Considering the current resurgence in commodity prices, every mining company should concentrate on strategy optimization to ensure that operations move from a cost-focused mindset to one centred on value maximization in order to reap the benefits of the upturn in the mining industry.
Recent advances in open-pit strategic mine planning software enable the optimization of intricate mining problems associated with a complex and vast array of parameters and constraints. These programs simultaneously optimize the mining sequence, cut-off grade selection, amount of mining equipment needed and capital expenditure to maximize the net present value (NPV) of a project or deliver on corporate goals. These modern techniques should be adopted at the strategic or life-of-mine planning level to ensure mines are developed in the most valuable fashion within the bounds of practical mining.
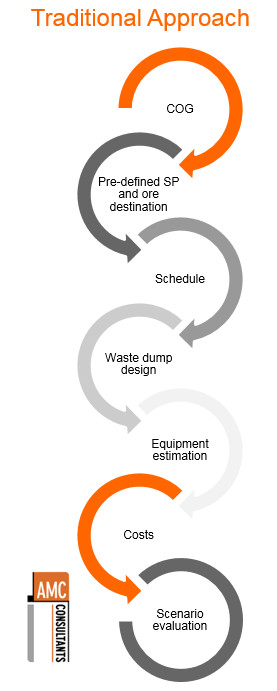 |
Traditionally, mine planning involves following a series of sequential processes to evaluate the merits of different mine planning scenarios. Typically, a mine plan is produced based on fixed cut-off grades and strives to achieve a primary goal, such as a target mill feed, while maintaining a smooth total material movement to simulate the operation of a pre-determined mining fleet. The mine plan is then used as a basis to calculate equipment hours and numbers. The latter form the input into cost models that calculate mining costs and overall project value. The process is repeated with different assumptions for total material movement, sequencing or cut-off grades. Once the mining engineer driving the mine plan is satisfied that an adequate number of scenarios have been evaluated, the best outcome is selected and used for the rest of the process such as waste dump and stockpile design.
The problem with this approach is that the entire process can be time-consuming, sub-optimal from a value perspective — especially when the operation being planned is complex — and heavily reliant on the mining engineer’s understanding of the deposit and their experience.
That is why the use of advanced mine planning software is becoming more widespread among mining companies and consultancies. Mixed-integer linear programming processes and advanced algorithms allow rapid evaluation of complex problems and help engineers and management make educated decisions regarding the best mine development or optimization strategy to adopt.
Related: Stochastic mine planning trial at Newmont's Twin Creeks mine shows value generation potential
The power of advanced mine planning software lies in its ability to achieve multiple targets while respecting a variety of constraints by looking ahead to ensure that the choice of mine development made in the first year of production, for example, does not jeopardize its ability to achieve targets in subsequent years and achieve optimum value. This is a vast improvement from a traditional approach whereby a mine plan is derived one period at a time.
Improving a project’s NPV can be achieved by applying variable cut-off grades by scheduling period. This is accomplished by defining grade bins based on the spatial distribution of the ore and grade tonnage curves. Advanced mine planning software can define a high-grading strategy that brings high-grade material to the processing facility earlier in the mine life while balancing the total material mined, and therefore the mining costs to do so. Following a high-grading strategy can typically result in a 15 per cent higher NPV compared to directly processing run-of-mine ore.
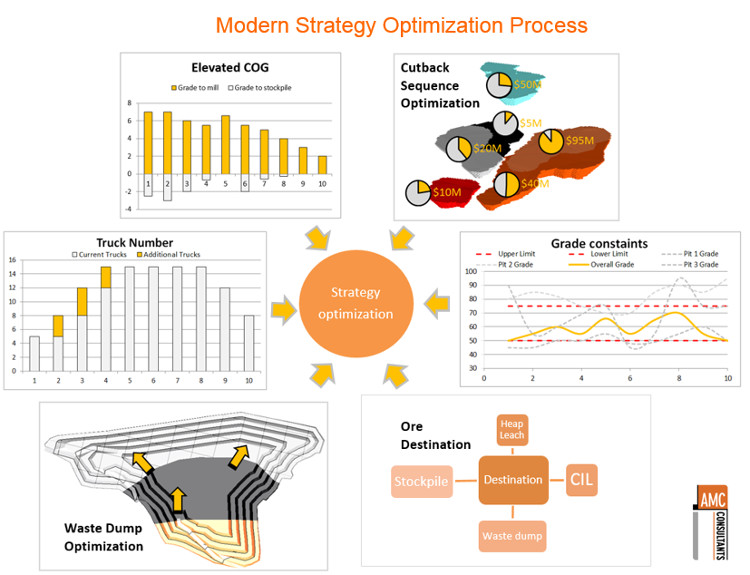
One of the issues with high-grading is that mining more material requires additional equipment. The impact of that cost can be evaluated within the software by accounting for equipment hours as a variable in the model. Assigning a capital cost to a larger fleet allows the software to gauge whether and when to increase production capacity to optimize the project’s NPV. Capital expenditure decisions are not limited to the mining fleet and can extend to evaluating the merits and best timing for increasing processing plant capacity or putting capital toward developing a new pit.
Optimizing project value becomes increasingly difficult for mining engineers when they must satisfy multiple targets or constraints. In iron ore deposits, for example, it is common to have to deal with stringent grade specifications and contaminant levels. Minimum and maximum grade constraints can be input to ensure the software respects them for the life-of-mine while achieving production targets and optimizing cut-back sequencing to obtain the highest possible project value.
These programs can also optimize the shape of waste dumps while simultaneously considering the aforementioned constraints or variables to maximize project value. Dump envelopes, representing the maximum possible waste storage capacity, can be imported into the software for evaluation. To generate hauling costs, the program uses cycle times from each mining block to each dumping block within multiple waste dumps. Subsequently, the hauling cycle times and costs help define the most suitable waste destination for each waste block to minimize hauling costs or level the hauling fleet over the project’s life.
Despite the advances in mine planning software, mining practicality still needs to be central to a development strategy. To avoid the “black box” solution effect that cannot be explained by the engineer, it is in the engineer’s best interest to produce multiple scenarios to demonstrate the incremental value generated and help tell the story behind the decision-making process.
These are only a few of the many applications of modern mine planning software that underlines how useful it is as a tool for mining companies to maximize the value extracted from their active mines or future projects.
Philippe Lebleu has extensive consulting and operational experience in the mining industry. He currently works as a principal engineer at AMC Consultants' office in Vancouver.
Got an opinion on one of our columns? Send your comments to editor@cim.org.