transferrable skills from working in farming and logging.
Each employee at New Afton has their own development plan and a supervisor with whom they come up with a quarterly training schedule. Employees are rotated through different positions to ensure they are “continually growing throughout the year,” said Prochotsky.
“In the past, the motto of the mining industry was you had to move out to move up. We want to break that mould. We want to retain our employees and move them up internally,” he said. The benefits of this approach are proven by New Afton’s turnover rate of less than five per cent per year and its enviable mine safety record. The operation has won four consecutive John T. Ryan Awards for having the lowest injury frequency rate for metal mines in B.C. and Yukon, five Safest Large Underground Mine Awards for B.C., four provincial Mine Rescue Competitions, and one National Western Regional Mine Rescue Competition Award.
Echoing Meadowbank’s Côté, Prochotsky said New Afton’s success is in part due to being attentive to the shifting demands of the mining workforce. “We found that people entering the mining industry now value a work-life balance over total cash compensation,” he said. In 2008, employees voted in a seven-day on-off rotation (and a less generous pay-package) instead of a longer 14-7 on-off rotation. It has remained in place ever since.
Prochotsky has been working with CTEM on a project to compile tried and true training approaches in the province into a training guide for new operations. Tsolinas said this type of collaboration and the “virtual hub” that CTEM provides is key, as mining suffers from the lack of a physical location where training efforts can be focused and can thrive.
![]() |
Reaching out to improve within
Economic downturns and upswings result in widely fluctuating demand for labour. Partnerships across Canada and beyond between industry, government and higher education are ensuring that lingering shortages from periods of inactivity can be quickly remedied, all the while ensuring that in the future, no such gaps will exist.
The power of collaboration is also being harnessed in Yukon at the Centre for Northern Innovation in Mining (CNIM). Before the centre opened in 2013, Yukon’s three operating mines were paying nearly “eight million a year between them to fly people in and out of the territory,” according to Shelagh Rowles, the centre’s executive director. The province’s available mining workforce had been sucker-punched by 10 years of inactivity from the late-1990s to the early-2000s. Now, the mining school runs multiple programs that combine classroom, simulator and on-the-job training for local talent. It also has a mobile lab that can be taken to local communities.
The CNIM’s governing council, which provides direction on training and helps administer funding, includes senior officials and general managers of the three operating mines in Yukon, First Nations government and provincial government officials, and CNIM faculty. Also central to the work of the advisory council is agreeing to a common standard for Yukon miners. “That’s to say, if we have an underground miner, what is that? What are the components of it? What are you looking for?” said Rowles. Standardization secures future job prospects for miners and safety for employers.
I truly believe in the future people are going to look back and say, 'Remember those days when we did training without simulators?' – A. Charbonneau
Council meetings are also a forum for discussing the industry’s needs. Recently, industry members aired concerns about safety standards for mine driller helpers – an increasingly sought-after role, given growing exploration activity. CNIM hired a trainer with the certification to offer Ontario’s standardized Common Core driller training. Two training sessions have been delivered in the past year, and nine students have graduated.
“When you have government, industry and post-secondary together, it’s kind of a magical combination where work can happen,” said Rowles.
The school also has an arrangement with the University of Alaska, whereby CNIM underground mining students spend two 14-day shifts at the American university’s state-of-the-art mine training facility, 800 kilometres northwest of Whitehorse.
CNIM’s collaborative ambitions do not end there; discussions are underway with the University of the Arctic in Norway, too. “We’re trying to be as nimble as we can, and also have a real focus on building the northern workforce and having a lot of these circumpolar connections, be that with Alaska, Finland, or Sweden. There’s some really good, important conversations happening,” Rowles said.
A couple of years ago, CNIM was also doing a “lot of back and forth and sharing information” with Newfoundland and Labrador as they were setting up training programs.
Part of CNIM’s work with industry is keeping an ear to the ground with regard to new technological innovations, and how they will impact the skillsets required for future Yukon miners. “That’s a huge pressure right now,” said Rowles, adding that “the more we communicate, the more we project, the more we gather information, the better our response will be. Obviously, there will always be tricky waters, but hopefully we’ll have a solid canoe.”
*****
Technology and training
Automation and technology are key considerations for future workforce planning. Montpellier said they will have a “significant impact” on the number of employees and the skillsets needed, although he acknowledged that their impact on the labour market is not yet apparent. For example, a shift to driverless haul trucks – as Suncor is preparing to do in Alberta – will mean that there will be less demand for heavy equipment operators and instead a need for people who can “design, program, monitor, optimize and maintain the fleet of vehicles,” he said.
While technological advances present challenges to workforce training, they also have the potential to positively transform it. Equipment simulators have already shaken up the industry by allowing inexperienced employees to be trained in a controlled and safe environment without interfering with actual operations.
At Rio Tinto’s Diavik mine, a 10-foot tall Epiroc (previously Atlas Copco) truck simulator incorporates an exact replica of the mine site – from ramps and fuel bays to rules, policies and procedures. At New Afton, a simulator trained 120 inexperienced workers over two years before the mine had even opened. (It has now been transported to New Gold’s newer Rainy River operation.)
Al Charbonneau, Epiroc’s project manager tester, said he believes simulators are likely to become more “versatile” and will play an increasingly large role in mine training, given their safety benefits. “I truly believe that in the future, people are going to look back and say, ‘Remember those days when we did training without simulators?’”
More Management
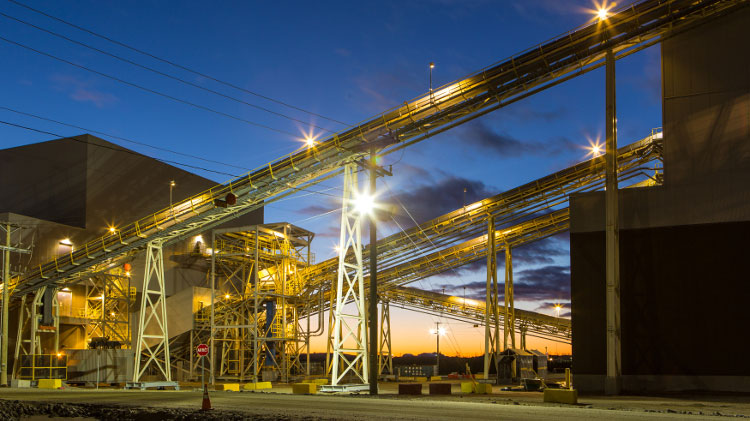
Power and productivity
As the cost of power has steadily risen over the past several years, mine operators have had to become more energy-savvy to keep the lights on
ICMM members adopt new measures to prevent future tailings dam failures
Tailings review from ICMM recommends increased emphasis on governance