The construction of the Nickel Rim South vent shaft. Mike Dupont/Courtesy of Cementation Canada Inc.
The two major developments in shaft sinking between 2007 and 2020 are the successes in mechanical excavation and the number of shafts sunk in China. To have four major mine shafts, over six metres in diameter and over 1,000 metres in depth, completely excavated with mechanical excavators and one additional shaft partially completed, is certainly noteworthy. Regarding the Chinese shaft sinking, we do not have the exact figures for the time period in question, but between 2000 and 2015, 1,092 completed shafts have been reported by Chinese shaft sinkers in both hard and soft ground. The advance rates in some of these shafts are similar to or better than those achieved in North America.
In addition to mechanical shaft sinking, there have been a number of other innovations that have been introduced since 2007. Perhaps the most important of these is the backhoe-type mucking machine.
Mechanical Shaft Excavators
During the time period under discussion, there were five shafts completed using mechanical shaft sinking equipment. Four additional shafts are currently under construction and an additional two are planned to start sinking in 2020. All these shafts were completed in soft to medium-hard ground. The shaft excavations that were completed during this period were:
» BHP Billiton – Jansen Production Shaft – 6.5 m diameter and 1,000 m deep.
» BHP Billiton – Jansen Service Shaft – 6.5 m diameter and 1,000 m deep.
» Eurochem – Uralkali Production Shaft – 7 m diameter and 549 m deep.
» Eurochem – VolgaKaliy #2 Production Shaft – 7 m diameter and 1,140 m deep.
» KGHM Polska Miedź – SW-4 Shaft – 7.5 m diameter and 1,216 m deep (The mechanical excavator was only used to a depth of 400 m.)
The four shafts that are currently under construction using mechanical shaft excavators are two potash shafts in Belarus, one shaft at a copper mine in Poland and a fourth shaft at a potash mine in Russia:
» Slavkaliy – Nezhinsky Production Shaft – 8 m diameter and 750 m deep.
» Slavkaliy – Nezhinsky Service Shaft – 8 m diameter and 700 m deep.
» Eurochem – Usolskiy Production Shaft #2 – 8 m diameter and 580 m deep.
» KGHM Polska Miedź – GG–1 Shaft – 7.5 m diameter and 1,340 m deep (The mechanical excavator was only used to a depth of approximately 500 m.)
The two shafts that are planned to start sinking using mechanical excavators are the two shafts being sunk to extract polyhalite in the United Kingdom.
» Anglo American (previously Sirius Minerals) – Woodsmith Production Shaft 6.75 m diameter and 1,594 m deep.
» Anglo American (previously Sirius Minerals) – Woodsmith Service Shaft – 6.75 m diameter and 1,565 m deep.
Of the shafts constructed using mechanical excavators, excavation has been completed on two of these, and two more are currently under construction using Herrenknecht shaft boring roadheader (SBR) machines. The remaining five shafts already constructed by mechanical excavators or currently under construction were excavated using shaft sinking excavators designed based on the Polish shaft excavators used in the KGHM copper shafts. The two shafts at the Woodsmith project, proposed to start excavation with mechanical excavators this year, are scheduled to use Herrenknecht SBR machines.
Herrenknecht SBR Shaft Excavators
The SBR was developed as part of Rio Tinto’s “Mine of the Future” program, a research and development project to advance more efficient mining technologies. It was subsequently chosen by BHP Billiton to excavate the shafts for their Jansen potash mine in Saskatchewan. The cutting system features a large roadheader cutting tool combined with a vacuum system to move the broken rock into a storage bin on the work stage above. From there, the muck is transferred to sinking buckets and hoisted to the surface. The Herrenknecht machines are massive – weighing more than 300 tonnes, and are suspended from the surface on winch ropes. Shaft lining is installed from the work decks above the excavator.
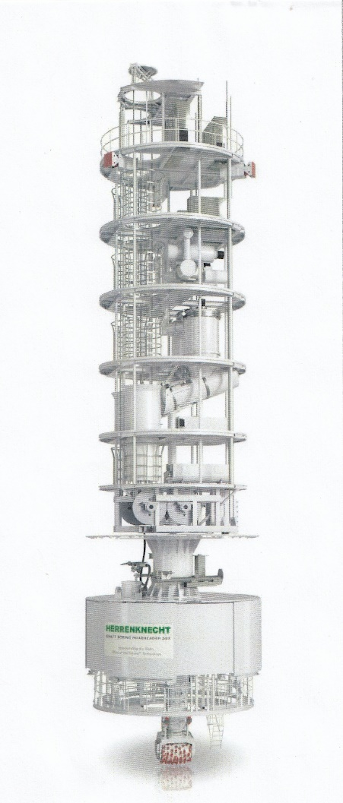
Herrenknecht shaft boring roadheader (SBR)
BHP Billiton – Jansen Shafts
The first of the two Jansen potash shafts excavated using prototype Herrenknecht SBR machines was started in December 2012. The second was begun in May 2013, with excavation in both shafts completed in April 2019. Both shafts were stopped in 2014 due to a geological problem that affected the temporary shaft lining. Another slowdown occurred when the SBRs encountered extremely hard rock at a depth of 470 metres.
