(This article was originally published in CIM Magazine’s March/April 2008 issue as part of the “Evolution of Shaft Sinking” series.)
The period between 1940 and 1970 can really be called the golden age of shaft sinking. It was during this period of time that a number of countries around the world set the shaft sinking records, which still stand today. Listed below are the shafts which were sunk at record-breaking speeds:
» January 1960: President Steyn #3 shaft (South Africa) – 1,020 feet (311 metres)
» March 1962: Buffelsfontein shaft (South Africa) – 1,251 feet (381 metres)
» September 1964: Staric main shaft (Czech Republic) – 1,053 feet (321 metres)
» April 1964: Proletarskaya (Russia) – 1,280 feet (390 metres)
» May 1969: 17–17 Bis mine (Ukraine) – 1,316 feet (401 metres)
Shaft sinkers from the Republic of South Africa generally claim to hold the shaft sinking record for their sinking project at the Buffelsfontein mine in 1962; however, as can be seen from the list above, both the Russians and the Ukrainians were faster.
The South Africans used much larger sinking crews than those in Europe or North America. Table 1 compares statistics on some of the shafts sunk during this period. Note the number of persons employed on the Buffelsfontein project.
Details on the Proletarskaya and the 17–17 Biz shafts are not available; however, the equipment and manpower utilized are probably similar to those of the New Boutoff shaft sinking a few years earlier.
Race to the bottom
Although the sinking rates of North American shaft sinkers do not compare with those achieved in South Africa and Eastern Europe, they are worth noting as they are faster than those currently being achieved. Some of the more notable sinking rates achieved by North American shaft sinkers in the 1950s and 1960s are as follows:
» November 1958: Shattuck Denn, Bardon Shaft, Utah – 392 feet (120 metres)
» January 1965: Alwinsal Potash (A.M.C. Harrison), Saskatchewan – 570 feet (174 metres)
» September 1966: Noranda Potash (A.M.C. Harrison), Saskatchewan – 620 feet (189 metres)
» November 1966: PCS Cory (Cementation), Saskatchewan – 640 feet (195 metres)
There were a number of inventions during this period that contributed to the increase in sinking advance rates – the mechanical mucking machine contributed the most to faster rates.
Perhaps the first mechanical mucking machine for the underground mining industry was the EIMCO rocker shovel loader, introduced in the United States in 1938. This particular model was not suitable for shaft sinking because it ran on rail. EIMCO, however, soon followed up the 12B model with the 630 model, which was crawler-mounted and therefore suitable for shaft sinking. The EIMCO 630 was not favoured by Canadian shaft sinkers, probably because it was not particularly suited to the benching method of blasting. In other countries, where the full face shaft sinking round was used, it has been utilized effectively up until the present day. It has been particularly popular in both the United States and the Republic of South Africa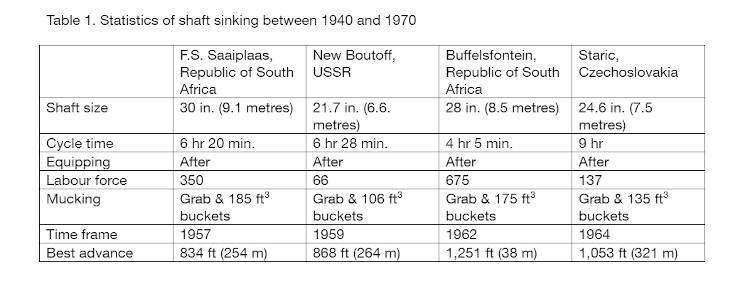
In 1943, the Riddell mucking machine was introduced in Canada and was immediately used with good success in the rectangular timbered shafts that were popular in Canada at that time. The Riddell worked much better than the EIMCO 630 for timber shafts, where the benching system of blasting was invariably used.
The Cryderman mucker was introduced in the late 1940s to Canadian shaft sinkers but did not find any real popularity until the early 1950s. Since that time, however, the Cryderman has been the mucking machine of choice for most Canadian shaft sinkers.
Grab and go
Certainly the clamshell or cactus grab type of shaft loader has been the most popular and commonly used shaft mucking machine, although not in North America. It was developed and used around the same time in both Eastern and Western Europe as well as South Africa.
In South Africa in 1949, a clamshell grab was successfully used for sinking a shaft at the Western Holdings mine. In 1952, the No. 2 shaft at the Vlakfontein mine was also successfully sunk using a one-ton capacity, pneumatically operated cactus grab.
