Dewatering system providers are settling on different strategies to meet the challenge of pumping mine water with high solid contents. Courtesy of Technosub
More than one dewatering technology provider has noticed in recent years that mines are trying to pump out dirtier water than in the past. Some underground mines may be experiencing changing geology as they go deeper; others may have made a dollars-and-cents decision not to pre-treat water before pumping. Whatever the reason, mines and their suppliers have spent the last decade coming to grips with high solid contents of 10 per cent or more.
Tougher alloys
Bill Schlittler, mining market manager at Cornell Pump, said he had seen the hardness of dewatering pump materials evolve as mining customers sought to get more pressure out of one pump. Schlittler explained that large-diameter impellers, spun at high speeds, take more damage from suspended solids than lower-pressure pumps. To make these newer pumps more durable, Cornell built them with stronger materials.
The MX line of centrifugal pumps, introduced in 2011, can generate heads of up to 800 feet. MX pumps have a heat-treated ductile iron volute and an impeller made of stainless steel. Cornell followed up with the MP product line, which uses even harder steel with a high chrome content of 27 per cent. MP pumps can handle coarse abrasives of up to three inches in diameter.
“We just sold 20 pumps of the MP line to a major U.S. copper producer for a dewatering loop that they developed for draining water out of the ore body,” said Schlittler. “They saw up to 10 per cent solids.” The mine dewatering pumps the operator had used “were just wearing out, like, in a week.”
High-chrome alloys have a long history in slurry pump construction, but it is only in the last decade that they have seen widespread adoption in dewatering applications.
“We have seen a tremendous change in the wear resistance in the hydraulic end,” said Peter Uvemo, sales manager at Swedish company Grindex, which specializes in submersible electric pumps. As of 2007, Grindex has offered all of its pumps with its own version of the chrome alloy, trademarked as Hard Iron.
Harvinder Bhabra, global product manager of mine dewatering at Weir Minerals, said the company had also applied more of its materials technology to its dewatering range in the last four to five years. “Our product portfolio is constantly being updated to keep pace with industry demands. This includes our self-priming pumps, which have evolved from our traditional hard-iron wet ends to a chrome- iron alloy,” he said. “Similarly on our submersible pumps, potential weak spots have been reinforced by better materials in pumps used in dewatering applications where we might have a larger than expected solids content.”
In 2015, Weir added a pump to its Floway vertical turbine range – traditionally used on clear water applications – by adding the capability of handling fine solids up to 15 per cent by weight. “For a vertical turbine pump, that was unknown in the past,” said Bhabra. The vertical turbine slurry pump includes iron bowls with abrasion resistant coatings, hard coated shaft, patented bearing design, and a mechanical shaft seal designed to withstand abrasion wear.
Technosub, a company that provides high-head/low- to medium- flow dewatering solutions in Canada, addressed a different problem for certain customers. “We developed a special alloy for the mines in the Arctic where they work in permafrost, where classic high-chrome alloys show poor performances” said Patrick Martel, vice-president of engineering and innovations at Technosub. “They have a lot of problems with corrosion because they need to pump brine. Also, crystallization inside the pump is a major issue.”
It took about two years to develop a double microstructure stainless steel that would resist corrosion. In 2012, Technosub began selling pumps with the new alloy to Arctic customers. In 2015, it began selling into Saskatchewan potash mines that also needed to pump corrosive brine.
Water treatment
Technosub’s most prized innovation is not actually a pump. Treatment is an essential step in the process of mine dewatering – any water discharged must be safe for the environment. Technosub spent five years working on a simple clarification system for removing solids from water. In this treatment system – dubbed the MudWizard – the operator has only to insert a flocculant-filled tablet shaped like a hockey puck into a dispenser about once a week. “It’s so simple that anybody underground can manage it,” said Martel. “The water flows into that dispenser, and we have a decanting system on the other side. Then we pump the clean water to surface or recirculate it via our dewatering system, and the solid concentrate goes into a disposal area where it will be dehydrated.”
