(This article was originally published in CIM Magazine’s February 2008 issue as part of the “Evolution of Shaft Sinking” series.)
Mine shafts sunk during 1900 to 1940 in North America were almost all rectangular, timbered shafts while in Europe nearly all were circular and lined with brickwork or concrete. The reason for this was ground conditions. The majority of North American shafts were sunk in hard, competent rock. In Europe, on the other hand, the majority of the shafts sunk were in soft sedimentary rock, often with major water-bearing strata.
This was a busy period for shaft sinkers in a number of areas in the world. In the Ruhr district of Germany alone over 200 shafts were sunk: 124 shafts from 1904 to 1914; 71 shafts from 1915 to 1932; 13 shafts from 1933 to 1940. This was also an exciting time for the Canadian mining industry, with many of the famous mining camps opening up from 1900 to 1940.
Canadian rush
After the discovery of silver in Cobalt, Ontario, in 1903, prospectors ranged widely over the Precambrian areas of Ontario, Quebec, Manitoba, Saskatchewan and the Northwest Territories. In Ontario and Quebec, Abitibi and Larder Lake were discovered in 1906, Porcupine in 1909, Swastika in 1910, Kirkland Lake in 1911, Matachewan in 1916, Rouyn-Noranda in 1924 and Red Lake in 1925. In Manitoba, the Rice Lake district was discovered in 1911, and in the Northwest Territories the deposits in the sediments in the Yellowknife area were discovered in 1933 and those in the greenstones in 1935. In Saskatchewan, the Box and Athona mines were discovered in 1934 and three shafts were sunk at these properties in the La Ronge gold belt.
In British Columbia, bedrock gold deposits first attracted attention in 1863 during the first great placer gold rushes in the province. Little work was done on any of the discoveries and most were forgotten. The Barkerville area was prospected in 1860 and some mining was done in 1876 and a few years thereafter. Largescale mining, however, did not commence until 1933 and 1934 at the Caribou Gold Quartz and Island Mountain mines. In 1897, the Cadwallader gold belt in the Bridge River district, containing the Bralorne and Pioneer deposits, was prospected, but it was not until 1928 that the Pioneer mine was brought into production, followed in 1932 by the Bralorne mine. The Premier mine in the Stewart district was brought into production in 1918 and the Zeballos gold belt on the west coast of Vancouver Island was discovered and developed starting in 1934.
In addition to all this shaft sinking activity, coal mining continued to attract attention in Nova Scotia, and over 100 new coal mines were opened in that province during the 1900 to 1940 period. Shafts in this area tended to be relatively shallow, however, generally less than 800 feet deep. This is in comparison with the McIntyre No. 11 Shaft that was sunk to a depth of over 4,000 feet in the Precambrian rock of Ontario. All in all, it is estimated that over 400 shafts were sunk in Canada during this time.
Electric hoists
Late in the 19th century, gold had been discovered in the Johannesburg area of South Africa, and from 1910 to 1948, 341 rectangular, 41 circular and seven elliptical shafts were sunk.
The introduction of compressed air and electrical power into mines at the beginning of the 20th century had a great impact on shaft sinking practices.
By the start of the Great Depression, miners and shaft sinkers alike celebrated the industry’s embrace of the electric hoist for most types of shaft work. Machinery makers had ironed out the wrinkles in the technology experienced by the mining industry during the 1900s and 1910s and by the 1930s were producing a variety of single and double drum models for shaft sinking and ore production. For removal of the broken rock from the shaft bottom, either sinking buckets or sinking skips were used.
New drills
In the early 1900s, drilling was revolutionized by the introduction of lightweight rock drills. Up until that time, the drills used for shaft sinking were still large and heavy and required some type of support to be used efficiently. The jackhamer, introduced by the Ingersoll-Rand Co. in 1912, was a high point in the evolution of drilling equipment. This hand-held machine with automatic rotation was easier to handle and more reliable than earlier models. It was used along with hollow drill steel, through which air and water could be directed to clear the hole of cuttings. This drill revolutionized downhole drilling and eased the lot of the shaft sinker. It likewise sounded the doom of the heavy tripod-mounted drills used up until that time. By 1921, the jackhamer was manufactured in five different sizes.
