(This article was originally published in CIM Magazine’s August 2007 issue as part of the “Evolution of Shaft Sinking” series.)
The sinking of mine shafts has been going on for thousands of years. The Egyptians mined gold as long as 4,000 years ago, and it is thought that the Persians, Greeks, and Romans learned their shaft sinking techniques from the Egyptians. Shaft sinking in the Egyptian period and early Roman period was carried out by prisoners of war and criminals, and conditions were terrible. Towards the end of the Roman period, prisoners of war became less available and working conditions improved dramatically. With the fall of the Roman Empire in the 5th century, shaft sinking and mining activity decreased substantially due to the instability in Western Europe. The social chaos and general economic instability persisted until the 11th century.
From 1100 – 1500 AD the status of the miner was much changed from Roman times. The trade of mining, which included shaft sinking, became a respected profession. Agricola, in his book De Re Metallica published in 1556, gives a number of references to shaft sinking. Advance rates at the end of this period were probably in the range of one to two metres per month.
The period from antiquity to 1600 AD covers a huge time period and many changes in civilization; however, from the early mining by the Egyptians, through Roman times, the Dark Ages, and then the Medieval period, very little changed as far as the techniques tilized for sinking shafts.
The origins of shaft sinking
The earliest miners sought flint for tools and weapons. Shallow shafts were commonly being sunk as deep as 300 feet or 90 metres in the chalk beds of northern France and southern England in the Neolithic period (8000 BCE to 2000 BCE). Their main excavation tools were wedges and picks made from deer antlers and shovels made from the shoulder blades of oxen.
During this early period, it is thought that the spoil from shaft sinking was hauled to surface in leather bags or wicker baskets, by one or two men. Fire setting was practiced for assistance in fracturing the rock and making it easier to remove with the primitive tools that were available at the time. Ventilation methods were also primitive, often limited to waving a canvas at the mouth of the shaft.
It is important to realize that the valleys of the Tigris, Euphrates, and Nile were home to the first metal-using cultures. Copper and gold were the first metals gathered in any quantity, with copper being particularly important. A civilization using considerable amounts of copper was established in Mesopotamia by about 3500 BCE and in Egypt by about 3000 BCE. Copper was used to make tools and weapons. From Egypt and Mesopotamia, the knowledge of metals spread across Europe. The copper based cultures of the world were replaced by cultures using bronze by about 1500 BCE. This development led to significant improvement in the quality of weapons and tools. Iron was not successfully smelted until about 1400 BCE.
Underground mining by the Egyptians was carried out over a wide area with two places in particular being well known—the Nubian Desert in northern Sudan and the Timna Valley in what is now Israel. The Egyptian miners who worked both the mines in Nubia and in the Timna Valley used metal chisels and hoes, and excavated very regular, circular shafts with footholds in the walls for moving up and down. Some of these shafts were over 30 metres deep. Mining operations in the Timna Valley peaked in the 14th to 12th centuries BCE. Egyptian miners of the day apparently wore loincloths, perhaps headbands and, if a prisoner, ankle manacles. An oil lamp was used for lighting. Fire quenching was the rock breaking method of the day. After heating, the rock was doused with water causing it to shatter and become easier to extract with the copper bars and wedges. Once removed, the broken rock was placed in baskets, which were carried on workers’ backs up the shaft via ladders and footholds cut into the rock walls.
The Greek historian Agatharcides, writing about 200 BCE, gives a vivid description of mining under the Egyptians. He speaks of fire-setting, breaking the rock with chisels, miners who wore candles on their foreheads, and of “overseers who never cease with blows.”
The Romans followed the Greeks as leaders of the then known world. Rome explored all around the Mediterranean for mineral wealth to support its rising empire. Shaft sinking and deep vein mining were recorded in Roman literature. Inclined or vertical shafts were necessary to provide access, ventilation, and a means of removal of the minerals. Shafts during Roman times were square, small (one to two metres), and braced with wood to prevent collapse. A shaft could be as deep as 200 metres.
From slavery to freedom
Shaft sinking techniques under the Romans were not very different from those the Egyptians employed earlier. Generally, iron tools were used to enlarge the fractures in the rock and assist in breaking it away from the face. Single and double-headed hammers were used in combination with pointed bars and wedges. Besides iron tools, the Romans used fire to fracture the rock for removal.