In Europe, the development of a pneumatically operated grab for shaft mucking was also being developed at about the same time. This particular unit is very similar to those used in South Africa.
Although not an invention, this period also saw the movement away from brickwork shaft linings and their substitution with cast in place concrete linings.
It was also during this period that the South Africans developed their sinking system which incorporated a suspended curb ring, a multi-deck Galloway work stage and a concrete slick line that would allow installation of the concrete shaft lining concurrent with excavation being carried out on the shaft bottom below.
The pilot bit for the Beatrix No. 1 shaft is shown on the right with the reamer shown on the left
Concurrent sinking and lining had been carried out before but the multi-deck stage and the concrete slick line contributed to a more efficient system. This system was first used in the Republic of South Africa in the late 1940s and was later adopted by both Canada and the United States, as well as a number of countries in Western Europe. This system was first used in Canada in the latter part of the 1950s.
In Canada, perhaps the first use of a cactus grab mucking machine was in the Potash Company of America’s No. 1 shaft near Saskatoon, Saskatchewan. The shaft was first frozen and then excavated using conventional drill-and-blast techniques. Mucking was done with a cactus grab type loader mounted on the bottom of a four-deck work stage. The shaft was started in February 1956 and bottomed out at 3,450 feet (1,052 metres) in June 1958. This was a rather remarkable shaft in a number of ways – the depth of freezing, the use of a cactus grab and the use of a multiple deck Gallaway work stage suspended from the surface.
Rectangular timber shafts were much more popular in North America than in either Europe or Africa. In North America, because of good rock conditions and rather modest depths, rectangular timber shafts continued to be sunk in Canada until the 1980s. Both Europe and South Africa changed over to circular shafts much earlier.
In Canada, the benching round was popular for the sinking of rectangular shafts. A good sump was always available and cleaning the bottom prior to drilling was quick and easy. As well, the Cryderman mucking machine replaced the Riddell mucker in most cases. Satisfactory advance rates were in the range of 8 to 10 feet a day (2.4 to 3 metres). Patrick Harrison and Co. advanced the 10 by 21 foot rectangular shaft at the Millikkan Lake mine near Elliot Lake, Ontario, 440 feet (134 metres) in June 1957, for a daily advance rate of 15 feet or 4.5 metres. This may very well be the North American record for a rectangular shaft sinking.
Freeze frames
It was during this period as well that the first shafts were sunk in North America using the Poetsch freezing method. Two shafts were sunk in the early 1950s – the South shaft at the Potash Company of America’s mine near Carlsbad, New Mexico, and the Ojibway shaft at the Canadian Rock Salt Company’s mine in southern Ontario. The South shaft was frozen only to a depth of 107 metres but the Ojibway shaft was frozen to a depth of 329 metres. Both of these shafts were lined with concrete and neither utilized tubbing in the water bearing sections.
The first use of cast iron tubbing in North America, to seal off water-bearing sections of the shaft, was at the International Minerals and Chemicals’ K–1 shaft near Esterhazy, Saskatchewan. A 380-foot section of tubbing was installed between the 1,241 and 1,621 foot levels. The shaft was completed at a depth of 3,378 feet in 1961. Subsequently, 11 more tubbed shafts were sunk in the Saskatchewan potash basin along with two shafts with welded steel linings in the water-bearing sections.
The use of the rockbolt for temporary support was another major step forward in shaft sinking during this period. A number of different types of mechanical anchorages were developed for rockbolts in the 1940s. However, the time and expense in drilling holes for rockbolts negated their advantages. Up until 1945 drilling rock was still time-consuming in spite of almost a century of technological developments. In that year, a historic conversion from alloy steel to tungsten carbide-tipped drill steel took place in Sweden.
Originating in Germany in the 1920s, the development of tungsten carbide bits culminated in Sweden in the early 1940s. Secoroc started production on a small scale in 1940, and the first cemented carbide bit was produced in 1943. During the 1950s and 1960s development continued for extension drill rods. In the 1960s, drill steel manufacturing in Sweden was restructured, giving rise to two companies – Secoroc and Sandvik.
In 1948, the Alimak raise climber was introduced to the mining industry and in 1962, the first commercial raisebore machine was introduced. Using either one of these machines, if shaft bottom access was available, it was now possible to raise and slash a shaft handling the broken muck on the shaft bottom. Using this method of shaft sinking, advance rates could be increased if bottom access to the shaft was available.