Although there was a huge improvement in the drills themselves used for sinking, there was no major change in the quality of drill steel. Without carbide inserts in the drill steel rill, it became dull very quickly when sinking in hard rock. Drill steel was usually sharpened onsite, either by hand or with a sharpening machine. This made a blacksmith an integral part of the sinking crew.
A number of drill rounds were used in shaft sinking. Common in most of the world was a full-face pyramid cut; however Canadian shaft sinkers preferred a different type of round – the bench round. This round involved blasting only half of the shaft at a time. The bench round had a number of advantages. It always provided a good sump and facilitated “cleaning bottom”. It also facilitated the hand-mucking process.
Nitroglycerine-based explosives were used for blasting, usually with electric caps. Mucking was by hand into relatively small 2.5 to 4-ton buckets.
In Canada, the benching method of excavation generally caused the blasted rock to be piled up at one end of the shaft. To ease the labour of hand mucking Canadian shaft sinkers generally placed the bucket on its side and scooped the majority of the muck into the bucket. After the bucket was filled as full as possible in this manner, it was picked up into a vertical position and the remainder of the bucket filled in a normal manner. This system speeded up mucking and also made it easier for the shaft sinkers.
A light-weight shaft sinking drill
This system of mucking contrasted sharply with the system used in South Africa where a full face round was blasted. In that country, the bucket was kept vertical on the shaft bottom and filled by a large crew of muckers. In Europe a full face round was commonly blasted as well, but mucking was carried out in a similar manner to South Africa but with far fewer persons.
There were a number of innovations during this period that speeded up the hand-mucking cycle. Hand mucking into a large open-sided bucket that was then hoisted up with an air tugger to fill a car was a precursor to the mechanical shaft mucker that was to be developed in the 1940s.
The installation of shaft lining, whether it be timber in a rectangular shaft or brickwork in a circular shaft, was installed in the same manner as had been used in the previous period. In the case of timber shafts, the new sets were installed from a platform, usually referred to in Canada as a blasting set, which hung beneath the last timber set. In the case of a circular shaft, the brickwork or concrete was installed from a one- or two-deck moveable platform suspended from the surface.
Contract labour
Shaft sinking in both Europe and North America during this period was nearly always carried out by contractors. This contrasted with South Africa where the mining companies generally sank their own shafts.
One important event occurred during this period that was to affect shaft sinking in Canada dramatically in the next period of time – the arrival of Patrick Harrison in Canada. Born in Belfast just after the turn of the century, “Paddy” Harrison emigrated to Canada in 1921. After working as a miner and shaft sinker for a number of years, Harrison became a mining contractor in 1934. His first shaft sinking contacts were in the Val-d’Or area of Quebec. His company, Patrick Harrison & Co., was to dominate shaft sinking in North America from its inception in 1934 until its demise in the 1980s – sinking almost 600 shafts during that period.
Illustration of a bit sharpener used during 1900-1940
Typical manpower in a 13 by 26-foot rectangular shaft sunk in North America is listed by Donaldson in Table 1.
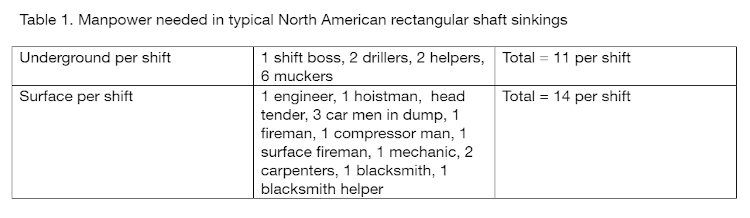
Statistics are given for several shaft sinkings in Wales. Daily advances of completed shaft varied from 1.8 to 6.6 feet per day, with the average sinking speed seeming to be in the range of three to four feet per day or 90 to 120 feet per month (27 to 37 metres per month).
In North America, shaft sinking advance rates were somewhat less than Europe, and the majority of the shafts were rectangular and timbered. Sinking progress under normal conditions ranged between 60 and 80 feet per month (18 to 24 metres per month).
South Africa's shift
In South Africa, sinking speeds were somewhat greater at an average of 135 feet per month (41 metres). The record shaft sinking rate in South Africa in 1900 was 203 feet in one month. By the end of the period, the record sinking advance rate had increased to 454 feet in one month.
