An illustration from Die Bergknappen depicting shaft sinking
(This article was originally published in CIM Magazine’s September/October 2007 issue as part of the “Evolution of Shaft Sinking” series.)
One of the early improvements to shaft sinking techniques during this period was the introduction of horse whims for the removal of material from the shaft bottom. This development occurred in the late 17th and early 18th centuries. A well-designed horse whim could remove material from the shaft bottom many times faster than windlasses operated by manpower.
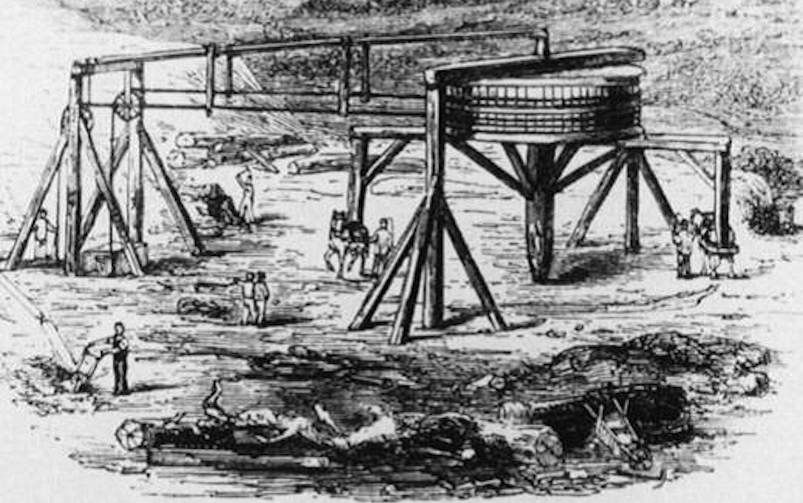
A whim, made up of a drum turned by horse power, and connected by rope to pulleys above the shaft transported buckets up and down.
Blasting
The second improvement to take place during this period was the replacement of fire setting with drilling and blasting. It took three centuries after gunpowder became known in Europe before some resourceful miner, probably in the late 1500s, thought to stuff some into the cracks in rocks, ignite it, and let chemistry do the work. Eventually, miners realized that if, instead of relying on natural cracks, they used an iron tool to make a deep hole with a small outer opening that could be plugged to confine the combustion gases, they could break even more rock. It is thought that the first use of blasting with black powder in mines was in Hungary in 1627. For various reasons, such as high cost, lack of suitable drilling tools, and fear of roof collapse, the use of black powder in mining and shaft sinking did not spread rapidly, although it was generally widely accepted by 1700.
One man swinging a four-pound hammer and holding his own drill rod was called single jacking. A two-man team was called double jacking. One man would swing a hammer that might have a nine pound head while his partner held the drill rod and rotated it in the hole. In average rock, one man might drill eight inches in an hour, while a two-man crew might make two feet. On average, it might take 40 to 60 holes, 1 to 11/2 inches in diameter, to be able to blast away enough rock to advance an eight foot by six foot shaft two feet. Drilling these 120 feet of holes might use up to 400 pieces of sharpened steel and require the better part of a week. Sometimes a third man was added, also with an eight or nine pound hammer, to further increase the drilling speed. For almost 250 years, this method of drilling blastholes was improved upon only in the composition of drill steels and the manner of tempering them.
Black powder was an extremely dangerous blasting medium. It had to be ignited either by flame or intense heat. The original fuse systems were thin lines of the powder itself or crude fuses made of straw, goose quills, paper, or other combustible material combined with sprinklings of powder. Burning speed of this type of fuse was extremely unreliable.
The New World
The first reference to blasting in America is contained in a committee report on the purchase of the Simsbury Connecticut copper mine for conversion into Newgate Prison in 1773. This report stated “by blasting rocks they had prepared a well-finished lodging room about 15 feet by 12 in the caverns and had secured the west shaft of the mine with a large door.”
The Spanish had discovered large reserves of both silver and gold in both Mexico and Peru in the late 16th century. In Mexico, a number of substantial shaft sinking projects were carried out in the latter part of the 18th century. Alexander von Humboldt visited these shafts and was full of praise for them in his Essai Politique sur le Royaume de la Nouvelle Espagne. “Over the mother lode, Obregon opened the shaft known as El Santo Cristo de Burgos, 493 feet in depth and later the hexagon Nuestra Senora de Guadalupe, which reached a depth of 1,130 feet. Lastly he dug the octagonal general shaft called Senor San Jose, with a perimeter of 88 feet and an eventual depth of 1,685 feet.” Humboldt called this last shaft one of the greatest undertakings in the history of mining.
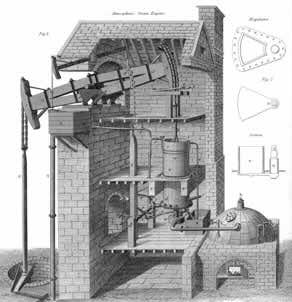
A Newcomen steam-powered water pumping engine
Technological advancements
A number of the improvements in shaft sinking techniques achieved during this period occurred near the end of the period with the Industrial Revolution. The date often given for the start of the Industrial Revolution in Britain is 1760. It was after this date that steam replaced muscle power as the primary power source in the mining industry. As early as 1689, English engineer Thomas Savery created a steam engine to pump water from mines. The Savery engine was very small and lacked sufficient power to be of much use in the mining industry. Thomas Newcomen, a Cornish engineer, was developing a steam-powered machine at the same time as Savery. Newcomen’s first steam-powered water pump was erected at a coal mine in Staffordshire in 1712. It was much more efficient than the Savery machine and raised 120 gallons a minute over a distance of 153 feet. Thomas Newcomen developed an improved version shortly after, and by 1769, there were 120 Newcomen engines operating in English mines.