The 15 to 20 mines that have installed the MudWizard were previously settling out their solids in sumps that needed to be mucked out. Martel said the downside to running the system that way is that it requires production equipment that could be used elsewhere, and damages that production equipment with dirty water. On top of that, the pumps incur damage because sumps are often a low priority for maintenance.
In contrast, Technosub’s decanting system requires less maintenance. It does not draw power, either. The pressure from the pump that feeds it starts the settling process, and the clarification puck continues it. The puck itself is made from non-toxic potato and corn starch.
At what point exactly water should be treated is a question with diverse answers. David Willick, GE Mining’s commercial director for North America, made his preference clear.
“We treat this as a system, not a product,” he said. “Create an environment in the water before you pump it that’s going to protect the pumping system. And if there are solids, corrosive water, etc., treat it before you pump it.”
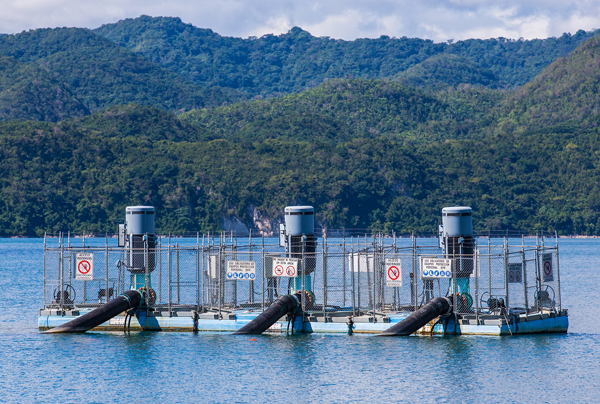
The demand from operations to recover water from tailings ponds, shown above, is growing, says Harvinder Bhabra of Weir Minerals. Courtesy of Weir Minerals
Low-hanging fruit
GE put that principle into practice when replacing a problematic dewatering system at a mine in Sudbury, Ontario. The original positive displacement pumps had frequent and heavy maintenance needs; GE’s solution has been running at 100 per cent uptime since installation in 2014, saving the mine operator more than $1 million a year in operating cost.
According to Willick, several different elements combined to generate the savings. First, mine water runs through a solid separation screen before entering the pump system. Second, the pumps installed were multistage centrifugal pumps that GE had already proven in its oil and gas division. Third, because the combined pressure of one multistage installation could add up to about 6,000 pounds per square inch, it was possible to pump 1,700 metres to the surface in one straight shot, obviating the need for multiple pump stations on multiple levels.
Willick said that GE customers had only begun to warm to this system in the last year or two. In a precariously low commodity price environment, optimizing system performance took on an allure it had not possessed back when meeting production targets was more of a concern than operational costs.
“In the past, if a solution wasn’t developed in mining, it was often dismissed as not applicable to mining,” said Willick. “What we’re finding today, is the realization of operators that they have to do things differently and therefore they have started looking outside to other industries and this case study is a classic example of such.”
GE is also looking at how innovations in adjacent industries can be deployed to the mining sector. Willick cites the example of advanced materials and nano coatings used in power generation turbines which could in turn be used to extend the life of pump impellers. “We call this approach, accessing the GE Store for technical expertise and solutions,” said Willick. “We apply knowledge and experience from other industries to new applications.”
The future of dewatering
A bit of innovation is also required to address an emerging challenge: in a time when environmental issues force mines to use their water efficiently, how can all that unwanted groundwater be put to best-use? Technosub and Weir are among the providers working with mines to recirculate the water they pump out.
“Rather than just pump water into the tailings pond like we used to, and just leave it there to settle out, we find that there is an increasing demand for that water to be reused in some form or other,” Weir’s Bhabra said. “We’re doing a lot of work with mining companies where we’re supplying them with pumps which are designed for dewatering, but they’re not dewatering in the true sense, but pumping it back to the mine, for reuse in the process. As well as the pumps we manufacture, we now supply barges that you’re floating out on the tailings pond with pumps on them. And they’re pumping the water back to the mine.”
In the dry mining climates of northern Chile, Weir has supplied several vertical turbine pumps, which circulate water back into mines from many kilometres away: an example of what, Bhabra jokes, they like to call re-watering.