A good description of shaft sinking in South Africa at the end of this period is given by C.B. Jeppe in his book Mining Practice on the Witwatersrand:
"Immediately the shaft is clear of fumes from the previous blast, the new shift begins operations. The shaft sinker, with his helper and 6 to 10 natives, go down the shaft, which they examine, clearing off any loose rock from the timbers. From the manifold platform, they examine and bar down the sides of the shaft to the shaft bottom; this usually takes 15 to 30 minutes."
"The rest of the native shift (45 to 60 natives) is then lowered and after watering down the broken rock and wall and walls, lashing is started. The “lasher boys” are placed to the best advantage for servicing the skips or buckets, which are first filled by hand with the larger rocks; special natives are detailed to break up, with 14 lb. hammers, rocks which are too large for handling."
"…When the shaft bottom has been cleared of rock, the lashing gang with their gear of shovels, picks and hammers, are sent to surface, the lashing operation taking usually from 4 to 5.5 hours."
"When the shaft has been cleaned and blown over and all misfires have been blown out, and all old holes plugged and excess water removed, drilling starts with the machines and drill steel, which have been sent down shortly before this. The drilling usually takes between 1 and 1.5 hours. … Charging up of the holes is then started, taking usually from 30 to 60 minutes."
In South Africa, at that time, regulations were that the shaft timber sets were to be kept within 50 feet of the shaft bottom. As the normal distance between sets was seven feet six inches, normal procedure was to install two sets per day. Procedure as laid out by Jeppe was as follows:
"Two timbermen and 12 to 16 natives can normally lower and swing one set in about half an hour, or two sets in 1 to 1.25 hours. The operation is carried out either on the morning or afternoon shift, whilst the shaft bottom is being drilled off. The installation of guides is also done during the drilling period, but on another shift by two more timbermen with their natives."
Although the mechanical excavation of shafts using rotary drilling techniques was not a popular alternative during this period, several mine shafts in Germany and Holland were excavated using these techniques. In the 1920s, the Germans were able to drill shafts up to nine feet (2.7 metres) in diameter to a depth of 425 feet (130 metres).
As with the previous periods, this period saw a huge increase in shaft sinking advance rates – from an average rate of 10 to 12 metres per month to 30 to 40 metres per month – a threefold increase.
ABOUT THE AUTHORS
Vern Evans was previously a general manager at Mining Technologies International. He is currently a senior consultant at Stantec.
Charles Graham was previously the managing director of CAMIRO Mining Division. He is currently retired.
REFERENCES
Brown, E.O.F. (1927). Vertical Shaft Sinking. London: Ernest Benn Ltd.
Donaldson, F. (1912). Practical Shaft Sinking. New York: McGraw-Hill Book Company.
Peele, R., & Church, J.A. (1941). Mining Engineers’ Handbook. New York: John Wiley and Sons, Inc.
Jaimieson, D.M., Pearse, M.P., & Plumstead, E. (1961). The evolution of shaft design and sinking technique in South Africa. The Seventh Commonwealth Mining & Metallurgical Congress (pp. 1-34). Kitwe: Northern Rhodesia Section of the Seventh Commonwealth Mining and Metallurgical Congress.
Jeppe, C.B. (1946). Gold Mining on the Witwatersrand. Johannesburg: The Transvaal Chamber of Mines.
Higham, S. (1951). An Introduction to Metalliferous Mining. London: Charles Griffin & Company Ltd.
McIntyre, J.T. (1949). Shafts of the New Consolidated Gold Fields Group. W.E. Gooday (Ed.), Symposium on Shafts and Shaft Sinking (pp. 197–272). Johannesburg: The Chemical Metallurgical and Mining Society of South Africa.
Jansen, F., & Glebe, E. (1960). Shaft sinking in the West German coal mining industry. H.E.
Collins (Ed.), Proceedings of the Symposium on Shaft Sinking and Tunnelling, the Institution of Mining Engineers (pp. 139-168). London: Andrew Reed & Co. Publishers.
Part 5 - Shaft sinking from 1940 to 1970: The golden age