James Watt made some improvements to the Newcomen engine and set up his own company building steam-powered engines. By 1800, the firm of Boulton and Watt had built 496 engines, of which 164 were employed for pumping water out of mines. Boulton and Watt also developed a steam-powered mine hoist, the first one of which was produced in 1784. Steam-powered mine hoists were to be in common use in the next period—1800 to 1900.
Along with steam engines being used to power pumps, the Industrial Revolution brought about the requirement for coal to power steam engines and other industrial applications such as mills and furnaces. Because the higher grade coal was to be found underground, it was accessed by shafts. Many of these shafts had to negotiate a heavy water bearing formation above the coal. To provide a waterproof shaft lining in these sections of shaft, cast iron shaft tubbing was used. In 1759, the first cast iron tubbing shaft lining was installed in a shaft in what is now Germany. Similar tubbing linings were installed in the Saskatchewan potash shafts in the 1960s and 1970s.
Miners gain recognition
Perhaps the most important reason for the improvement in sinking techniques during this period was the improvement in the status of the shaft sinker and miner alike. By the end of the 15th century, shaft sinking and mining in general had become a respected occupation. Particularly in the area of modern-day Germany, the Czech Republic, and Slovakia, shaft sinking techniques improved greatly. Mining became a skilled and valued profession. As early as the Middle Ages, miners in many European countries were freed from paying certain taxes, were allowed to carry arms, and did not have to serve as soldiers. A miner was also free to choose the mine in which he preferred to work. In England, as early as 1201, organizations of miners were protected from outside interference by the King of England himself.
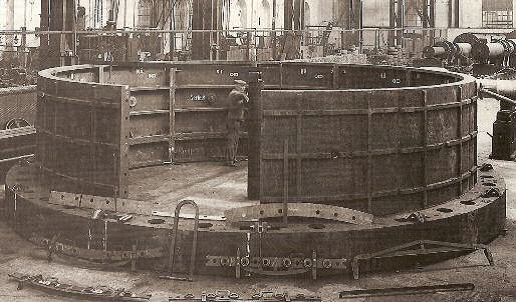
A typical tubbing ring
Universities and mining schools were opened where the techniques of shaft sinking and mining were taught and, in general, these techniques improved greatly during the period.
The purpose for the opening of these schools was to graduate engineers capable of developing and operating the mines which had become essential to the prosperity of the various countries in which the schools were located. Shaft sinking methods were an important aspect of the mining engineer’s education at this time because a successful shaft sinking project was essential in the development of mining properties.
Although published in the mid-1800s, the book Die Bergknappen, by Peter Heuchler, illustrates the typical life of a miner during the latter part of the 18th century.
Eduard Heuchler (1802–1879) published a number of books describing the life of a miner in the Freiberg area during this period of time. Heuchler started his career as a mining boy but then studied at Freiberg Bergschule (School of Mines) and subsequently at the Freiberg Bergakademie (Mining Academy). Later, he became architect and professor of civil engineering at the Freiberg Mining Academy.
It would also appear that by this time, shaft sinking was considered a separate occupation from mining. In a book published in 1708, The Compleat Collier; The Whole Art of Sinking, Getting and Working Coal-Mines, & c., As is Now Used in the Northern Parts, Especially Sunderland and Newcastle, the master sinker in the book speaks of using only experienced shaft sinkers. The reason for using experienced sinkers, as explained by the master sinker to the mine owner, are as follows: “Only experienced sinkers would be employed for if he [the sinker] be altogether unacquainted with this sort of sinking labour, he may lose his life by styth, which is a sort of bad, foul air or fume, exhaled out of some mineral, or partings of stone, and here an ignorant man is cheated of life insensibly; as also he, by his ignorance, may be burnt to death by a surfeit, which is another sort of bad air, but of a fiery nature like lightning, which blasts and tears all before it, if it takes hold of the candle… If $1,000 or more be spent in carrying down a pit or shaft almost to the coal expected, and then by an ignorant man should be blasted by a strong blast or surfeit, so that it may, as has been known, tear up your timber work and shatter the gins, and shake the stone-work or framework, so as to let in feeders of water, besides the destruction of the persons in the shaft, this would be a dismal accident with a witness, as well as loss of all labour and costs by ignorance.”
There are a number of references to sinking using hand drilling and black powder. Monthly sinking rates varied between 3.2 and 4.5 metres per month. It appears that a satisfactory sinking rate was between 3.0 and 4.0 metres per month. This was a fourfold increase over the advance rates of the previous period.
ABOUT THE AUTHORS
Vern Evans was previously a general manager at Mining Technologies International. He is currently a senior consultant at Stantec.
Charles Graham was previously the managing director of CAMIRO Mining Division. He is currently retired.
REFERENCES
Chadwick, R. (1983). “Copper: the British contribution.” CIM Bulletin, 76, (858), 84–88.
Habashi, F. (1997). “The first schools of mines and their role in developing the minerals and metals industries – Part 1.” CIM Bulletin, 90, (1015), 103-114.
Heuchler, E. (1857). Die Bergknappen. Essen: Verleg Gluckauf GmbH.
J.C. (1708). The Compleat Collier: The Whole Art of Sinking, Getting and Working Coal Mines, & c As Is now Used in the Northern Parts, especially about Sunderland and Newcastle. London: Printed for G. Conyers at the Ring in Little-Britain.
Morhard, R. (1987). Explosives and Rock Blasting. Maple Press Company.
Paul, W. (1970). Mining Lore. Portland: Morris Printing Co.
Preito, C. (1973). Mining in the New World. New York: McGraw–Hill Book Company.
Part 3 - Shaft sinking from 1800 to 1900: Cousin Jacks