During the Egyptian and early Roman Empire, shaft sinking and mining in general was not a job people took voluntarily. Therefore, the shaft sinkers and miners were generally slaves, criminals, and prisoners of war. In the early days of the Roman Empire, conquests of new lands produced many prisoners of war who were available for work in shaft sinking and mining in general. Because slaves were plentiful, conditions in the mines were terrible. Later in the Roman Empire, when new slaves were less easy to obtain, they became more valuable. Beginning with the reign of Hadrian (138 AD), the Romans began to recognize a degree of individual ownership of mines and permitted the exploitation of some orebodies by free men. Roman labour laws were therefore passed that mandated conditions for the workers in the mines. Shafts and tunnels had to be adequately supported with timbers to prevent collapse. Miners were entitled to sleeping and bathing accommodations, food, and specific hours of work.
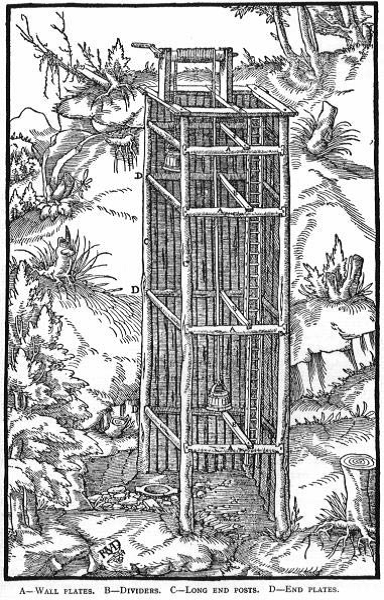
Detailed illustration from Agricola’s De Re Metallica: A. wall plates; B. dividers; C. long end posts; and D. end plates
By the standards of the time, some Roman shafts were quite deep. For example, the shafts at El Centenillo in Spain went down 650 feet.
Economic ups and downs
The fall of the Roman Empire in the West during the latter part of the 5th century was followed by widespread political and economic chaos that persisted in Europe for more than four centuries (The Dark Ages). The social chaos, incessant warfare, plagues, and general economic instability from the 5th to the 11th century resulted in a marked reduction in mining and therefore in shaft sinking.
With growing stability in the 12th to the 16th century, shaft sinking and mining activity increased. In central Europe the Avars, Czechs, and Saxons mined gold in Bohemia, Transylvania, and the Carpathians. This particular mining revival was led mainly by the Saxons and other Germanic peoples.
In 1168, silver was discovered near the town of Freiberg in Saxony. A silver rush spread across Europe in the late 12th and early 13th centuries, with strikes in Bohemia, Moravia, Hungary, the Alps, and Sardinia. To develop these mines, Saxon shaft sinkers were normally brought in. One of the greatest silver mines of all time was discovered at Joachimsthal in Bohemia in 1516. It was in this town that Agricola resided and his book on mining and shaft sinking is based on techniques employed in this area.
Early instruction manual
We have a fairly comprehensive picture of the most advanced mining and shaft sinking techniques of the 1500s from the book De Re Metallica written by Georgius Agricola.
Agricola describes the sinking process: “Now when a miner discovers a ‘vena profunda’ he begins sinking a shaft and above it sets up a windlass, and builds a shed over the shaft to prevent the rain from falling in, lest the men who turn the windlass be numbed by the cold or troubled by the rain."
"Now a shaft is dug, usually two fathoms long, one third of a fathom wide and thirteen fathoms deep; (1 fathom = 6 feet) but for the purpose of connecting with a tunnel which has already been driven in a hill, a shaft may be sunk to a depth of only eight fathoms, or at times fourteen more or less."
"There are two kinds of shafts, one of the depth already described, of which kind there are usually several in one mine; especially if the mine is entered by a tunnel and is metal bearing. For when the first tunnel is connected with the first shaft, two new shafts are sunk; or if the inrush of water hinders sinking, sometimes three are sunk; so that one may take the place of a sump and the work of sinking which has been begun may be continued by means of the remaining two shafts… The second kind of shaft is very deep, sometimes as much as sixty, eighty or even one hundred fathoms.”