Slavkaliy – Nezhinsky Shafts
The third and fourth SBRs were second generation machines and began sinking the shafts in mid-December 2018 and late January 2019. Shaft sinking in the upper 365 metres frozen section progressed at an average 2.2 metres per day, including start-up and learning curve. Tubbing was then installed in this section. Sinking in the lower section started in January 2020 and daily advance rates have been above five metres per day to date.
Anglo American – Woodsmith Shafts
The shaft collars have been completed at the Woodsmith project and the third generation Herrenknecht SBR excavators are on site. Shaft excavation is expected to commence in 2020.
European Mechanical Shaft Excavator
The Eurochem shafts and the KGHM shafts were excavated using a similar type of excavator that is commonly used at the KGHM copper mines in Poland.
The European shaft excavator is a much simpler design than the Herrenknecht machines. The excavator is suspended below the Galloway stage and mucking is carried out through the deck of the excavator using a cactus grab suspended from the Galloway stage above. The concrete lining and the cast iron tubbing rings are installed from the deck of the excavator.
The European excavators have one huge advantage over the Herrenknecht machines in that the changeover from mechanical excavation to drill and blast can be accomplished in a couple of days. Another advantage is financial, as the European excavator is considerably less expensive than the Herrenknecht machines.
The underside of a Russian shaft excavator shows the cutting mechanism of the boring machine used at the Eurochem shafts.
Eurochem – Usolskiy Mine
The service shaft was completed in October 2013, while the production shaft was completed in August 2014. Both shafts are lined with cast iron tubbing rings from top to bottom. One shaft was excavated and lined by the Russian contractor, US-30, using a mechanical excavator.
Eurochem – VolgaKaliy Mine
At Eurochem’s VolgaKaliy project, three shafts were sunk, all 7.5 metres in diameter and approximately 1,100 metres deep. All three shafts are completely lined with cast iron tubbing rings. Two of the shafts were sunk conventionally with the third shaft sunk using the same mechanized shaft boring machine as used at Usolskiy. The shaft boring machine achieved advance rates 50 per cent faster than the two shafts that used a drill and blast method. Since all of the Eurochem shafts were installed using a cast iron tubbing shaft lining, comparing advance rates to shafts with other types of lining is difficult.
KGHM – SW-4 Shaft
Sink preparations commenced in 2005 and the 7.5 metre diameter shaft was completed in 2013 to a depth of 1,216 metres. The shaft was frozen, and 470 rings of tubbing were installed in the shaft to a depth of 705 metres. The upper 400 metres of the shaft were excavated using a mechanical shaft excavator.
KGHM – GG-1 Shaft
The first bucket of muck left the shaft on December 2013. The shaft is 7.5 metres in diameter and 1,340 metres deep. The shaft was frozen, and 466 rings of tubbing were installed in the shaft to a depth of 700 metres. A mechanical excavator was utilized to a depth of approximately 500 metres, after which the shaft was advanced by drill and blast means.
Shaft Sinking in China
Due to the number of mine shafts sunk in the period under discussion, this aspect of shaft sinking is important to note. Certainly, the number of shafts sunk in China dwarfs the number sunk in any other region of the world.
The numbers in the table below are taken from a recent paper presented at the Shaft Design and Construction conference held in Toronto in 2019.

Statistics of shaft sinking in China 2000 to 2015
According to the paper, Chinese statistics of 2010 showed that there were approximately nine billion tonnes of ore mined in China that year, including 3.6 billion tonnes of coal. The ore was mined from 12,900 coal mines, about 6,500 metal mines and about 80,000 non-metal mines, with only five per cent of these being underground mines.
In 1957, the Beijing Institute of Mine Construction of China Coal Research Institute was set up to develop modern shaft sinking techniques and the use of mechanized mining equipment in China. There were several different shaft sinking systems developed for different ground conditions. Chinese shaft sinking seems to be based on European shaft sinking techniques. This would include the following:
» Twin single drum hoists
» Relatively short rounds – 3.5 metres.