Patrick Harrison
During this entire period, shaft sinking in Canada was dominated by one mining contractor – Patrick Harrison & Co. Ltd. The company was actually first established in 1934 in Val-d’Or, Quebec, and sank a number of shafts in that area. It was, however, the work carried out in the unstable ground conditions of the Quebec asbestos mines that established the company as a major force in North American shaft sinking. The majority of the shafts sunk in the Elliot Lake uranium boom were sunk by PH & Co. Seven frozen shafts were sunk in the Saskatchewan potash basin in a joint venture with a German consortium, and a huge contract was carried out to develop the Thompson nickel properties for Inco. At the time of the Thompson contract it was the largest underground development project ever let to a mining contractor. A total of 1,500 persons were employed. These are but a few of a total of 600 shafts sunk by PH & Co. in its relatively brief history.
Rotary drilling
It was during this period, as well, that the technology for the drilling of mine shafts using rotary drilling techniques took some giant leaps forward. Between 1961 and 1969, there was huge progress made in the drilling of shafts using modified oil field rotary drilling equipment. The biggest effort during this period was at the U.S. Nevada test site of the Atomic Energy Commission. Holes with diameters of 72 inches were drilled to depths of 4,200 feet. Some of these holes were completed in as little as seven months.
Besides the drilling at the Nevada test site, a number of other shafts were completed. In 1966, a 60-inch diameter shaft was completed for the Bunker Hill Company at its Higden mine in Missouri. In the same year, Kermac Potash Company completed an 8.5 foot diameter shaft to a depth of 1,650 feet. One of the deepest shafts drilled during this period was in 1969 when a 6,150 foot (1,875 metres) deep shaft 90 inches (2.28 metres) in diameter was drilled in the Aleutian Islands of Alaska.
Perhaps more important to shaft sinking were two shafts drilled in Holland at the Beatrix mine between 1955 and 1959. These shafts were 7.65 metres in diameter and just over 500 metres deep, drilled using the pilot hole and ream method whereby an initial pilot hole 2 metres in diameter is initially drilled and then enlarged in stages to its final diameter. The shafts were kept completely full of drilling mud at all times during drilling and a combination wall of steel and concrete was installed after the shaft drilling had been completed. The drilling of Beatrix II was started in August 1955 and completed in January 1959 – a total of 1,130 days, for an advance rate of approximately 0.45 metres per day. The installation of the lining required an additional 44 days.
During this period, shaft sinking rates again increased threefold from 30 to 40 metres per month to 90 to 110 metres per month.
ABOUT THE AUTHORS
Vern Evans was previously a general manager at Mining Technologies International. He is currently a senior consultant at Stantec.
Charles Graham was previously the managing director of CAMIRO Mining Division. He is currently retired.
REFERENCES
Brown, E.O.F. (1927). Vertical Shaft Sinking. London: Ernest Benn Ltd.
Dellinger, T. B. (1966). Current status of big hole drilling. The Annual Meeting of the American Institute of Mining, Metallurgical and Petroleum Engineers. New York: American Institute of Mining, Metallurgical and Petroleum Engineers.
Hynd, J.G.S. (1960). Shaft sinking through water bearing dolomite. Canadian Mining Journal, August, 74–76.
Jamieson, D.M., Pearse, M.P., & Plumstead, E.R.A. (1961). The evolution of shaft design and sinking technique in South Africa. Transactions of the Seventh Commonwealth Mining and Metallurgical Congress (Vol. 2, pp. 589-625). Johannesburg: South African Institute of Mining and Metallurgy.
Jansen, F., & Glebe, E. (1960). Shaft sinking in the West German coal mining industry. Proceedings of the I.M.E. Symposium on Shaft Sinking and Tunneling. London: The Institution of Mining Engineers.
Jaros, A. (1967). Shaft sinking methods in Czechoslovakia. In G.L. Colborne ( Ed.), Index ’67. Saskatchewan Industrial Exposition and Mineral Symposium 1967 (pp. 121-127).
McIntyre, J.T. (1949). Shafts of the New Consolidated Gold Fields Group. Symposium on Shafts and Shaft Sinking. Johannesburg: The Chemical Metallurgical and Mining Society of South Africa.
Smit, G.L. (1964). Sinking and commissioning of the Eastern Twin Shaft System at Buffelsfontein Gold Mining Company Limited. Presented at the Annual Meeting of the American Institute of Mining, Metallurgical and Petroleum Engineers. New York: Society of Mining Engineers of AIME.
Part 6 - Shaft sinking from 1970 to 2007: Mechanical excavation