Agricola also gives quite a detailed description of the types of linings used in the shafts sunk during that period.
“Now shafts, of whatever kind they may be, are supported in various ways. If the vein is hard, and also the hanging and footwall rock, the shaft does not require much timbering, but timbers are placed at intervals, one end of which is fixed in a hitch cut into the rock of the hanging wall and the other fixed into a hitch cut in the footwall. To these timbers are fixed small timbers along the footwall, to which are fastened the lagging and ladders. The lagging is also fixed to the timbers, both to those which screen off the shaft on the ends from the vein, and to those which screen off the rest of the shaft from that part in which the ladders are placed. The lagging on the sides of shaft confine the vein, so as to prevent fragments which have been loosened by water from dropping into the shaft and terrifying, or injuring, or knocking off the miners and other workmen who are going up and down the ladders from one part of the mine to another."
"If the vein is soft and the rock of the hanging and foot walls is weak, a closer structure is necessary; for this purpose timbers are joined together in rectangular shapes and placed one after the other without a break… The great weight of these joined timbers is sustained by stout beams placed at intervals, which are deeply set into hitches in the footwall and hanging wall, but are inclined."
"Further, in whatever way the shaft may be timbered, dividers are placed along the wall plates, and to these is fixed lagging, and this marks off and separates the ladder–way from the remaining part of the shaft.”
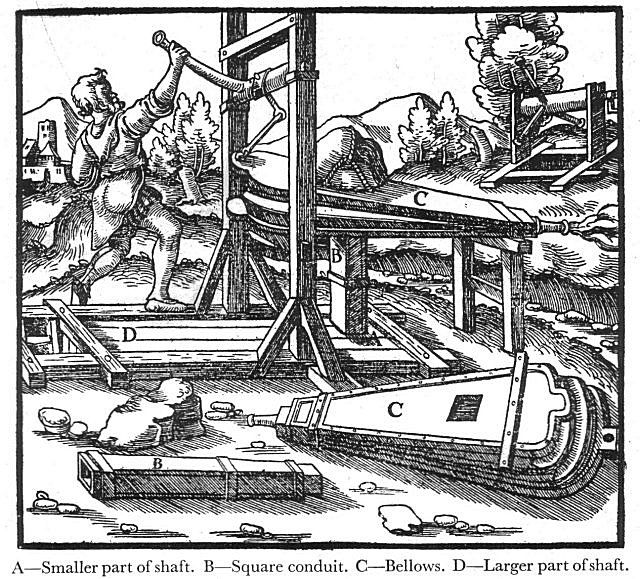
Ventilation methods: A. smaller part of shaft; B. square conduit; C. bellows; D. larger part of shaft (Agricola, 1556)
One of the most interesting developments in mining and shaft sinking was the growth in the miner’s status from the convict or slave in the Egyptian and early Roman times to a free man in the Middle Ages, often with substantial privileges. Miners in places like Frieburg, Goslar, and Joachimstal were exempt from military service and taxation. English tin miners had the right to prospect anywhere except in church yards, or on highways, orchards, or gardens. Such privileges and freedoms are a marked contrast to those of the miners under Egyptian or early Roman rule. As the Egyptians and Romans had done before them, the Czechs and the Saxons used fire quenching as a method of breaking the rock.
To summarize, the shaft sinking system utilized at the end of the 15th century would have been comprised of the elements found in the table. We are able to estimate sinking rates during this period at 1.5 metres per month.
ABOUT THE AUTHORS
Vern Evans was previously a general manager at Mining Technologies International. He is currently a senior consultant at Stantec.
Charles Graham was previously the managing director of CAMIRO Mining Division. He is currently retired.
REFERENCES
Agricola, G. (1556). De Re Metallica. New York: Dover Publications Inc.
Donaldson, F. (1912). Practical Shaft Sinking. New York: McGraw–Hill Book Company.
Habashi, F. (1994). "Georgius Agricola and his time". CIM Bulletin, 983, 82–88.
Hartman, H.L. (1992). SME Mining Engineering Handbook (2nd edition). Littleton: Society for Mining, Metallurgy, and Exploration Inc.
Temple, J. (1972). Mining—An International History. New York: Praeger Publishers.
Part 2 - Shaft sinking from 1600 to 1800: A skilled profession