» Concrete forms on the shaft bottom
» Umbrella type shaft drill jumbos
» Cactus grab mucking units
It would appear that the monthly shaft sinking advance rate is not far off North American rates and, in fact, some are considerably better. Below is a table illustrating some of the better rates achieved.
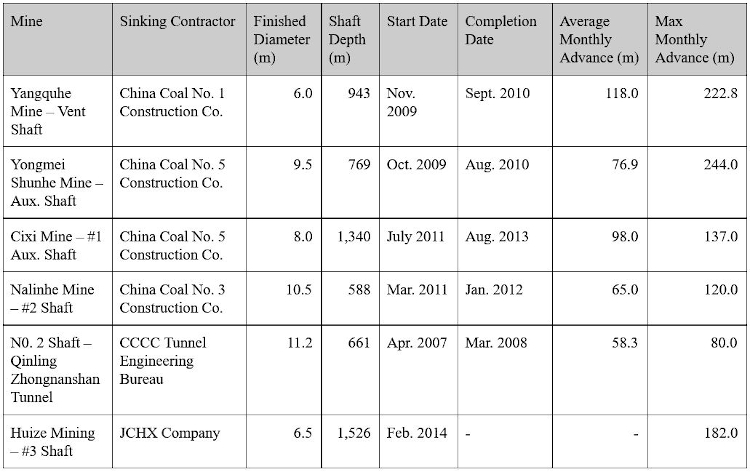
It was estimated by Long Zhiyang and Xiao Ruiling that China’s requirements, based on 2015 statistics, are 10 billion tonnes of ore annually, including four billion tonnes of coal. At least 100 mines will need to be built or expanded, which would result in 300 to 400 shafts in the short term. At least 70 per cent of these shafts would have to be in excess of 700 metres deep.
Further Shaft Sinking Innovations
Backhoe type mucking machines have been used as far back as the 1970s, but were never able to compete successfully with Cryderman type muckers used in North America or the cactus grab machines used in Europe and elsewhere. However, both the Cryderman muckers and cactus grab muckers are difficult to operate. Here in North America, it is currently difficult to find Cryderman operators and the timeline to train operators is long. The backhoe type muckers are extremely easy to operate. Redpath Mining Contractors and Engineers completed the Scissors Creek shaft and the two K3 shafts using backhoe type muckers and these are now being used in Mongolia by Redpath. It is important to develop this technology as backhoe type muckers could be automated to be operated remotely.

Typical backhoe type shaft mucking machine
Man-riding buckets have become popular lately and have been utilized on a number of recent projects. These are enclosed buckets, complete with doors and canopies. These buckets ride in the crosshead and are connected to the hoist rope in the same manner as the muck bucket. Muck buckets are removed, and man-riding buckets installed whenever man travel is necessary in the shaft.
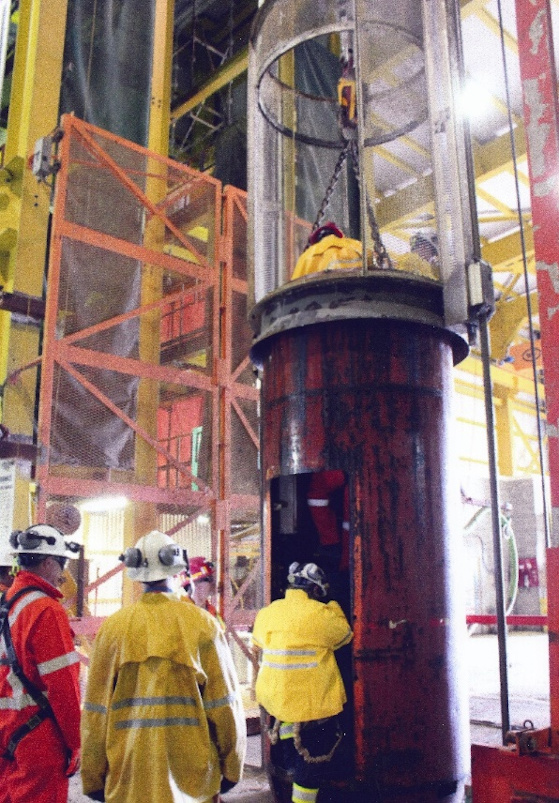
Man-riding bucket utilized at the Mosaic K3 shaft sinking project
The Way Forward
Neither the Herrenknecht SBR excavator nor the Polish/Russian shaft excavator are suitable for excavating in hard rock because of the cutting devices used. Pencil point tools, as used on the SBR machine and the European shaft borers, are limited by the strength of rock that they can cut. Hard-rock tunnelling machines use rotating disc cutters to perform in hard rock. Any shaft excavation in hard rock will also necessarily have to be carried out using rotating disc cutters.
