Technology
Charging aheadThe move to battery-powered underground mining fleets is gathering speed. It is also opening up miners to a new realm of possibility.
The move to battery-powered underground mining fleets is gathering speed. It is also opening up miners to a new realm of possibility.
April 23, 2018
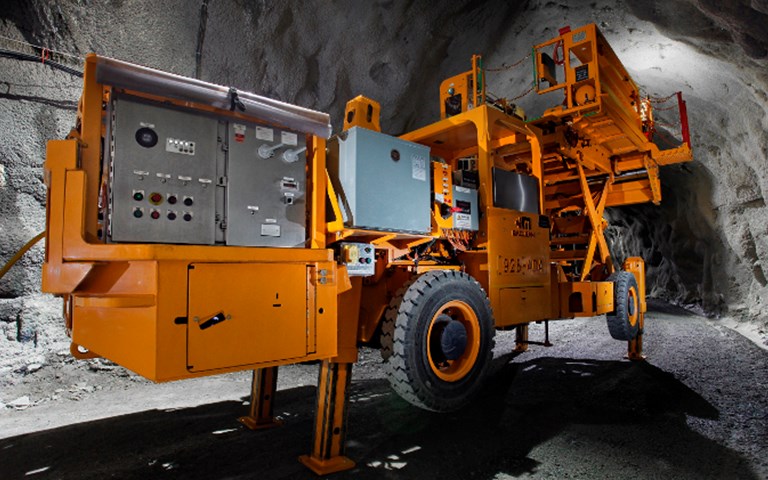
MacLean Engineering now offers a suite of non-ore-moving electric vehicles, including the 975 Omnia Bolter. Courtesy of MacLean Engineering/James Hodgins
This is NOT A PAYWALL To access CIM Magazine, please create a free account
(Note that by creating an account you are not signing up for a CIM membership.)
If you are a CIM member or have already signed up, click here to log in
If you already have a CIM account, please enter your username (often your email) and your password.
If this is your first time here, you can create a free account
More Technology
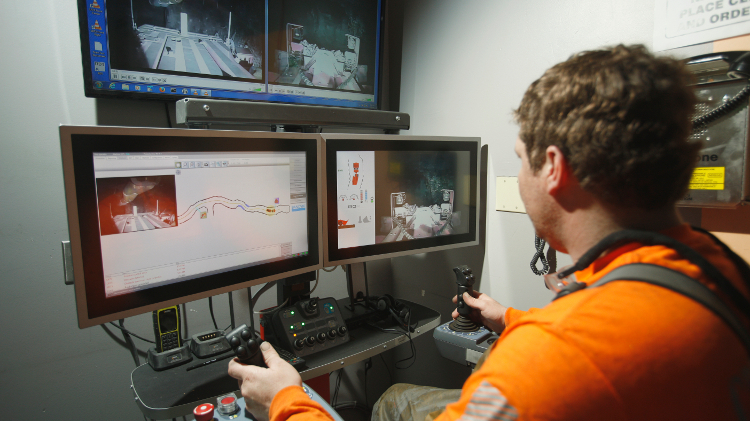
The automation revolution
There is no doubt the future of mining is automation. But what does that look like, and how will we get there?
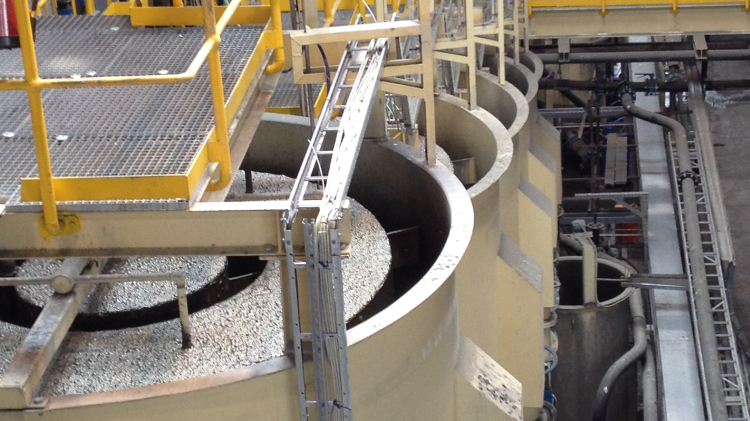
The future of flotation
Buoyed by pressure to cut costs and improve recovery, new flotation technologies are on the rise