Projects
Taking a shortcutGoldcorp and Redpath blaze an underground trail to connect mine to mill at Red Lake
Goldcorp and Redpath blaze an underground trail to connect mine to mill at Red Lake
November 11, 2014
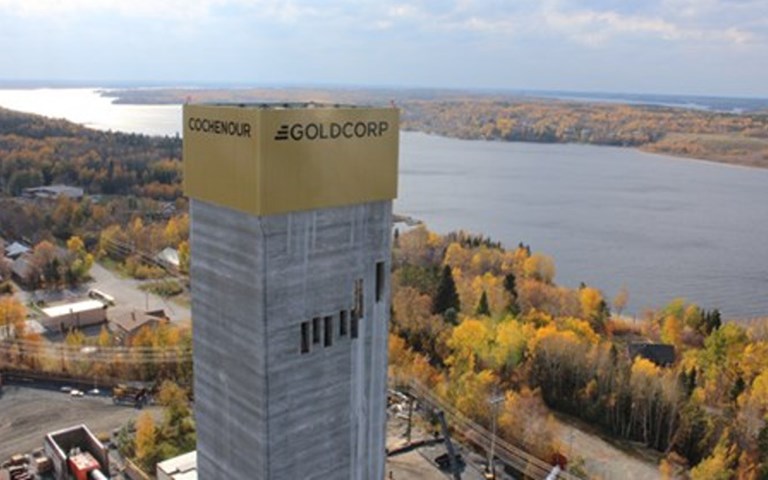
Goldcorp’s Cochenour headframe | Courtesy of Goldcorp
This is NOT A PAYWALL To access CIM Magazine, please create a free account
(Note that by creating an account you are not signing up for a CIM membership.)
If you are a CIM member or have already signed up, click here to log in
If you already have a CIM account, please enter your username (often your email) and your password.
If this is your first time here, you can create a free account
More Projects
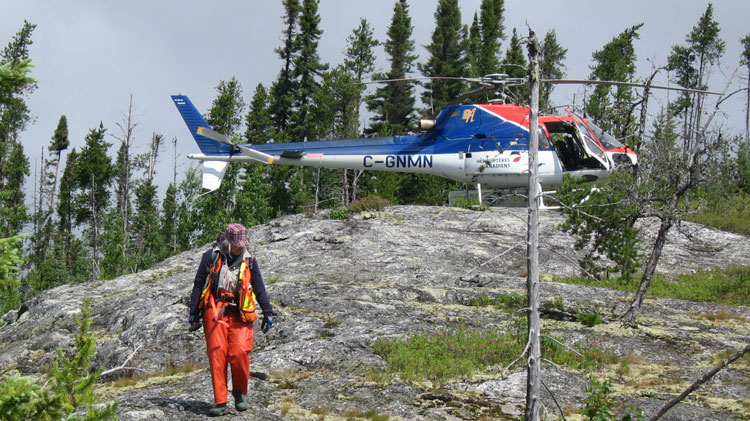
Quebec’s golden pockets
Exploration is stagnant around most of the world, but Quebec’s gold camps in the Abitibi and James Bay regions offer a ray of light in an otherwise dark tunnel
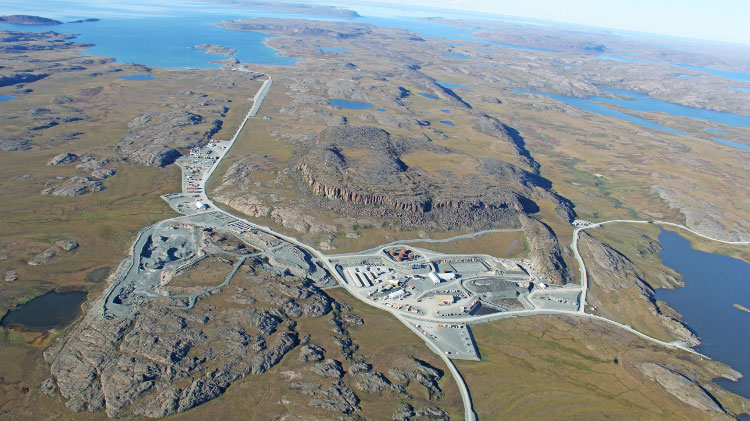
Hope for the future
TMAC’s high-grade Hope Bay gold project in the Kitikmeot region of Nunavut is nearing start up