Another shaft excavation machine that was developed by Herrenknecht in a partnership with Rio Tinto in the “Mine of the Future” program was what is now known as the shaft boring machine (SBM). Since that time, another shaft excavator, the shaft boring cutterhead (SBC), has been developed. Both are equipped with disc cutters, as opposed to the pencil bits on the SBR.
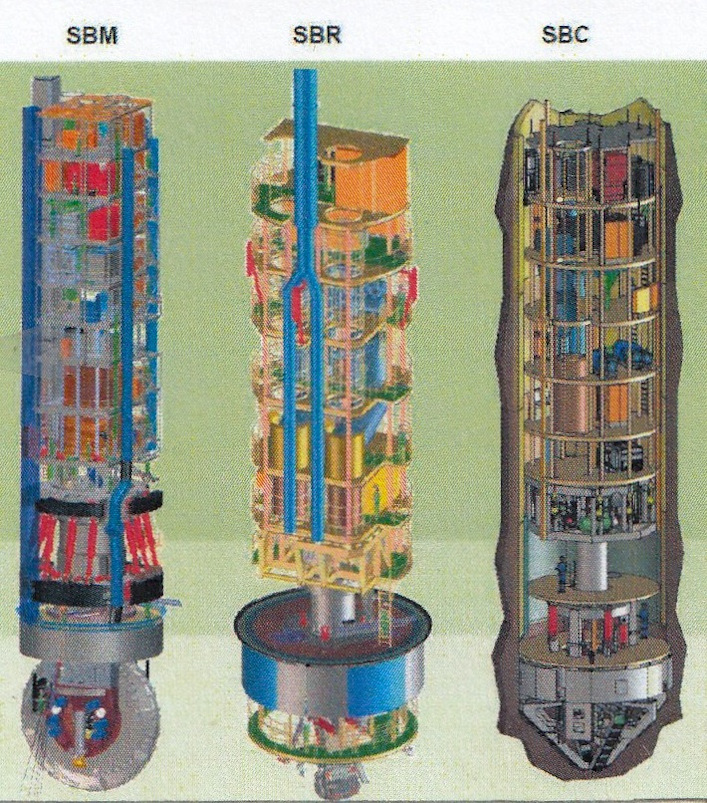
Herrenknecht SBM, SBR and SBC
The SBC has a conical-shaped cutterhead equipped with disc cutters. The cutterhead is submerged in water during the cutting sequence. The coarse material from the cutting sequence is removed utilizing the muck buckets, while the fine material is pumped to surface. Unless ground conditions are poor, the permanent shaft lining would be installed concurrent with excavation.
The SBC is 40 metres long and weighs 350 tonnes. It is supported from the surface by four shaft ropes installed on winches.
In a further effort to achieve a true hard-rock shaft excavator, in 2014 the Herrenknecht company partnered with Thyssen Schachtbau and Murray & Roberts Cementation to update and adapt the technology of the V-Mole shaft enlargers that were used successfully in the past, mainly in Europe, to enlarge a pilot raise bore hole to a much larger finished shaft. This machine has been named the Herrenknecht shaft boring extension machine (SBE).
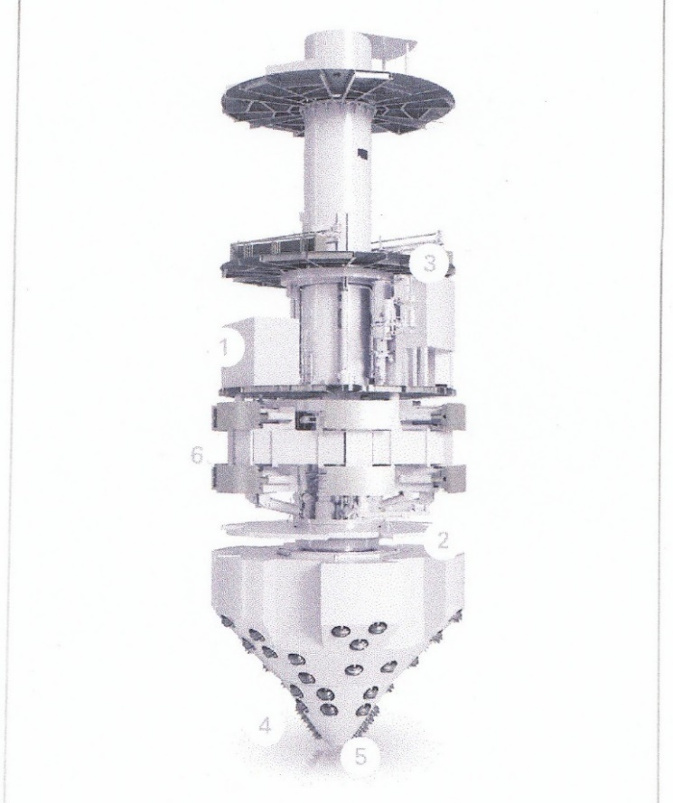
Herrenknecht shaft boring extension machine (SBE)
Herrenknecht points out that the hard-rock shaft excavation machines are not currently employed on any project.
Besides the Herrenknecht machines and those being used in Poland and Russia, the South African raise boring company Master Drilling announced in 2016 that it was developing a blind shaft boring system (BSBS). This machine, recently tested in South Africa, also uses single disc cutters.
At an advance rate of three metres per day, it is unlikely that the Herrenknecht machines are financially viable for most shaft sinking projects; however, at five or six metres per day the equation certainly changes. The European shaft excavators will probably not attain rates of five or six metres per day, but have proven themselves to advance more rapidly than drill and blast in the right ground. The fact that they can change back and forth between mechanical excavation and drill and blast makes them an important tool for shaft sinking in soft to medium-hard ground.
The Chinese appear to have made considerable progress in both their shaft sinking technology and advance rates. In the future these will probably continue improving, along with progress towards a safer sinking environment.
ABOUT THE AUTHORS
Vern Evans was previously a general manager at Mining Technologies International. He is currently a senior consultant at Stantec.
Charles Graham was previously the managing director of CAMIRO Mining Division. He is currently retired.
REFERENCES
Anon, (2014), Powerful New Version of a Proven Shaft Enlargement Technology in Mining, Herrenknecht Press Release, June, 2014.
Anon, (2019), Sinking for Show, International Mining, September 2019.
Anon, (2019), Sirius Minerals Project Factsheet – Shaft Sinking, Sirius Minerals Website.
Anon, (2018), That Sinking Feeling, International Mining, September 2018.
Anon, (2017), The Mosaic Company – The Next 50, YouTube, April 28, 2017.
Anon, (2013), Terex S20 Shaft Excavator at Scissors Creek, Canada, YouTube, April 04, 2013.
Bruemmer, K., (1979), Experience in Operating a Blind Shaft Borer with Hydraulic Muck Removal System, 1979 RETC Proceedings.
Burger, W., Neye, E. and Frey, A., (2014), Future Trends in Shaft Development, Tunnelling in a resource Driven World, Vancouver, TAC 2014.
Burger, W., Rauer, M., (2012), Mechanized Shaft Sinking Method for Soft and Medium Strength Rock, SME Annual Meeting, February 2012.
Frenzel, C., Burger, W., and Delabbio, F., (2010), Shaft Boring Systems for Mechanical Excavation of Deep Shafts, Australian Center for Geomechanics, May 2010.
Greinacher, J., Otten, F., (2019), Sinking of two Freeze Shafts Using Shaft Boring Roadheader (SBR) Technology for the Slavkaliy Nezhinsky Potash Mine in Belarus, Proceedings of the 4th International Conference on Shaft Design and Construction, November 2019.
Hagemann, B., (2014), Herrenknecht’s New Shaft Boring Enlargement Technology, Australian Mining.
Khan, A., (2015), Are Self-Levelling snd Self-Compacting Concrete Same, www.quora.com.
Long Zhiyang, XIAO Ruiling, (2019), Sinking Methods and Present Situation of Vertical Shafts in China, Proceedings of the 4th International Conference on Shaft Design and Construction, November 2019.
Lopez-Pacheco, Alexandra, (2020), A New Era in Shaft Sinking, CIM Magazine, February 2020.
Ming Jin Gu, Jian Fu Chang, (1987), Mechanization of Shaft Sinking of Metal Mines in China, Proceedings of the VI Australian Tunneling Conference, Melbourne, March 1987.
Rennkamp, P., Trodel, W., Fearn, (2019), A Case Study - Blind Shaft Sinking for BHP Jansen Project, Proceedings of the 4th International Conference on Shaft Design and Construction, November 2019.
Shaver, W., (2019), Shaft Sinking in the Next Five Decades, Proceedings of the 4th International Conference on Shaft Design and Construction, November 2019.
Slater, D., (2016), German Company Develops Four Machines for Blind-Shaft Construction, Enlargement, Mining Weekly, June 03, 2016.
Trodel, W., McIntyre, K., (2019), The York Project: Shaft Sinking Mission 2021 – Reaching Polyhalite, Proceedings of the 4th International Conference on Shaft Design and Construction, November 2019.